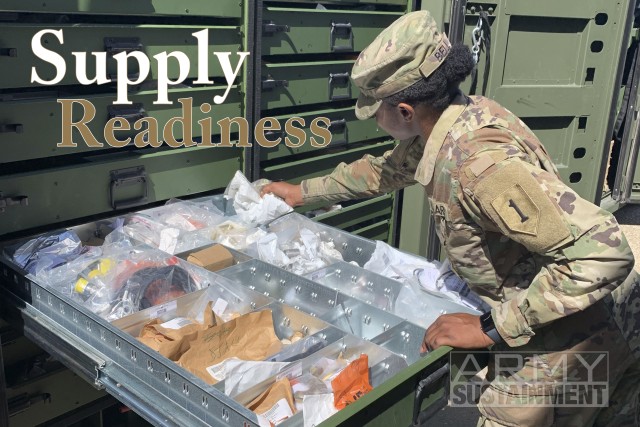
Proper supply chain management is a catalyst for readiness and directly influences an armored brigades combat team’s (ABCT) ability to fight and win our nation’s wars. An M1 Abrams tank becomes non-mission capable due to a failed transmission. A replacement is put on order and, being in stock, an immediate release is performed at the supporting supply support activity (SSA) utilizing the materiel release point process. Within hours, that company’s combat capability is back at 100%. This success story could have gone differently, dependent on the SSA’s organization, processes, use of their Common Core Authorized Stockage List (CCASL), the supply heartbeat of any brigade combat team.
Purpose and Concept
Army Materiel Command (AMC) began implementing CCASL several years ago to replace the legacy SSA Authorized Stockage List (ASL), creating an identical standard in terms of material, organization, and transportation for all similar brigades across the Army to model. Prior to CCASL, each brigade had autonomy to develop their own ASL dependent on their unit needs. While this was more flexible to unit mission, it decentralized ASL management and hindered transitions between brigades during combat operations. With the creation of CCASL, AMC created Army-wide familiarity by having identical lines of ASL and containers between armored brigades, increasing the brigade’s overall equipment readiness by enabling immediate support to the unit with the right maintenance-significant parts measured through accommodation and fill rates. To ensure the right items were stocked, historical needs of the equipment and parts are analyzed through an authorized-to-forecast (ATF) review and demand analysis to determine which required parts the supporting SSA should keep on hand. As consumption occurs for the material items and the safety stock is reached, Global Combat Support System-Army (GCSS-Army) automatically orders the consumed quantity to ensure that the ASL item is always in stock before the next shipment comes in.
History
1st ABCT, 1 Infantry Division (1/1 ABCT), Fort Riley, Kansas conducted its CCASL conversion from August 2017 to June 2018. The impacts were immediately felt as the brigade moved from its non-standardized ASL, of 2,200 lines stuffed into field pack units and steel quadcon containers, to the more versatile, structured, and organized CCASL. The conversion was no simple task. Over 2,000 additional lines were added to the SSA’s footprint, each having to be carefully cataloged, organized, and stored. This organization was accomplished through implementation of AMC’s planograph—a document that out-lined where items were to be placed amongst the storage containers and flat racks. Each of the more than 4,200 lines had to be checked, stored, and updated in GCSS-Army before it could be marked as complete. The planograph also directed the lines be stored in eighteen 20-foot BOH storage containers, each with internal sliding compartments designed for effective organization. Thirty-five Container Roll-Out Platforms (CROPs) were also used for bulk items and major assemblies. A tailored approach was taken to filling the CCASL, due to a backorder of BOH containers fielding across ABCT formations.
During the conversion, the SSA platoon was only manned at 19 of the 32 authorized automated logistics specialists (92A), due to an exceptionally active permanent-change-of-station (PCS) cycle. 1/1 ABCT mitigated these shortfalls by augmenting the SSA with internal assets and cross training 10 additional personnel from the Distribution Company’s Fuel and Water Platoon. On top of the conversion, 1/1 ABCT SSA still processed over 150,000 receipts across three battalion-to-division field-level exercises.
Lessons Learned
The CCASL conversion, multiple field exercises, and continued support to the units presented some of the greatest challenges for the 1/1 ABCT SSA. The first lesson learned was ensuring dedicated time is provided to the SSA to conduct its conversion. If treated with the same mentality of a wall-to-wall inventory—where support is paused except for the most critical items—units will find their CCASL conversion to occur more quickly and with better results. The most significant challenge took place in winter and spring of 2018, when the SSA was fielded 18 BOH containers, and several days later began receiving the 2,200 additional lines of material. This influx of material coincided with a field exercise in March and May 2018, causing the SSA to split its commitments to both brigade support and CCASL conversion.
The second lesson came as the SSA tried to balance expeditionary operations with CCASL creation. The process to put away material continued as the SSA supported the brigade in the field. New material that was received, as well as old material stored in quadcons, were immediately transported forward where it was balanced against the planograph and stored in its proper location. This enabled the SSA to continue to build the brigades CCASL while simultaneously sup-porting decisive action operations.
The simultaneous support and conversion was a significant source of friction for the SSA that resulted in decreased efficiency and accuracy. Even with augmentation, the SSA struggled to balance all field operations, supply support, and CCASL creation. The time between the two field exercises was heavily maximized by striking a balance between the conversion, providing support to the brigade, Soldiers low-density training, and core competencies. AMC recommends that units converting to CCASL refrain from tactical operations, and rather conduct their support from the rear, utilizing hard-structure facilities while easing into expeditionary support. Units should heed this advice to avoid SSA inaccuracies while balancing Soldier well-being and customer support.
The final lesson of the CCASL was influenced by maintaining the standardization after an ATF was conducted. The brigade’s first ATF review was conducted in August 2019, one year after the CCASL conversion was completed, and resulted in a 500-line increase to the ASL. This review replaced the old demand-analysis process and is used to determine the effectiveness of a unit’s ASL while adjusting the stock based on the previous year’s trends. Unlike the additional fielding, the line increase was not on the planograph with identified storage locations. This caused friction with the larger intent of a standardized AMC planograph layout that provides predictability, as each increase in the ATF will result in a slightly different CCASL layout. We recommend that efforts be made to laterally communicate the results of an ATF and allow SSAs, or AMC, to develop a new standardized planograph that enables the intent to be continued.
If the original 4,500 lines of an ABCT’s CCASL is standardized, then the final 500 should be as well.
Conclusion
The CCASL conversion delivered enduring lessons that units should heed as future supply support activities evolve. Ensuring dedicated time and deconflicting the CCASL conversion against a tactical setting creates the conditions for a timely and successful conversion. This action alone sets the tone and mindset for Soldiers to work, and it should be treated in the same regard as any new equipment fielding or major battalion training event. Converting the ASL in a garrison environment reduces inaccuracies while also decreasing the time necessary to put away the items. Units should take caution in ensuring that parts are stored correctly in the BOH container or flat rack to ensure that all items fit before locking in its location. Finally, SSAs should take an extra measure to ensure that new additions or deletions across multiple locations are standardized by location to ensure the intent of the planograph is met.
1/1 ABCT has had a steady in-crease in overall readiness since the CCASL conversion was completed. The standardization, ease of access, and accuracy of GCSS-Army storage location has resulted in a consistent 40% increase in accommodation and fill rates. Overall, the CCASL conversion has been beneficial when converted with deliberate staffing and resourcing, the CCASL provides a systematic ability to quickly enable generation of combat power.
--------------------
Lt. Col. Angel Cardenas is currently assigned as the Battalion Commander, 101st Brigade Support Battalion, 1st Armored Brigade Combat Team, 1st Infantry Division, in Fort Riley, Kansas. She received her Bachelor of Science in Criminal Justice from Cal State University of Long Beach. She received her Masters in Policy Management from Georgetown University.
Maj. Michael Johnson is a brigade support operations officer assigned to 1st ABCT, 1st ID, Fort Riley. He holds a Master of Science in Logistics Management from Florida Institute of Technology and a bachelor’s of arts degree in political science from Christopher Newport University.
Capt. Stephen R. Haley serves as the company commander for Alpha Company, 101 BSB, 1ABCT, 1st Infantry Division located at Fort Riley. He holds a Bachelor degree in Finance from Oregon State University. He is a graduate of the Logistics Captains Career Course from the Army Logistics University and the Air Assault School.
Warrant Officer 1 James L. Copeland served as the accountable officer for Alpha Company, 101st BSB, 1st ABCT, 1st ID, at Fort Riley. He holds an associate's degree in real estate management from American Military University. He is a graduate of the Warrant Officer Candidate School, Joint Operations Advanced Course, Airborne and Air Assault School.
--------------------
This article was published in the October-December 2020 issue of Army Sustainment.
RELATED LINKS
The Current issue of Army Sustainment in pdf format
Current Army Sustainment Online Articles
Social Sharing