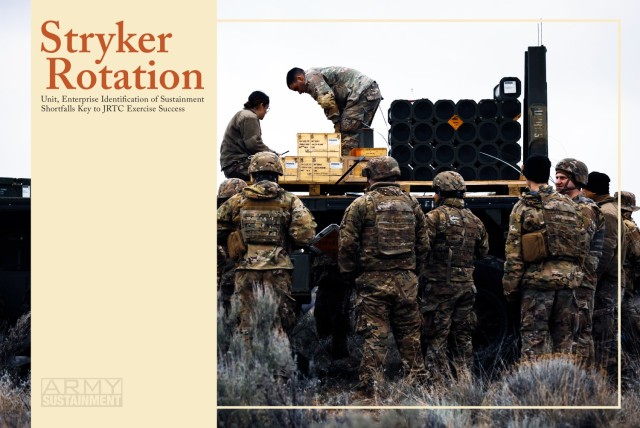
Stryker rotations have been infrequent at the Joint Readiness Training Center (JRTC) but are planned once a year for the next five years. As the fourth Stryker brigade combat team (SBCT) to train at JRTC, 2nd SBCT, 4th Infantry Division (2/4ID) completed JRTC 23-03 from Jan. 7 to Feb. 9. The brigade’s seven organic battalions were augmented by units from Canada; Fort Carson, Colorado; Fort Riley, Kansas; and Fort Bliss, Texas. While unit and enterprise preparation for Combat Training Centers (CTCs) always includes logistics planning, a Stryker rotation at JRTC poses several unique challenges not faced at the National Training Center (NTC). The installation supply support activity (ISSA) at Fort Johnson, Louisiana, does not stock Stryker or tank repair parts on its authorized stockage list (ASL). The call-forward process during force-on-force is much more restrictive at JRTC than at NTC and requires additional division logistics support element (DLSE) oversight by the Army Field Support Battalion (AFSBn). The standard JRTC regeneration timeline coming out of the box is 10 days compared to 12 for NTC, but rail outload is complicated at JRTC with only six spurs and the lack of locally owned locomotives. Identifying and focusing on the logistics capability shortfalls for an SBCT during the predeployment site survey and months leading up to the rotation proved pivotal in condition-setting the brigade to succeed.
The 2/4ID maintained an operational readiness (OR) rate of no less than 82% during force-on-force and achieved 91% by regeneration day 3. Before the exercise started, however, the unit had to deliberately plan to set conditions for success:
Healthy common ASL and optimized shop stock list (SSL) upon arrival. Units within 120 days of a CTC rotation or deployment must prioritize filling optimized SSL. This is especially important when going to JRTC, where there is no Stryker ASL to fall back on. The 2/4ID began the rotation with a 94% optimized SSL fill rate, allowing them to quickly regenerate combat power at the training center immediately following rail download with minimal reliance on the supply system. With division sustainment brigade and G-4 oversight, 4ID identified zero balance lines for common ASL and optimized SSL. The division first cross-leveled internally and then worked with the installation supply representative at the AFSBn and the Defense Logistics Agency team to expedite the remaining parts. The team recognized the lead time required to receive, process, and pack these items ahead of rail operations and began these efforts four months out.
Pre-positioned repair parts at the Fort Johnson ISSA. Given the infrequency of Stryker rotations at JRTC and the need for Stryker and tank parts elsewhere in the Army, it does not make sense to maintain a Stryker ASL at the Fort Johnson ISSA. However, pre-positioning parts there before Stryker rotations make sense to reduce response times and maintain fleet OR rates. The enterprise supported 2/4ID and Fort Carson’s request to pre-position parts, dramatically reducing the need for expensive, last-minute shipments from other locations. The basis for the pre-position quantities was a pull of the brigade’s most recent NTC rotation consumption data. Adjusting to account for differences in JRTC’s terrain, the critical parts request was 31 lines valued at $2.8 million. The AFSBn then communicated that list through the 407th AFSB to the Army Sustainment Command support operations team. Of the 31 items, 18 were available in the system and moved within the Army Working Capital Fund to the Fort Johnson ISSA in the weeks leading up to the rotation. This process worked very well with the support of the Fort Johnson Logistics Readiness Center and should be standard in the future for Stryker rotations. Additionally, the enterprise must ensure the narrative about the cost of pre-positioning parts remains on the realized second destination transportation (SDT) costs of the movement and not the dollar value of the parts in the temporary Army Working Capital Fund movement. As was true for 2/4ID, the rotational brigade should always keep the requested pre-position quantities to reasonable amounts to consume as much as possible and minimize any return SDT costs following regeneration.
Consolidated sustainment support location. The AFSBn’s DLSE, 4ID Division Support Element, 4th Division Sustainment Brigade, and 13th Expeditionary Sustainment Command worked out of the same building at North Fort Johnson to ensure a common operating picture. This enabled daily crosstalk and prevented confusion about OR rates in daily reports to the division, III Armored Corps, and Army Sustainment Command. It allowed visiting senior leaders to engage all sustainment teams simultaneously. This consolidated footprint also served as the hub for logistics assistance representative (LAR) and field support representative (FSR) coordination, which was particularly important at JRTC. Brigades are not allowed to bring unit-funded FSRs into the box during force-on-force, but they do want to utilize them during expeditionary reception, staging, onward movement, and integration (RSOI) and regeneration. AFSBns should plan to manage the daily transportation and coordination for these unit-funded FSRs in addition to the LARs during Stryker rotations, an increase of 20 to 25 personnel.
As Stryker rotations at JRTC will likely increase, here are some ways units can prepare for future exercises: Repair parts estimates need continued refinement. While the list of requested pre-position parts was based on accurate consumption data from NTC, the team learned several lessons. The 2/4ID only used 13 of the 18 pre-positioned lines (72%). Of the 13 lines they used, they needed more than requested. Additional Stryker units training at JRTC utilizing pre-positioned parts will enable better estimates over time. In the future, the pre-position list should include critical tank parts, even if the enabler tank company intends to bring a portion of its optimized SSL from the home station.
Optimized SSL fills to healthy levels should be standard practice. It is currently up to the rotational unit and local AFSBn to ask the enterprise to expedite parts to fill common ASL and optimized SSL in the months leading up to a CTC rotation. Standardized enterprise involvement 120 days out would help immensely. Army Sustainment Command is constructing a team to determine how the Army could formalize this process for units with known CTC and deployment dates.
Rail as the regeneration limitation. The standard regeneration model at JRTC is 10 days compared to NTC’s 12 with a similar flow of events. The unit focuses first on maintenance and return of vehicles drawn from the CTC, clearance of hand receipts for all supply classes, and turn-in of Multiple Integrated Laser Engagement System (MILES) gear. Units typically progress through turn-ins first and transition to rail upload for the second half of regeneration. This sequential model works at NTC because the rail head has 11 spurs to load vehicles and one for containers. Units complete outload in the remaining number of regeneration days. At JRTC, however, there are only five spurs to load vehicles and one for containers. The JRTC transportation team does not have its own locomotive or locomotive engineers, making them entirely reliant upon rail carriers to reorganize empty and loaded cars. This delays rail outload for larger Stryker rotations. The 2/4ID brought eight full trains of 75 cars from the home station plus enabler equipment from other installations to rotation 23-03. By comparison, a typical infantry brigade combat team (IBCT) brings five smaller trains with 45 cars each, plus enablers. Given the increased volume of equipment, 2/4ID required an exception to policy from JRTC to begin upload during regeneration earlier than an IBCT would so they could complete rail by the tenth day. JRTC granted that exception but generally grants them sparingly, for a good reason. Allowing units to ship containers home before clearing MILES hand receipts increases the risk this expensive equipment could accidentally be sent to the unit’s home station. While 2/4ID did get approval and began rail upload early, the 10-day model still proved insufficient to complete outload before the arrival of 2nd Brigade Combat Team, 10th Mountain Division. The rail overlap challenge was compounded by rail car delays outside of unit control, a frequent occurrence, but it further supports allocating additional regeneration days to an outbound SBCT or standardizing early rail upload. Since CTC training calendars are created a year out or more, it is essential to start that dialogue early to impact future Stryker rotation calendars. It is worth noting JRTC plans to test a new, condensed expeditionary RSOI and regeneration model in late summer 2023. This new model reduces both expeditionary RSOI and regeneration windows to nine days instead of 10. The idea is to test limiting IBCTs to four trains worth of equipment instead of the five they usually bring and, if adopted, would see JRTC adopt a 28-day model versus a 30-day one. While this could be very efficient for IBCTs, the reduced timeline should not apply to Stryker rotations.
Next-generation automatic test system (NGATS) or Direct Support Electrical Systems Test Set (DSESTS). Fort Johnson should maintain an NGATS or DSESTS to support rotations with tank enablers. Some tank companies bring one, but not all, and the logistics readiness center does not have one on-site.
The 2/4ID’s JRTC 23-03 was very successful from both enterprise and rotational training unit standpoints. Through deliberate planning by 4ID, AFSBn-Carson, Fort Johnson, and Army Sustainment Command, repair parts support in the absence of a local Stryker ASL went smoothly. Synchronized reporting from 4ID and the AFSBn led to a common operating picture and centralized coordination for LAR support. For required parts beyond what was pre-positioned at Fort Johnson, the 13th Expeditionary Sustainment Command team was instrumental in enabling supply visibility and moving additional critical parts from Fort Cavazos. The JRTC leadership’s exceptional support and flexibility during the rotation allowed 2/4ID to quickly identify and safely work through challenges. The team will take these lessons and be better prepared for the next Stryker rotation at JRTC.
--------------------
Lt. Col. Sarah Gilbert serves as the commander of the Army Field Support Battalion at Fort Carson, Colorado. She previously served in the 4th Infantry Division, 10th Mountain Division, the Defense Logistics Agency, and the Army Human Resources Command. She was commissioned as a second lieutenant in the Quartermaster Corps and awarded a Bachelor of Science in business and a Bachelor of Arts in international studies from the University of Missouri-Columbia. She holds a Master of Science in supply chain management from the University of Kansas.
--------------------
This article was published in the Summer 2023 issue of Army Sustainment.
RELATED LINKS
The Current issue of Army Sustainment in pdf format
Current Army Sustainment Online Articles
Connect with Army Sustainment on LinkedIn
Connect with Army Sustainment on Facebook
------------------------------------------------------------------------------------------------
Social Sharing