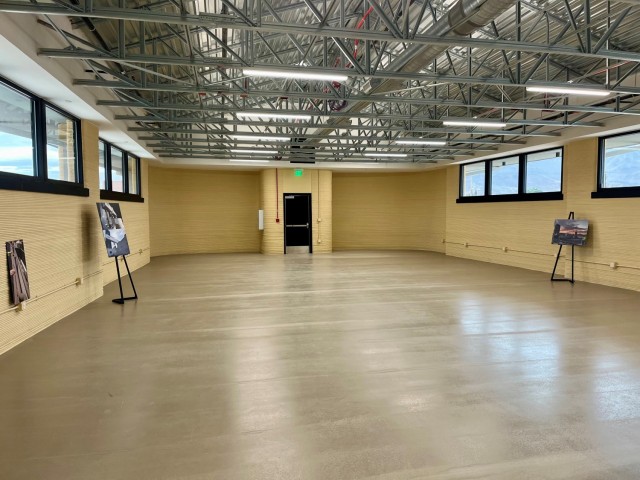
FORT BLISS, Texas — Sgt. Maj. Michael Perry, the senior enlisted advisor to the deputy chief of staff G-9, recently visited Fort Bliss, where an innovative pilot program aims to improve Soldier quality of life and enhance the resilience of the Army’s installations.
The Army’s 3D printed barracks pilot program represents a transformative approach to enhancing Soldier living conditions and readiness, with three first-of-their-kind new barracks scheduled to open later this Summer.
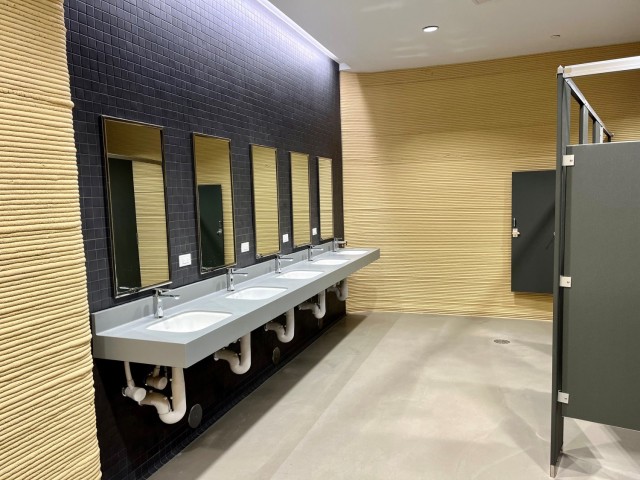
Fort Bliss is currently completing construction of three of these facilities, scheduled to open later this summer. Each facility will have 36 bunk beds and be able to house up to 72 Soldiers. Initially, these barracks will be used as collective training barracks.
“By prioritizing Soldier well-being with mold-resistant materials and energy-efficient designs, these new barracks truly represent how ‘it’s better at Bliss,’” said Fort Bliss Command Sgt. Maj. Dave Sweeney. “The introduction of 3D printed barracks embodies our commitment to creating a truly exceptional experience for Soldiers living and working here.”
These barracks offer a promising solution to the Army's housing needs by exploring the benefits of energy efficiency, cost savings and resilient materials associated with 3D printed structures.
At more than 5,700 square feet, the barracks began construction as the largest 3D-printed structures in the Western Hemisphere. They are designed to highlight how 3D printing could be used to build energy-efficient and resilient buildings faster and at a lower cost than traditional building methods.
“With the promise of energy efficiency and cost savings, this pilot embodies the Army’s dedication to innovation in meeting the evolving needs of our force,” Perry said. “By exploring these pilots, we’re not only exploring ways to build better and faster, but we’re also exploring construction options that will ensure our Soldiers thrive in sustainable living quarters.”

The barracks are also set to be the first 3D-printed structures to comply with the Defense Department’s updated Unified Facilities Criteria, which provides construction guidance DOD-wide.
Previously, the UFC did not include specifications for 3D-printed concrete wall systems, preventing the Department of Defense from leveraging potential efficiencies gained from 3D printing and preventing companies that built wall systems through 3D printing from bidding on Department of Defense construction projects.
ICON, a construction technology company based in Austin, Texas, was selected to complete the barracks pilot construction using their proprietary Lavacrete material to build the wall systems.
According to ICON, this material is designed to withstand extreme weather and reduce impacts from natural disasters, while also enhancing energy efficiency. These wall systems are also designed to be printed at high speeds, enabling structures to be built faster, which helps construction projects stay on schedule and on budget. ICON also claims this building material will last longer than traditional construction materials and methods and lend themselves to being mold resistant.
“The weather resilient and mold-resistant properties of this pilot underscore the Army’s commitment to enhancing quality of life for our Soldiers,” said Perry. “By prioritizing pilots that offer these properties, we safeguard Soldier health and wellbeing, creating homes for our Soldiers that can withstand the test of time and environmental challenges faced across our installations.”
Resilience and readiness are interconnected and mutually reinforcing. A more resilient installation enhances the Army's readiness, capability and lethality. The technology explored to construct these barracks offers the potential to enhance Soldier quality of life and transform how the Army approaches installation resilience.
Social Sharing