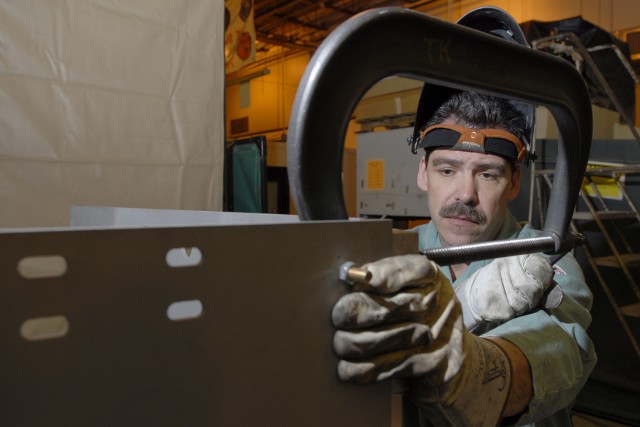
TOBYHANNA ARMY DEPOT, Pa. (April 26, 2010) -- Tobyhanna is meeting a short suspense to provide an installation kit that offers armored protection for a mine-detecting robot.
The Talon Hermit Robot Deployment System, or RDS, is used for route clearing, mine detection, vehicle inspections and route surveillance.
The Deployment System Kit is an electrically controlled arm that is installed on the Mine-Resistant Ambush-Protected, or MRAP Buffalo vehicle platform. It stores the Talon Robot in an armored housing attached to the arm. When the Talon Robot is needed, the arm is lowered from within the vehicle and the robot is deployed via remote control.
Employees are fabricating several kits in a quick-reaction effort for the U.S. Army Research, Development and Engineering Command at Edgewood Chemical Biological Center. The center asked Tobyhanna to assist with the development, testing and fabrication of the kits.
"Basically, we're building the box that the robot stays in while being transported on the MRAPs," said Tim Knabel, mechanical engineer. "The boxes sit on the outside of the vehicle and protect the robot while it's in transit. Each box weighs more than 200 pounds."
Knabel works in the Manufacturing Engineering Branch of the Production Engineering Directorate's Engineering Design Development and Manufacturing Division.
Work began in March. "Following notification of upcoming workload, Tobyhanna engineers visited the center to review the drawing packages and made suggestions that would make the product easier to manufacture," Knabe said. "Once suggestions were implemented, the center provided updated drawing packages that would allow us to start fabrication."
The kits contain the items to build the box, such as the box itself, a primary pivot arm, a secondary arm, a cylinder mount to raise and lower the carrier on the vehicle, and a hook assembly that locks the carrier in position.
They are fabricated in a collaborative effort by Production Engineering and Systems Integration and Support directorate personnel. Engineers worked with technicians in sheet metal, machining and welding shops to build the parts.
"We use the drawings to create models and then send the models to the manufacturing cell," said Jack Andrejko, mechanical engineering technician, Manufacturing Engineering Branch. "The manufacturing cell creates part programs that provide instructions on how to fabricate each of the nearly 70 parts. The parts programs are then sent out to the floor."
From these models, computerized numerical control part programs were developed to fabricate the parts in the sheet metal and machine shops. Routes in the Logistics Modernization Plan, or SAP system here were developed that describe to the shops how the parts are fabricated or welded.
One challenge sheet metal shop technicians faced was a 30-degree bend for the opening of the box. Technicians from the Sheet Metal Fabrication Branch contributed collectively to the solution of the problem of forming the armor plate material.
"Tooling normally on-hand for forming regular bend radii on common materials was not readily available in this case," said Robert Aten, chief of the Sheet Metal Fabrication Branch. "Technicians started the process to adapt and use old-style tooling from our recently replaced press brakes to form the armor plate brackets. They were able to program the new press brake to accept the old-style tooling, and successfully form the parts. This prevented the need to contract out the forming of the armor plate and helped meet a very tight schedule."
After they are fabricated, parts are sent to the Refinishing Services Division for sandblasting, plating and/or painting.
"There have been a couple of changes since starting production, but we're flexible, Knabel said. "That's why the center likes working with us. We're able to do whatever they want."
"Our partnership with Tobyhanna has been great; they are able to produce quality, high-volume parts very quickly," said Kevin Ridgley, mechanical engineer at Edgewood Chemical Biological Center. "Everyone has been very helpful in getting us to our deadline production-wise and have dealt with any changes we needed to make. I look forward to working with them again."
Finished kits are sent to the Edgewood center for assembly and shipped to Southwest Asia.
"With such a short suspense on this project, the shops have been very flexible and cooperative, said Knabel. "If we get a late change from the customer, they're able to adapt and overcome obstacles."
Tobyhanna Army Depot is the Defense Department's largest center for the repair, overhaul and fabrication of a wide variety of electronics systems and components, from tactical field radios to the ground terminals for the defense satellite communications network. Tobyhanna's missions support all branches of the armed forces.
About 5,600 personnel are employed at Tobyhanna, which is located in the Pocono Mountains of northeastern Pennsylvania.
Tobyhanna Army Depot is part of the U.S. Army CECOM Life Cycle Management Command. Headquartered at Fort Monmouth, N.J., the command's mission is to research, develop, acquire, field and sustain communications, command, control computer, intelligence, electronic warfare and sensors capabilities for the armed forces.
Social Sharing