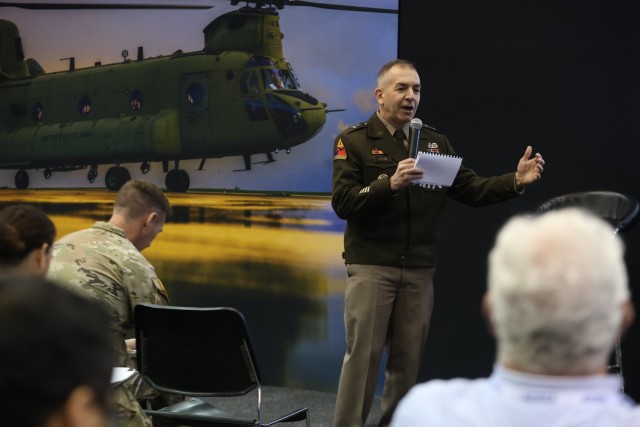
HUNTSVILLE, Ala. – From 3D printing parts for Soldier use in the field to ensuring the readiness of watercraft, the U.S. Army Tank-automotive and Armaments Command plays a critical role in force modernization and preparedness.
That was the key theme of the remarks by Maj. Gen. Michael B. Lalor, TACOM commanding general, at the 2025 Association of the United States Army Global Force Symposium and Exposition. During three separate Warriors Corner sessions, Lalor showcased recent successes in advanced manufacturing, the Operational Readiness Program and watercraft maintenance to an audience of key military and defense industry leaders.
“This isn’t something we’re going to do in the future,” Lalor said about the command’s innovative advanced manufacturing initiatives. “We’re doing it right now.”
The March 25-27 conference at the Von Braun Center in Huntsville, Ala., highlighted how the Army is driving continuous transformation and becoming a multi-domain capable force.
In the advanced manufacturing presentation, Lalor and TACOM Integrated Logistics Support Center Executive Director Mark Colley said the command has been driving hard, with urgency, for more than a year to harness and develop high-tech tools and processes.
They explained how TACOM’s Battle Damage Repair and Fabrication program has used 3D printing and other advanced technologies to design and produce more than 50 different lines of approved temporary use parts, with many more expected soon.
The program is intended to supplement – not replace – the traditional supply chain.
“The purpose of our advanced manufacturing mission, both at AMC (U.S. Army Material Command) and as driven by TACOM, is to fill gaps, active gaps, in the supply chain, and then to serve as a catalyst for proliferating this capability throughout the formations on the battlefield so that we can produce at the tactical point of need, generate readiness and keep ourselves moving in any future operation,” Lalor said.
He noted that the world-class 3D printers at Rock Island Arsenal-Joint Manufacturing and Technology Center (JMTC) have “graduated way past” polymers and are making parts using titanium and steel.
Lalor also said that some BDRF-produced parts, such as an M88 actuating arm, have outperformed their original counterparts in key tests.
“Ultimately, where we’re going to go is to produce parts in the thousands, and we’re going to qualify the parts through a process that qualifies the material, data and processes so that we can manufacture and produce at a higher rate, and at echelon from the tactical edge back to the strategic at JMTC,” Lalor said.
In December, TACOM launched the first-of-its kind quarterly BDRF technical bulletin. It is also playing a key role in the ongoing development of an Army-wide advanced manufacturing strategy, which is expected to be released later this year.
Colley said TACOM is not just sustaining today’s Army but also preparing for tomorrow, especially as units are keeping inventory longer and can’t always endure lengthy wait times through the supply chain for replacement parts.
Advanced manufacturing is going to propel us forward, he said, “and we’re going to push the boundaries on advanced manufacturing.”
In another session, Lalor, Colley and two other presenters – Maj. Gen. Sean Davis, Deputy Chief of Staff G-4 for the U.S. Army Forces Command and Brig. Gen. Terry Tillis, Deputy Commanding General - Support for the 1st Infantry Division – talked about how the Operational Readiness Program is having an enduring impact on readiness.
Launched in late 2024, the program enhances readiness and training in tactical units through an approach that combines sustainment-level maintenance and field-level maintenance training. It is geared toward brigade combat teams with aging fleets of track and wheeled vehicles, with 58 platforms targeted so far.
“The idea is to inject maintenance and converge that with some training to get a readiness effect for the unit, and then for the Army,” Lalor said.
The program gives newer Soldiers unique opportunities to learn directly from seasoned depot-level mechanics. Tillis said he recently saw four Soldiers watching a subject matter expert change out a generator on a tank.
“The very next day, on another vehicle, I’m watching those four mechanics who watched that subject matter expert from the flyaway team, they were the ones installing it the next day,” he said. “If you think about the competence, that they can not only perform the function, but they have the confidence and they can do it in a field environment, I think that’s critical.”
During the presentation about Army watercraft, Lalor said TACOM is proud to tackle sustainment-level watercraft maintenance worldwide. He spoke alongside U.S. Army Chief of Transportation Col. William Arnold; Chief Warrant Officer 5 Nicholas Laferte, chief warrant officer for Combined Arms Support Command; and Brig. Gen. Shane Upton, Army Futures Command, Contested Logistics Cross-Functional Team commander.
Lalor said over the last 18 to 20 months, there has been an aggressive push to perform more watercraft maintenance forward and in new regions, with some vessels currently undergoing repairs west of the International Date Line.
TACOM has helped lift the Army’s sagging watercraft readiness rates, Lalor said, with total fleet readiness jumping more than 200% over the last four months. That readiness is expected to increase another 50% by the third quarter of the 2026 fiscal year.
“Our focus has been to be responsive, to fix forward,” Lalor said, “and to make sure that we get a fully mission capable system back to the mariners who need to execute their mission.”
Social Sharing