
“Steeped in tradition, our US military has had a love-hate relationship with innovation and change. And while military leaders will enthusiastically embrace tactical innovation on the front line ... during peacetime leadership is hesitant to support tactical or strategic innovation, especially in organizations more distant from the fight.”
- Dr. Rod Korba, Small Wars Journal, November 22, 2016
This quote from a Small Wars Journal contributor addresses logistical dilemmas on the modern battlefield. Traditional means of sustaining and transporting the force are challenged daily as the American military engages in an ever-changing global fight. How we, as logisticians, approach sustainment problems abroad and embrace innovation is the determining factor in achieving adversarial supremacy. Creating new methods and innovative solutions is never easy, especially when synchronizing many different organizations.
When it comes to war, the U.S. military is always playing as the visiting team. Over the past 125 years, most U.S. conflicts have been in distant places far from American shores. For units aligned to the U.S. Pacific Command (USPACOM) area of responsibility (AOR), places such as China, Russia, and North Korea are all nearly on the opposite side of the globe. The vast Pacific Ocean keeps these adversaries thousands of miles from U.S. shores.
Sustaining a forward presence in the USPACOM AOR across such distances is challenging. The wide variety of terrain in the USPACOM AOR spans from mountain peaks to dense jungles, often making ground lines of communication nonexistent. Despite enormous advances in surface vessel and strategic airlift technologies, distance remains the key challenge for the U.S. Army in the Pacific.
Earlier this year, the 17th Field Artillery Brigade commander charged the support operations (SPO) team with solving a critical sustainment task that had yet to be addressed: in an austere environment, how does an M142 High Mobility Artillery Rocket System (HIMARS) battery or battalion offload critical Class V from fixed and rotary wing aircraft when no organic material handling equipment (MHE) exists? The task was simple but would prove difficult to solve. In a matter of months, U.S. Army Pacific would begin participating in annual exercises with partner nations in the Pacific. The brigade would soon be deployed to various isolated islands dispersed throughout the region. Leaders had to solve this problem creatively and efficiently, leveraging existing capabilities while integrating joint and multi-compo organizations.
Solving the Problem
A field artillery (HIMARS) brigade support battalion (BSB) differs from a brigade combat team in capability and structure. Key among the shortfalls was the inability of the forward support companies (FSCs) to provide MHE support for their respective batteries. The only MHE capability in the brigade lies in the BSB and is limited to two 10K ATLAS forklifts. To support lift requirements for both firing battalions simultaneously, the BSB is dependent upon external organizations for MHE support. The inability to provide MHE organically is compounded as batteries and platoons are dispersed to deliver surface-to-surface precision strikes in support of joint task force operations.
To solve the given problem, we had to be innovative in our approach. Again, attempting to execute offload and resupply methods for the first time adds to certain anxieties at all levels. Making the proof of concept realistic, feasible, and repeatable were the key factors in addressing the situation. Assets organic to the brigade centered around the M1084 Resupply Vehicle (RSV), while assets organic to the firing battery included the M985 Heavy Expanded Mobility Tactical Truck (HEMTT) and M1120 Load Handling System (LHS) with the M3 container roll-in/out platform (CROP) (organic to the FSC and BSB) loaded with four rocket pods. These were the three assets in which the unit used to solve the problem. In addition to using the assets organic to the brigade, recreating the vast distances of the Pacific Ocean was another area to be addressed to reflect the realism of solving the problem. Utilizing both the Yakima Training Center (YTC) and training areas at Joint Base Lewis-McChord (JBLM), we sought to create two separate “islands” for the delivery of munitions via aircraft. To incorporate realistic situations in which our brigade may encounter dispersed, we planned simulated firing point resupply via rotary wing and FSC and BSB ammunition transfer holding point resupply via the fixed wing. Each echelon of rocket pod resupply would encounter one, if not both, methods that were tested. The proof-of-concept was dubbed Operation Island Hopper. Utilizing a Cargo Helicopter 47 (CH-47), the unit tested an offload method using an RSV crane at JBLM training areas. At a landing zone at YTC, the unit tested its ability to offload rocket pods from a C-17 utilizing the HEMTT and LHS only.
The Game of Inches
In the film “Any Given Sunday,” Al Pacino refers to life and football as a game of inches due to the margin of error in both being so small. One step too early or too late, too slow or too fast, and someone won’t make it. This quote best describes the learning process accomplished in creating the proof of concept. The finite dimensions of CH-47 (90 inches wide by 78 inches tall) and C-17 (208 inches wide by 190 inches tall) ramp and cargo door areas forced the unit to be diligent in its efforts. As training pods were loaded, offloaded, reset, and transferred, unit personnel searched for ways to get additional space to complete the offload. The most knowledgeable personnel in the brigade (on RSV, HEMTT, and LHS) utilized every feature their vehicle was equipped with to get every inch possible. Details, including when would the rocket pod be exposed on the ramps, which mode does the LHS need to be in to maintain the lowest profile for offload, and how far does the crane need to boom out, were regularly addressed in each iteration of training. Each measurement had to be correct, codified for reference, and repeated with each vehicle crew for continuity. Every inch mattered. Every piece of shoring factored into weight distribution. Every operator’s expertise added to a greater margin of error during execution. Through deliberate attention to detail in all factors of size, weight, capability, and overall expertise, the processes ensured that offloads were not too early, too late, too slow, or too fast.
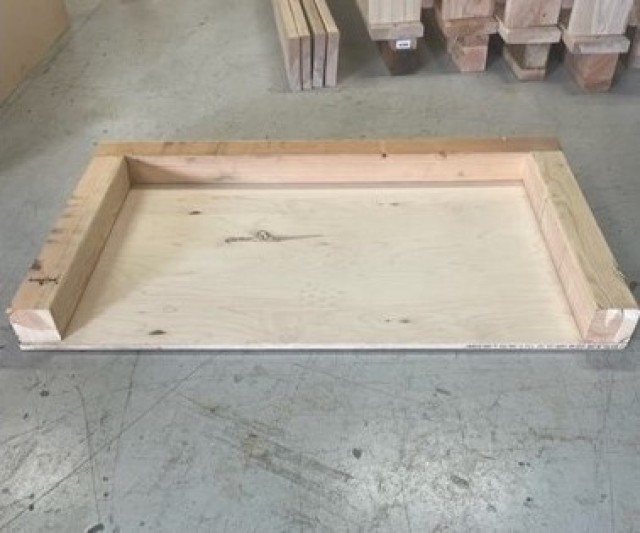
McChord, Washington, on April 17, 2022. VIEW ORIGINAL
Ready for Prime Time
On the day of execution, the culmination of five months of planning, training, and coordination between 18 separate agencies took place. The task was simple but not easy: offload the rocket pods using organic vehicles without damaging the aircraft. To make shoring portable in either a high mobility multipurpose wheeled vehicle or other military vehicles, the team created a device that allowed the pod to be freely moved on the CH-47 utilizing its roller system and protect the pod and aircraft from damage. We utilized 3/4-inch plywood as a base with 4- by 4-inch beams on the front and sides to prevent the pod from shifting. The plywood was cut to a width of 51 3/4 inches and a length of 28 inches. The device was placed on both the front and back ends of the pods.
Once the CH-47 landed, the ramp was lowered to its lowest point. When given the signal, a two-person pusher team unstrapped two of the three ratchet straps and pushed the pod until the pod shoring closest to the ramp rested on the ground. Once the pod was pushed forward, the crew chief guided the CH-47 approximately five feet forward to expose the attaching point at the center of the pod. Once ready, the CH-47 crew chief signaled the RSV team leader to position the RSV. The RSV team leader ground guided the RSV to the aircraft ramp with the crane in a “scorpion” position. The RSV team leader lowered and extended the crane to a low enough position to give the rear rotor blades of the CH-47 at least four feet of clearance. The RSV team leader ground guided the RSV to approximately thirteen feet from the ramp of the CH-47. The RSV crew extended both outriggers to stabilize the RSV in preparation to support the pod. The RSV was then able to hook onto the pod and lift until the RSV supported the weight. The pusher team rotated the pod until it was perpendicular to the CH-47. The crane rotated to the side and set the pod onto the ground. The total time from lowering the ramp to having the pod cleared of the aircraft was 7 minutes and 49 seconds.
The C-17 iteration presented a different set of problems: operating in a joint environment. The challenge of joint operations is that each branch of the U.S. military speaks its own language. When interacting with another service, both parties take for granted that both the sender and receiver of information understand exactly the context of the message. This challenge was overcome by overcommunication and redundant information between Army and Air Force elements.
Once the C-17 landed, taxied, and stopped, the ramp was lowered to a coplanar position (horizontal). When given the signal, the pallet pusher team pushed the T3 pallet train to the end of the ramp until it was flush with the edge. Once the T3 pallet train was pushed forward, the loadmaster signaled the LHS team leader to position their vehicle within 12 inches of the ramp. The hook arm was positioned between the ramp of the aircraft and the upright of the M3 CROP. The hook arm hooked into the M3 CROP, securing the load to the vehicle. The aircraft ramp was lowered to five degrees below horizontal to allow for more space as the M3 CROP was elevated onto the LHS vehicle. A guide stationed inside the aircraft guided the hook arm’s operation utilizing the Manual Hook Arm and Manual Main Frame modes of the LHS. The guide, along with the loadmaster, communicated which direction the LHS hook arm needed to maneuver to safely offload the M3 CROP without damaging the aircraft’s roof.
A mixture of relief, pride, and excitement swept across the aircraft once each pod and M3 CROP was successfully offloaded onto their respective vehicles. After 7 minutes and 36 seconds, sustainment history was made, and everyone knew it. For the first time, an Air Force aircraft was successfully offloaded by Army assets other than traditional MHE. We solved a realistic problem set that has far-reaching applicable capabilities for our formations. Various elements of brigade and corps level leadership were interested in our endeavor, which magnified the success or failure of this venture. Success was achieved through deliberate planning, meticulous coordination, and creative thinking.
Reflections
While reflecting on what we accomplished with Operation Island Hopper, the SPO team conducted three after action reviews (AARs). The three AARs were conducted with the 308th BSB participants, the aircrew of the CH-47 General Support Aviation Battalion, and the loadmaster and air mobility liaison officer team from the Air Force. Critical data was gathered during each AAR and codified into two separate manuals for future use by other organizations. In addition to the codification, key lessons learned from the entire operation, from initial planning to execution, are worth sharing.
Here are a few key takeaways:
- The Human Psyche. Convincing 18 different organizations, all with experience within their field ranging from decades to only a few months, to risk assets, time, and reputation borders on being its own art form. Skepticism of the plan and the data presented, along with overall unwillingness to break from the norm all played roles in the challenge of bringing so many different elements together. Lessons learned from Operation Island Hopper include learning what each subject matter expert offers and fostering trust and motivation to utilize their skills effectively. That cannot be achieved through phone calls or emails alone. Taking the time to coordinate, in person, with each organization aided in our ability to sync 18 different elements simultaneously for success.
- Rehearse, Rehearse, and Rehearse Some More. Rehearsals are crucial in ensuring the success of the offload procedures. This method is more complex and requires an in-depth rehearsal of key actions so that all crews understand the sequence of events, cues to proceed, and contingencies. This, plus anything else requiring so many moving pieces, cannot be rehearsed enough. Once the team feels as though they completely understand what is required, rehearse it again. Due to the risk to personnel and equipment, it is highly recommended to have an experienced crew to conduct the offload. The crane and hook arm will potentially get within a foot of the aircraft with active rotor blades and running jet engines. Deliberate and continuous rehearsals will mitigate any confusion and allow each offloading crew to operate with minimal error.
- Take Prudent Risk. Nicolo Machiavelli states, “All courses of action are risky, so prudence is not in avoiding danger (it’s impossible) but calculating risk and acting decisively.” The riskiest things the military does include operating vehicles, aircraft, or weapons systems. Each provides its own level of risk associated with the operators using it. Attempting something new with one or a combination of the three adds to the already associated risk. Training, synchronization, and engaged leadership mitigated most risks encountered during processes for Operation Island Hopper. Sometimes the norm must be challenged, the impossible attempted, and the unforeseen planned. Taking the prudent risk after conducting the necessary steps to have a solid, resourced plan can pay off in far-reaching areas that no one thought possible. Do not be afraid to take prudent risks.
- What did the unit learn? After every static training iteration, in-progress review, and data pull, the team’s most important discussion point was, “What did we learn?” Being caught up in the moment is a primary reason critical data points and lessons learned are lost when creating new methods and processes. Each team member readily had cameras, clipboards, and notebooks to ensure there was something to reference afterward through every step. With such finite training time and the availability of assets, the team could not afford to recreate many of the steps conducted throughout. No matter what role one has in creating new processes, ensure that every stakeholder has the opportunity to codify their observations. Always remember to ask each team member, “What did we learn?” They may be surprised at what was missed.
--------------------
Maj. John B. Raynor currently serves as the 308th Brigade Support Battalion Support Operations Officer and 17th Field Artillery Brigade S4. Raynor was commissioned in the U.S. Army Transportation Corps in 2009 from Sam Houston State University ROTC. He holds a Master of Arts in Military History from Norwich University, Vermont.
--------------------
This article was published in the Fall 22 issue of Army Sustainment.
RELATED LINKS
The Current issue of Army Sustainment in pdf format
Current Army Sustainment Online Articles
Social Sharing