
Our joint and service maneuver doctrine tells us that decisive action depends on the operational reach to extend a force’s distance and duration in large-scale combat operations. It speaks to an implied operational imperative then, that a combined joint land force must have reliable, constant, and timely access to all classes of supply. When practitioners of the art of war think this, we focus on the classic essentials: sustenance, fuel, and ammunition. However, if case studies of previous high-intensity conflict have taught us anything, it’s that every class of supply matters. Moreover, in scenarios where mass casualty events are at the company or battalion echelon in terms of numbers, this article offers that class eight (CLVIII, medical supplies) is just as vital as the aforementioned supply needs. Today, within Europe, providing forward contingency stock of CLVIII for 62 nodes has shaped the requirement for future operations. The 16th Sustainment Brigade (16SB) tested a proof of concept on CLVIII integration, highlighting three opportunities that illustrate how the Army should adapt its doctrine, manning, and medical-logistics forward distribution systems to fully support CLVIII integration to extend its operational reach. These opportunities include changes to personnel and force structure, establishing a multi-layered distribution web, and modifying current business ordering platforms to become more inclusive.
The first opportunity in our proof of concept maximizes the efficient use of personnel against an assigned but potentially under-resourced mission set. People-first organizations require a methodology to cross-train their population to support complex operations, while not detracting from their primary mission or adding undue, unmitigated work. Understanding these needs, we sought to augment advanced individual training for our 19 Automated Logistical Specialists (92As) in the 240th Composite Supply Company, Supply Support Activity (SSA), providing them with a crash course for medical warehouse operations. The result was outstanding. All 19 achieved full certification and training in all ordering systems, platforms, and warehouse operations for basic medical resupply, bolstering their enlisted record briefs to include medical logistics operator. Some may say this small step is not enough to make a dent in the capability gaps for medical resupply across a large footprint. Still, this provides countless opportunities to streamline logistics operations across the military for many customers. This key step into the SSA transition demonstrates how the main medical supply chain requirements can be ordered, packaged, and distributed to most of the fighting force across the Army.
Furthermore, this creates cost savings by eliminating commercial contracts and providing additional medical stock at strategic points, decreasing customer wait times. If the Army were to replicate this concept, the amount of 92As could remain the same with an augmented training requirement for CLVIII ordering. It currently takes approximately one hour, per order, to process, from the time the customer communicates with the team at the SSA, to include the receipt, stock, or packaging of the CLVIII. If an item, filled through United States Army Medical Materiel Center – Europe (USAMMC-E), is not stocked at the SSA and is a new non-reoccurring order, dependent on the type and number of item(s) requested and handling requirements due to shipping method, order processing time increases several hours. As the proof of concept grows over the many phases, the SSA processing time should mimic USAMMC-E closely as the process becomes streamlined and CLVIII operations become routine. Although the 16SB has been able to execute with subject matter experts and minimal input from the medical brigade during this concept of support, another option would be to inject a well-versed Medical Supply Technician (68J) as a warehouse lead to oversee operations and provide customer support while the 92As gain expertise over phases and eventually years.
Establishing a multi-layered distribution web is not easy, and this second opportunity combats the distribution gaps and fiscal constraints. The medical brigade in the European theater primarily uses a direct shipment approach, or a cross-dock process, to minimize the amount of stock in the warehouse. This concept is very appealing to customers who do not have additional personnel as third-party commercial shipping companies that deliver directly to the customer door. This only works for small shipments and relies on the item being in stock at USAMMC-E. However, the strain on the large theater lead agent for medical materiel (TLAMM) in Europe causes backlogs with a single point of failure if our TLAMM process becomes frustrated or eliminated during deployment operations. The advantage of CLVIII within the SSAs is an already established process for pick up and distribution, existing without a need for third-party participation. During the U.S. Army Europe and Africa (U.S. Army Europe and Africa) Defender Europe 21 (DE 21) exercise, each unit’s DOD activity address code was aligned to a forward SSA. Units were then able to order from a condensed list of CLVIII items that were established in an authorized stockage list. As customers pick up CLVIII from the SSA, the availability of supplies decreases customer wait times with the centralized stock approach. Initially, the proof of concept focused primarily on emergency packages as “free issue” to the organization utilizing them, which has worked out greatly in four specific locations: Glamoc, Bosnia; Kucove, Albania; Zadar, Croatia; and Alexandropoulos, Greece. At the end of the exercise, the remaining CLVIII stock at Camp Bondsteel in Kosovo either remained for issue or was reintegrated back into the main SSA stock.
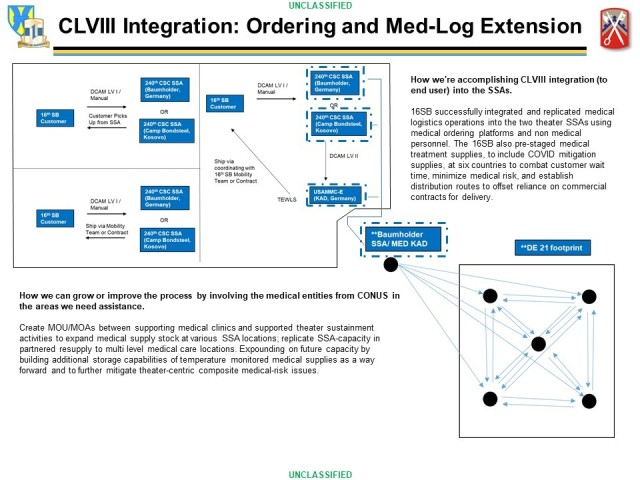
On systems ordering platforms, the third opportunity created challenges, as multiple ordering systems did not interface with each other. Once infrastructure issues were resolved, the actual systems can be implemented to streamline processes. The 92A’s are trained and proficient in all CLVIII ordering systems to include Defense Medical Logistics Standard Support Customer Assistance Module (DCAM) and Theater Wide Logistics System (TEWLS), as well as being proficient in Global Combat Support System – Army (GCSS-A) for all other classes of supply management. Although the CLVIII ordering systems do not interface with each other, the 92As were able to adapt and integrate their knowledge toward the different platforms and deliver CLVIII to customers. USAMMC-E has been a tremendous proponent in providing support to the 16SB with training, guidance, and materiel. The 16SB has submitted the necessary documents to gain access to TEWLS, and USAMMC-E is in the process of getting approval through the Army’s medical logistics community, which adds another step toward CLVIII integration. This would be the first time a non-medical warehouse uses the same capability as a TLAMM and provides an increased capability for management and procurement at an Army sustainer level. The entire train-up process at USAMMC-E and Baumholder, Germany, including on-the-job training with real-time orders, was 60 days, but it was only that long due to COVID mitigation strategies.
The advantage to DCAM is very simple; with no transaction codes to memorize, the 92As were quick to adapt to the system and immediately use it with their experience of GCSS-A. The primary disadvantages were being unable to see a real-time reflection of stock on hand, establishing the warehouse, and building the plant manually. Whereas, with TEWLS, USAMMC-E would be able to assist in building a plant and creating an actual warehouse for storage, truly expanding medical logistic capabilities. One hurdle to overcome with customers on both platforms is that many units in Europe are not structured under a brigade combat team with a brigade medical supply office (BMSO) to consolidate orders and utilize their DCAM. In Europe, under the 16SB, the surgeon cell orders CLVIII to consolidate for hundreds of personnel as a staff function without the warehouse capabilities. Additionally, in a BMSO, if they were to adopt the warehouse operations and decentralize CLVIII receipt, stock, and management, the BMSO would have to handle all shipping discrepancies. This would also require the BMSO to report requirements and item substitutions; As most BMSO positions are filled with junior officers, expertise becomes a concern when this position is filled with someone, not medical logistics board certified.
As the Army streamlines processes to model a Systems Applications and Products in data processing-based approach, the 16SB’s proof of concept runs in parallel to streamline CLVIII management into the SSA, centralizing logistics efforts across USAEUR-AF for DE 21 and preparing for TEWLS integration. The concept is not to eliminate the doctrinal medical logistics abilities existing within the medical brigade, but to expand the medical support to increase the commander’s operational reach and to mimic the forward distribution team (FDT) concept within the medical logistics company (MLC), just on a much larger scale than what is available today. Doctrinally, the MLC is designed to provide three FDTs. However, in Europe one of those is designated to augment USAMMC-E for various missions. This leaves a significant gap for capability in the European footprint; with direct shipment costs and customer wait times continuously increasing, in part due to COVID, country, and border clearances. Incorporating CLVIII into the SSA expands the medical resupply reach and streamlines processes across the footprint to minimize stock issues and distribution costs within existing routes and mobility apparatuses. In resourcing ways to solve these issues, units must replicate an existing capability quickly across their footprint. Locating an entity with most of the resources required is the key to implementing this concept in a short amount of time. The SSA has the organic warehouse material handling equipment (MHE) and the reach back for organic movement capabilities to work with multiple transportation elements such as fixed-wing, ground, and rotary assets, as shown with different shipments during DE 21. As the 16SB set up multiple warehouses and key receipt points across the footprint, this created additional logistics hubs using organic 92As exclusively to streamline capabilities to “plug and play” at any SSA. As we anticipate filling the medical logistics gaps and addressing the risks associated with CLVIII placement, the ability to operate jointly and use all movement assets becomes even more imperative in planning factor incorporation. For example, the MLC has enough MHE to doctrinally only provide three FDTs. However, Europe-wide exercises would require many more stocked locations, especially with country clearances, COVID mitigation strategies, movement assets, and limited reoccurring distribution priority timeline setbacks to provide isolation facilities (ISOFAC) CLVIII to include COVID mitigation contingency stocks. The current doctrinal approach for medical logistics demonstrates a limited location-based availability across the footprint, further compounded by a disconnect in communication to each other with no single large warehouse feeding medical supply to individual customers outside of USAMMC-E. In the Multi-layered Distribution Web figure, the model displays the integration of medical supply at multiple SSAs to replicate capabilities, and they all communicate and ship to each other with streamlined stock. This shortfall requires a doctrinal modification to theater CLVIII and medical logistics support in future multi-domain competition, something 16SB’s medical and logistics teams are planning to champion through our proof of concept with Combined Arms Support Command’s Force Development Directorate Multi-Function Division lead’s Force Design and Force Structure teams. To assist in laying out a way to map this doctrinal alteration, the 16SB concept illustrated a proven methodology, suppling seven critical node locations with medical supplies far before the contingency stock arrived that was planned from conventional medical logistics distribution. Furthermore, it demonstrated our ability to deliver emergency resupply to Role II clinic assets with direct shipment capabilities. For this year’s DE series, more than 13 occupied countries and 11 ISOFACs across the footprint required CLVIII resupply, in addition to the many Role I assets at outer lying locations. 16SB has successfully filled those gaps through distribution, additional manpower, and streamlining ordering techniques to rapidly provide for sustainment units.
In summation, understanding that there is a reconfiguration of sorts being discussed for the Army’s MLC and sustainment force, the 16SB understood the need to execute a proof of concept early to visualize options and timelines and to be able to execute backfill in this level of medical logistics complexity. In addition to successfully integrating CLVIII into the SSA, 16SB has taken this proof of concept one step further by embedding three 92As into a forward warehouse to replicate efforts into a non-organic SSA more than 1,200 miles away (from Germany to Kosovo). The next hurdle is to transition to Phase III after retrograde operations from DE 21this year and begin Cold Chain Management (CCM) training for temperature-sensitive medical products. The comparison between 68Js and 92As in this proof of concept offers that the CCM and vault procedures are what set the medical communities apart. 16SB is setting out to prove that the 92As and the 68Js can work side by side to expand the medical support and logistics-entwined support capability in any type of operational, semi or non-permissive environment. Our SSA personnel have proven their ability to adapt and operate as a team with the medical logistics community, and there is no doubt that we can be successful in our ability to tackle CCM and vault procedures, one day managing those stocks under a medical logistics officer’s guidance. The most important takeaway in this proof of concept is that mitigating the medical risk across the forward contingency stock for 62 nodes has reshaped our requirement for medical logistics integration in future operations. Questions remain about how future doctrine will change to shape how our warehouses look in the Army’s 2035 and 2050 operating concepts. What we must look to, in answering that question, is how this doctrinal shift is proven successful through streamlining processes across all levels of medical logistics distribution, mitigating the amount of medical risk to a blue-force multi-domain task force or joint forces command-commander across the operational environment.
--------------------
Col. Scott Kindberg is the chief of staff for Army Sustainment Command. Kindberg is an ROTC Distinguished Military Graduate of the University of Wisconsin-Whitewater and holds a Master of Strategic Studies from the U.S. Army War College in Carlisle, Pennsylvania, a Master of Arts in National Security and Strategic Studies from the U.S. Naval War College in Newport, Rhode Island, and a Master of Arts in Transportation and Logistics Management from American Public University in West Virginia. His professional military education includes the U.S. Naval War College, the Joint and Combined Warfighting School at the Joint Forces Staff College in Norfolk, Virginia, and the U.S. Army War College.
Maj. Ericka Bergman currently serves as the brigade medical operations officer for the 16th Sustainment Brigade in Baumholder, Germany. She holds a Bachelor of Science in Physical Education from Pacific Lutheran University and a Master of Arts in Transportation and Logistics Management with a concentration in Reverse Logistics Management from American Military University.
Maj. Kyle McElveen serves as the brigade S2 for 16th Sustainment Brigade in Baumholder, Germany. He is an ROTC Distinguished Military Graduate and holds a Bachelor of Science degree in Social Sciences with a Concentration in History from Campbell University in Buies Creek, North Carolina. McElveen also holds a Master of Arts degree in Military Operations from the U.S. Army's School of Advanced Military Studies (SAMS) in Fort Leavenworth, Kansas.
--------------------
This article was published in the Winter 2022 issue of Army Sustainment.
RELATED LINKS
The Current issue of Army Sustainment in pdf format
Current Army Sustainment Online Articles
Social Sharing