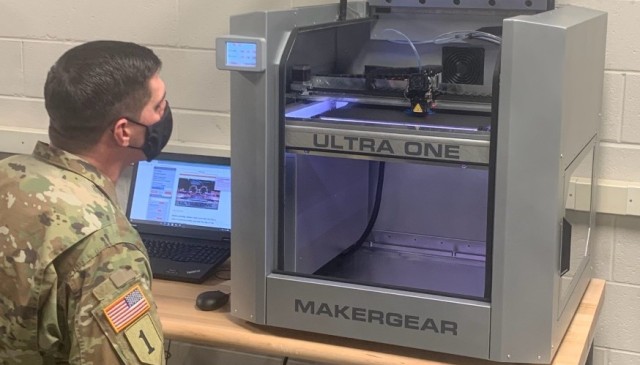
FORT LEE, Va. - The Army Logistics University (ALU) has been training Ordnance Corps Allied Trades Warrant Officers (914A) on advanced manufacturing at Fort Lee, Virginia for approximately one year.
Advanced manufacturing (AdvM) is the marriage of subtractive computer numeric controlled (CNC) machining and additive manufacturing (AM), commonly called 3D printing.
The subtractive side of AdvM is a long-time core competency of 914As, who have been machining precision parts out of metal for many years. Additive technologies add another powerful tool to the 914A’s ability to fabricate parts at the point of need and sustain readiness at the field level.
AM training was added to the Warrant Officer Advanced Course (WOAC) after a small number of 3D printers were fielded to selected units who had a Metal Working and Machining Shop Set (MWMSS) Type II. Chief Warrant Officer 3 Keith Davis was the first 914A to be fielded a 3D printer as part of the limited user evaluation at the 602nd Support Maintenance Company, 1st Cavalry Division in 2018.
“Additive manufacturing is a very useful addition to [the] Allied Trades,” said Davis, who is now a 914A instructor at ALU. “It enables us to better support battle damage assessment and repair (BDAR) and overall readiness during large-scale combat operations.”
Since that initial fielding, AM expanded at a rapid rate. ALU and the U.S. Army Ordnance School responded by adding 88 hours of AM training to the 914A WOAC course. The revised class was first conducted early in 2020 at Cohen Hall on the Ordnance Campus.
914A WOAC students start by using Computer Aided Drawing and Computer Aided Manufacturing software to draw 3D models of parts using either a blueprint or by reverse engineering a physical part. Once modeled, the part can then be CNC machined, or 3D printed. The 914A students fabricate the parts using equipment included in the MWMSS Type II system.
During the course, students also model and print repair parts for various combat systems, mostly from blueprints provided to the instructors. Many parts fabricated by the 914A students are sent for certification by the respective product managers and life-cycle management command, such as the Tank-automotive and Armament Command.
Effective in fiscal year 2021, AM training was also added to the 914A Warrant Officer Basic Course.
The ALU AM training prepares the Allied Trades Warrant Officer to use 3D printing capability once they have been fielded the MWMSS Type II with the AM kit. 3D printing parts at the point of need will fill a critical gap when replacement parts are not readily available. The parts fabricated during the course are uploaded to a digital library so other Allied Trades sections have access to the validated files and can fabricate the same parts.
As a tool to effect BDAR, “3D technology has the potential to alleviate supply chain challenges associated with long lead times and obsolescence,” said Adrian Bailey, Army Futures Command Capability Developer.
Bailey noted that capability developers “strive to incorporate the best emerging technologies into [the Army’s] programs of record to enable Soldiers the greatest flexibility to sustain readiness at the tactical edge.”
Based on current policy, 3D printed parts cannot be used as a permanent replacement. Currently, the Army is limited to various engineering grade polymers for 3D printing at the tactical level. Many of these polymer filaments have strength properties similar to metals but there are some limitations. In the future, it is likely that metal additive technology will be fielded with the MWMSS, which will further increasing the capabilities of the 914A.
The use of AM at the field level is governed by Department of the Army EXORD 050-18 and will be addressed in the upcoming revision of AR 750-1, Army Materiel Maintenance Policy.
Social Sharing