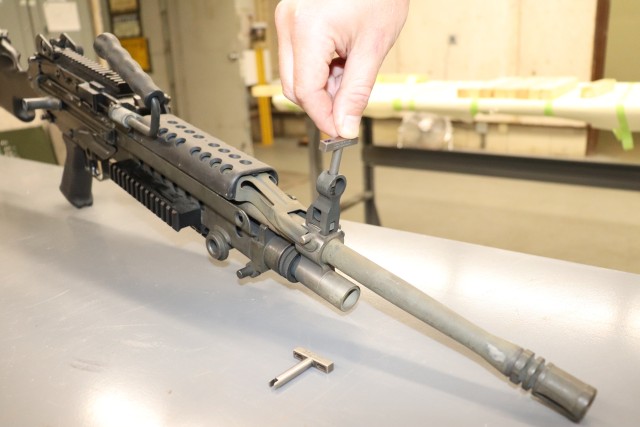
The commanders of Army Materiel Command’s Major Subordinate Commands – the Tank-automotive and Armaments Command, Communications-Electronics Command and Army Aviation and Missile Command – gathered telephonically Oct. 15 to discuss the Army’s Advanced Manufacturing program with reporters from several defense-related publications.
The event was organized as part of the Association of the United States Army annual meeting in which events were conducted virtually, a first for AUSA.
“We’re fully invested in integrating advanced manufacturing techniques into our industrial base and into our supply chain,” stated Brig. Gen. Darren Werner, commanding general of TACOM. He explained that critical groundwork for developing eligible additive manufacturing parts – which types of parts can be produced, certification of those parts, actual printing, qualifying as usable, and ultimately delivered to Soldiers or the industrial base – has been laid.
The Army, Werner said, established a Center of Excellence for Advanced and Additive Manufacturing at TACOM’s Rock Island Arsenal – Joint Manufacturing Technology Center in May of 2019. The CoE currently has 21 3D printers capable of printing polymer, titanium, steel and aluminum and works closely with the Army Futures Command, the Program Executive Office for Combat Support and Combat Service Support and PEO Ground Combat Systems.
“What we’ve done to this point is qualified one specific part,” Werner stated. “It’s been given a stock number and has been provisioned, so a Soldier can order that part right now and we’ll produce it and deliver it to them.”
The process of enabling that first part to be ordered for use in the field may seem like a humble beginning, but the door has been opened for much more.
“We have an additional 48,000 secondary items that are cued up to enter into our critical path to determine whether they’re viable candidates,” Werner explained. “There are additional parts outside of that 48,000 that will evolve over time as we become responsible for that equipment, as well obsolete material that we’ll have to come up with solutions for.”
“Our team looks across the requirements and we identify parts that have long-lead times,” Werner said. “If it takes the (original equipment manufacturers) a significant amount of time to deliver those parts, we look at those as candidates. We look at parts that are unnecessarily expensive because of low demand and, since the OEMs don’t produce a lot of them, traditional manufacturing techniques drive the prices up.”
Additive manufacturing will also allow for battlefield damage service and repair capabilities.
“We are looking at parts that potentially could be re-manufactured or improved or repaired forward using our mobile (Metal Working and Machining Shop Set),” Werner stated. The MWMSS integrates emerging technologies including 3D polymer printing within shipping containers that can forward deploy.
Werner also stated that a newly awarded contract for an infantry squad vehicle included technical data for some of the vehicle parts which should allow for additive manufacturing/3D printing in the future.
“With this new acquisition, we actually will have the technical data for a few of the parts that are on that vehicle,” he said, adding that parts data is currently being entered into a database in coordination with the requirements PEO and will further refine the additive manufacturing information process.
“TACOM’s role in AMC and the Army is to collaborate across the spectrum with our partners, CECOM, and AMCOM to really advance this type of manufacturing to a new level for the Army. We’re taking advantage of technologies to improve Army readiness, resulting in an Army that is more lethal and more agile,” Werner said.
The general officer noted that TACOM’s additive manufacturing capability was also called on to support the nation’s response to COVID-19 earlier this year.
“We were able to produce a significant amount of COVID test swabs and other material to support our nation’s needs,” he said.
Social Sharing