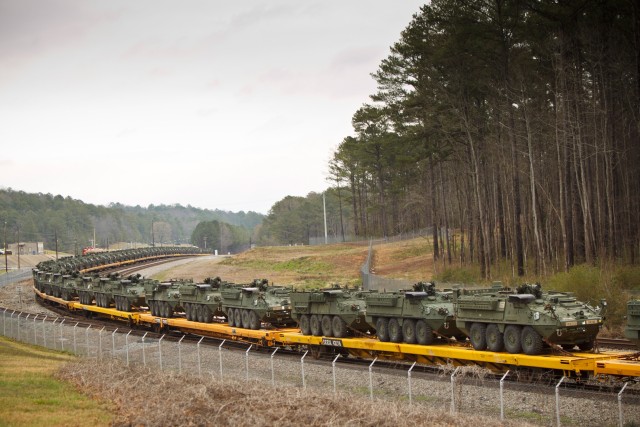
In 2002, Anniston Army Depot and General Dynamics Land Systems formed a partnership centered on a new military vehicle, the Stryker.
The vehicle was named in honor of two Medal of Honor recipients who died in service to their country -- Pfc. Stuart S. Stryker, who served in World War II, and Spc. Robert F. Stryker, who served in Vietnam.
GDLS builds the Stryker's 10 variants new and, from the beginning of the partnership, has utilized the ANAD workforce for a small percentage -- about five percent -- of the labor on each vehicle.
"Our Stryker workload has definitely grown through the years," said David Mize, the depot's Stryker program manager. "When we first began, it was all new production. GDLS built the vehicles and ANAD performed the final paint processes."
A small number of depot employees, about 14, were also cross-trained at that time by GDLS. These employees assisted with production and prepared the depot to eventually assume repair and overhaul missions for the Stryker.
That day came in 2006, when battle- and combat-damaged vehicles first rolled onto the installation for repair and ANAD's piece of the Stryker workload grew dramatically.
BDAR and CDAR vehicles are inspected to determine what systems and portions of the vehicles need new or refurbished parts. The repair work is performed by depot employees while GDLS supplies new parts and components.
In 2009, the depot workload expanded again and the installation's partnership with GDLS changed to accommodate a new type of work -- Stryker reset.
For these programs, the depot and GDLS, working side-by-side, repair, maintain and upgrade the Army's Stryker brigades.
In 2011, the partners celebrated their 1,000th vehicle brought to better-than-new condition through this process.
"Now, we have BDAR, CDAR, test-damaged, accident-damaged, reset, infantry carrier vehicle overhaul, special technical inspection and repair, repair and overhaul at the component level and we are scheduled to complete pilot overhauls for seven Stryker variants this fiscal year," said Mize.
From the 14 depot employees who cross-trained on the Stryker with GDLS employees in 2002, ANAD's Stryker workforce has grown to 260, encompassing a division within the Directorate of Production.
"The Public Private Partnership of GDLS and ANAD has proven to be a win-win situation for both partners. The P3 evolved from the depot's small support operation for General Dynamics on new production into a 50/50 work share on the Stryker Centralized Reset program where we have restored four Brigades of Strykers, for a total of 1,063 war-torn vehicles," said Lee Waldron, plant manager for GDLS at Anniston. "The GDLS team looks forward to a continued future relationship working side-by-side with the professionals at ANAD."
"In addition to the workload and revenue these agreements generate, ANAD has become the Army's designated depot source of repair for the Stryker family of vehicles," said Sonja Freeman, a depot business management specialist.
10 Stryker variants:
• Air-Tank Guided Missile Vehicle
• Command Vehicle
• Engineer Squad Vehicle
• Fire Support Vehicle
• Infantry Carrier Vehicle
• Medical Evacuation Vehicle
• Mobile Gun System
• Mortar Carrier Vehicle
• Nuclear, Biological, Chemical Reconnaissance Vehicle
• Reconnaissance Vehicle
Related Documents:
Stryker Timeline [PDF]
Social Sharing