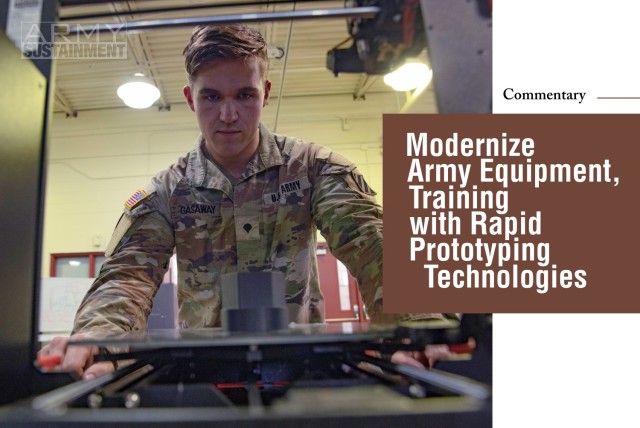
Additive manufacturing, also known as 3D printing, allows users to create physical objects using digital files. The user generates a digital model using computer-aided design software or with an existing item using a 3D scanner. Originally, companies used 3D printing to create prototypes more rapidly. These prototypes can serve as a tooling master, which allows more durable materials to be used. For example, if an engineer designs a new part that must be manufactured out of carbon fiber and resin, they model the object and produce a negative of the model using a 3D printer. This negative is then used as a mold to apply carbon fiber and resin. It is important to remember that although this process sounds complicated, a Soldier can learn how to do this in a single day of instruction for small items, given they have access to the correct equipment.
Unit-level 3D printing
The 3D printing program at the 28th Ordnance Company (EOD) is purpose-built for their needs, and it is an effective example of the widespread utilization of 3D printing at the small unit level. The program balances start-up costs, long-term viability, and overall production.
Brief History and Overview
The 28th EOD started its 3D printing program in 2022 after an Aberdeen Proving Grounds 3D printing conference demonstrated how to use the capability within units. Representatives from the Army, Navy, Air Force, and Marines were in attendance, as well as law enforcement personnel from across the U.S. The sponsors demonstrated various 3D printing solutions, including metal, compact, and large-volume printers. The participants decided a useful program needed to be economical, require little technical expertise, and be efficient with one’s time. These requirements were derived from the things that historically caused programs in the industry to fail: lack of money, training, and time. Money, training, and time are required to 3D print, and the 28th EOD demonstrated a usable model to balance them.
The unit initially purchased three 3D printers and two 3D scanners. Each 3D printer was purposefully chosen to complete a certain task, and the 3D scanners encompassed the two capabilities previously mentioned. Remembering the expendable portions of the 3D printing process is also important. Filament materials and expendables such as nozzles and other components must be forecasted.
PTKM-1R/POM3 Landmines
The 28th EOD saw the need for the program after the discovery of PTKM-1R and POM3 landmines in Ukraine. As a snapshot into potential future conflicts, Ukraine has been illuminating the capabilities of competing foreign countries. These next-level landmines, discovered in April 2022, use advanced technology to target vehicles and personnel. They change the battlespace in a way that necessitates an understanding of them to train and equip U.S. forces properly. The initial estimate, even for priority units capable of paying premium prices, of receiving training aids for these ordnance items was 18 months. Commercial entities move as slowly as the economic process allows them to, and, unfortunately, they are not fast enough to keep up with the initiative of the U.S. military. Using 3D printing, the 28th EOD had a full-scale training aid replica of the PTKM-1R 3D modeled, printed, and in front of Charlie Company, 2nd Battalion, 75th Ranger Regiment in five days. This level of prototyping and flexibility was unprecedented and allowed the unit to adjust to changing conflicts and train on new technologies as they are found, not months after.
The unit has successfully printed 29 different models in various quantities. It has also printed pieces of equipment developed in-house by unit members. These pieces of equipment are not safety-related but instead increase functional implementation of existing equipment, such as night vision covers, cable organizers, shipping aids, battery compartments, etc. These items are used across the organization, and any surplus is given to peer units to bolster their capabilities.
All additive manufacturing projects across the unit have reduced the cost of applicable training aids and equipment by 97% and the acquisition time by 99%. This savings is achievable by all Army units, whether stateside or deployed.
Army Academic Institution Integration
Although 3D printing is not new, many Soldiers must be taught its benefits by introducing them to this technology and its capabilities at Army’s learning institutions, especially leader courses. The curriculum should focus on small unit implementation and the actions of the individual to affect the process at the associated level of instruction. For example, an enlisted Soldier in the Basic Leader Course should learn about resources to provide functional expertise and physically navigate the 3D printing process. In contrast, an enlisted Soldier in the Senior Leader Course should learn to advise on and manage such a program.
In addition to increasing awareness, updating curriculum should include the most recent information across the Army about existing additive manufacturing initiatives, resources available to units, current policies, and examples of successful implementation, like the 28th EOD.
The end goal for modernization instruction at Army learning institutions should be that the most pertinent and current information about improving the Army is shared in an open-forum capacity. This is the structure featured in Army courses, and the curriculum should be shared at the level at which the instruction can reach the most Soldiers to achieve maximum dissemination of information.
--------------------
Staff Sgt. Marcel A. Blood currently serves as an explosive ordnance disposal (EOD) team leader at the 28th Ordnance Company (EOD) (Airborne), 192nd Ordnance Battalion (EOD), on Fort Liberty, North Carolina. He enlisted in the Army in 2011 as an EOD technician. He deployed to Afghanistan in support of Operation Enduring Freedom, to Syria and Iraq in support of Operation Inherent Resolve, and to Afghanistan in support of Operation Freedom’s Sentinel. He is a Distinguished Honor Graduate of the Senior Leader Course, Advanced Leader Course, and Basic Leader Course. He has an undergraduate degree in forensic psychology from Southern New Hampshire University (SNHU) and a graduate degree in industrial/organizational psychology. He is concurrently enrolled in his second graduate program in mental health counseling at SNHU and his second and third bachelor programs in nutrition science and organizational leadership at the University of Arizona.
Editor’s Note: This article was a selection from the Army Sustainment University President’s Writing Competition.
--------------------
This article was published in the Summer 2023 issue of Army Sustainment.
RELATED LINKS
The Current issue of Army Sustainment in pdf format
Current Army Sustainment Online Articles
Connect with Army Sustainment on LinkedIn
Connect with Army Sustainment on Facebook
---------------------------------------------------------------------------------------------------------------
Social Sharing