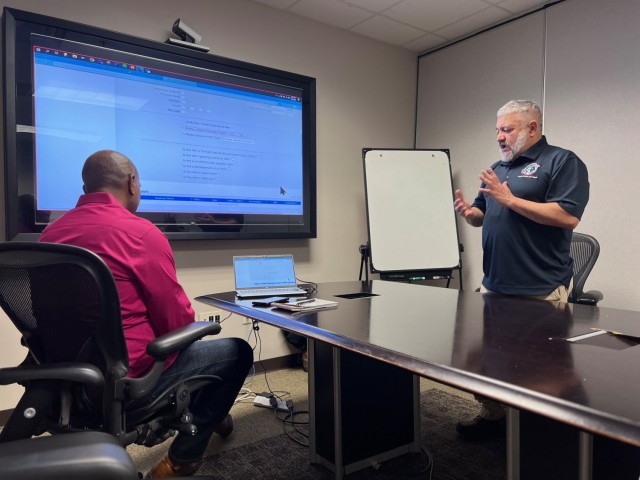
FORT DETRICK, Md. -- In medical logistics, there are many moving parts -- each as important as the next -- to help U.S. Army medical professionals receive equipment and supplies they need to protect and save lives.
And everything starts with information.
Every medical supply item used by Department of Defense agencies and service branches are assigned an NSN, or National Stock Number. Each entry in the Defense Medical Logistics Item Identification System, or DMLIIS, includes vital information about an item -- its description, size of package, manufacturer, price and more.
Correct information can make all the difference in the product ordering process, ensuring a timely delivery, accuracy and accountability for government funds, according to Matthew Diggs, a supply management specialist for the U.S. Army Medical Materiel Agency’s Business Support Office.
“The initial record can be there essentially forever if an item is still procurable,” Diggs said. “That’s why it’s so important that we get the most accurate information possible -- because it’s going to be there for the life of the NSN.”
DMLIIS serves as a repository for all commodities to manage and create new NSNs throughout the Department of Defense. This differs from another system with a similar acronym, DMLSS, or the Defense Medical Logistics Standard Support, which provides for ordering medical supplies and associated logistics functions.
Oversight of the DMLIIS falls under Defense Logistics Agency Troop Support-Medical, which serves as the commodity manager for medical materiel. USAMMA, a direct reporting unit to Army Medical Logistics Command, is the secondary inventory control activity, or SICA, in support of the system.
“We provide continuous support to develop and maintain the federal catalog system and Army cataloging operations,” said Maxine Bowens, data manager for the BSO.
Recently, Diggs and fellow trainer Juan Flores provided training -- both in-person at Fort Detrick and virtually -- for members of Defense Health Agency’s Medical Logistics Directorate. The sessions covered important steps in the cataloging process, such as verifying manufacturers, item descriptions and part numbers when correcting current NSN entries or creating new ones.
“If you’ve never been involved in cataloging, it can get very confusing,” Flores explained. “We’re trying to avoid creating NSNs with incorrect information because that’s not going to help anybody.”
Outdated information can cause any myriad of issues, such as delaying maintenance requests or even spatial issues aboard a Navy vessel where storage is limited.
Sgt. 1st Class Joseph Peer, a clinical analyst for DHA MEDLOG, said its valuable for military and civilian personnel alike to learn or refresh their training on how NSNs are established and answer questions about the process to minimize the potential for kickbacks in the system that could delay purchases.
“This training has been extremely helpful,” Peer said.
Social Sharing