Medical materiel is fielded to the operational force in the form of a medical assemblage (i.e., the bill of materiel within the Global Combat Support System — Army (GCSS-A)). Assemblages are all-encompassing capabilities consisting of expendable items such as bandages, intravenous tubing, and medical equipment components such as pulse oximeter probes or electrocardiograph leads. A medical assemblage also contains durables such as forceps and scalpels or non-expendable items like defibrillators, infusion pumps, and radiographic units that require routine scheduled parts replacements, calibrations, and repairs that require a reliable supply of parts. Each medical assemblage, and its associated items of equipment, is accounted for on the property book within GCSS-A, enabling property accountability, asset management, and the ability to manage all maintenance functions, for the purpose of procuring repair parts and components.
Replacing components of a medical assemblage during the performance of patient care, normal wear-and-tear, loss, maintenance, or damage cannot be performed within GCSS-A because medical materiel ordering is performed through numerous medical supply activities at the Installation Medical Supply Agency, which is usually the local medical treatment facility. When stationed outside the continental U.S., units are typically supported by one of the U.S. Army Medical Materiel Agency’s three medical supply agencies: the U.S. Army Medical Materiel Center (USAMMC) — Europe, USAMMC — Southwest Asia, or USAMMC — Korea. These agencies utilize one or more of several medical supply systems depending on a unit’s location (i.e., the Defense Medical Logistics Standard Support (DMLSS), the DMLSS customer assistance module (D-CAM), or the Theater Enterprise Wide Logistics System (TEWLS)).
Each medical logistics agency uses a local catalog unique to that agency, which may or may not possess the catalog or procurement record necessary to replenish, sustain, or repair originally fielded medical assemblages or equipment. For example, an assemblage may contain an anesthesia unit, but the oxygen sensor provided during the original fielding may not be available through the local medical supply agency. Another way to articulate this is after working meticulously with the Womack Army Medical Center’s staff to source medical materiel needs to sustain a medical mission on Fort Bragg, North Carolina, a unit deploys to another location such as the National Training Center in Fort Irwin, California, Europe, or Afghanistan, where the sourcing is different and uses a different medical catalog from the unit’s adopted medical supply agency, creating gaps within medical materiel needs. Consequently, even when a required item possesses a local catalog record through the local medical supply system, orders may be rejected or canceled by the medical supply system, and units are instructed to produce a new item request (NIR) to develop or reestablish a procurement record, a concept referred to as “fill or kill.”
How can an item the medical logistics enterprise issued or fielded to the organization now be considered a new item when a replacement is required?
As stated above, the underlining cause is that the medical supply system operates under numerous non-standard catalogs and disparate computer systems between agencies. Thus, the agency that originally fields or issues the assemblage is most likely not the agency supporting the organization during the sustainment of the assemblage. Furthermore, the medical supply system does not possess an integrated product support (IPS) or item management (IM) capability at the national level to develop and cultivate a single master catalog. Thus, each local nonstandard medical catalog is cultivated via numerous NIRs, developed over time, unique to each local medical supply agency, by numerous medical customers such as the medical maintainer, medic, or nurse. With this understanding, by developing a medical NIR, one is effectively operating as the medical item manager in a similar manner performed at a life cycle management command (LCMC), such as the Tank-automotive and Armaments Command or the Communications-Electronics Command.
Since the NIR process is utilized to develop and cultivate the medical supply system’s numerous local catalogs, here are a few strategies to develop a sound NIR. It is important to understand approximately 85% of medical materiel provided to the DOD is sourced through the Defense Logistics Agency (DLA). Therefore, if the medical supply system rejects or cancels an order, another vendor contracted with the DLA likely carries the same item. Ironically, under this circumstance, the item being researched is not new, and the catalog record used to develop the original canceled order is no longer sourced, requiring a clinical expert to reestablish sourcing utilizing the NIR process. Conversely, suppose a unit requires an item the local medical supply agency does not offer. In this case, the responsibility also resides with the customer to establish a catalog record utilizing the NIR process.
An important task as the medical customer developing the NIR is to determine if the DLA possesses the desired item within the DLA Troop Support’s Medical Master Online portal to establish sourcing. The DLA is a tremendous partner in the acquisitions of medical materiel, offering numerous sourcing options such as the prime vendor and electronic catalog programs. The medical customer can request access to the portal via a common access card and a short justification. After researching the DLA’s online product listing and potentially finding the desired item, it is helpful to first contact the company or vendor to confirm the identified item offered through the DLA is the item required. Too often, sourcing assumptions made during the NIR process by either the customer or the medical logistician result in the wrong item being provided after ordering. This also impacts other customers, because if a catalog record is sourced inaccurately during the initial NIR process, each follow-on procurement rendered from a poorly sourced record results in the wrong item being procured until the record is fixed.
Many companies provide product listings on their websites, including pictures and detailed descriptions. Furthermore, companies often advertise that they sell to the government and may provide contract numbers and product identifications (IDs) to ease research with the DLA. If explicit sourcing requirements, such as a replacement battery to a fielded automated external defibrillator, are found within a unit’s assemblage, phone calls or emails with the company or vendor are appropriate to determine specific technical factors such as whether a specific battery can be utilized between models. To aid in sourcing research, the DLA’s website and the DMLSS system both provide company or vendor contact information such as email addresses, phone numbers, and website addresses to aid in the research. Another option afforded to the DOD customer is the ability to procure materiel directly from DLA’s web services without the need to develop a lengthy NIR with a local medical supply agency in a similar manner as other classes of supply offered by the DLA, such as FedMall, or through the Government Services Agency website.
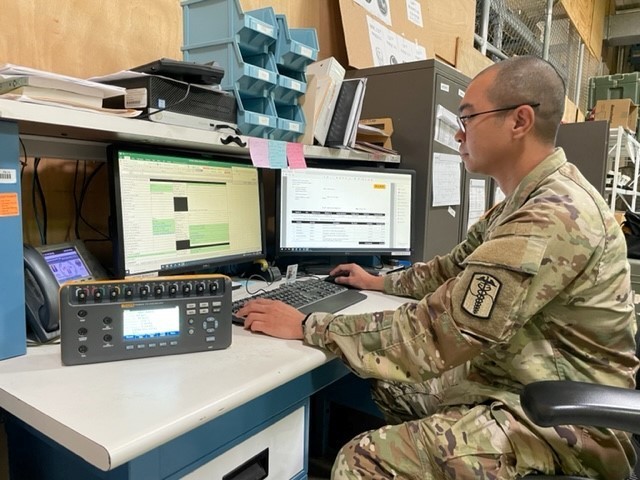
property lateral transfer within Global Combat Support System — Army on March 17, 2022. VIEW ORIGINAL
As stated earlier, the DLA accounts for approximately 85% of the Army’s medical supply needs. Thus, it is inevitable a sizable portion of medical materiel requirements to sustain the Army’s fielded medical assemblages are not sourced by the DLA. Local vendors are the most likely sourcing methodology leveraged to procure materiel outside of DLA’s portfolio, often through the government purchase card (GPC) program or some other established contractual vehicle such as a Blanket Purchase Agreement. Local medical supply agencies provide specific procedures on how to craft an NIR and how subsequent procurement documents should be developed. For example, a local GPC program may require one to three quotations from industry, depending on the cost threshold.
After performing the necessary research with the DLA and industry, it is time to develop an NIR. As stated earlier, the medical supply system is inherently a local and manual business model. Thus, it is important to consult with the local medical supply agency for specific guidance and formatting on developing an NIR. However, at a minimum, the medical logistician requires the item’s name, manufacturer product ID, and point of contact to include phone numbers, email, websites, and unit price. Some medical supply agencies may require additional information such as the product’s weight, dimensions, and end item information such as model number and voltage. Moreover, depending on local policy, justification and leadership endorsement may also be necessary.
Once an NIR is accepted by the local medical supply agency and an actionable catalog record is successfully developed or reestablished within either DMLSS or TEWLS, the D-CAM catalog must be updated or synchronized with the local medical supply agency to ensure the unit possesses the new record within the broader local catalog. At this point, units can place their order or reestablish the originally canceled order.
The Army requires a medical materiel requisition capability fully integrated with the rest of the Army’s logistics functions to facilitate the Army's total mission. The Army can achieve this by first elevating the IPS and IM functions currently performed at the tactical level by numerous medics, nurses, or medical maintainers to a national level Medical LCMC, cultivating a single cataloging and sourcing concept within the Federal Logistics Information System to develop standard national stock numbers, similar to all other classes of supply. This Medical LCMC should ensure, at a minimum, that medical materiel necessary to sustain the Army’s current medical assemblage construct and medical equipment fleet possesses a catalog record and is appropriately sourced to the nation’s industrial base to include materiel beyond the DLA’s portfolio. The Medical LCMC would then collapse numerous medical supply systems that facilitate the current local medical supply business model within the operational force and replace them with GCSS-A to enable a clean enterprise-wide medical supply business model compatible with the Army’s logistics architecture.
--------------------
Chief Warrant Officer 4 Kevin O’Reilly currently serves as the brigade maintenance officer for the 65th Medical Brigade. He has deployed to Iraq and Afghanistan with the 82nd Airborne Division, 44th Medical Brigade, and 1st Medical Brigade. He served as the Chief for the Equipment Management Branch at the Kimbrough Ambulatory Care Center in Fort Meade, Maryland, and in Landstuhl, Germany. He holds a master’s in data analytics and a doctorate in business from the University of the Incarnate Word.
Chief Warrant Officer 3 Dae Kim is the property book officer for the 65th Medical Brigade. Kim has deployed to the United Arab Emirates with the 108th Air Defense Artillery Brigade, Iraq, the U.S. Army Security Assistance Command, and the 10th Mountain Division. Kim holds a master’s in business administration from Fayetteville State University, North Carolina.
--------------------
This article was published in the Fall 22 issue of Army Sustainment.
RELATED LINKS
The Current issue of Army Sustainment in pdf format
Current Army Sustainment Online Articles
Social Sharing