Maintenance operations in Arctic winter conditions carry unique challenges. This article will present what distinguishes extreme cold weather (ECW) maintenance from temperate field condition maintenance. The specific methods and requirements mentioned in this article for conducting maintenance in ECW are primarily based on feedback and experience of subject matter experts currently operating in Alaska. There are multiple variables, such as the need for heated maintenance shelters, thawing vehicles, and longer work-rest cycles due to ECW exposure which can affect the speed and throughput of repair for any piece of equipment. Understanding these challenges will help better prioritize personnel and equipment to support maneuver operations in the Arctic winter. This article is intentionally focused on performing maintenance at the brigade support battalion (BSB) level and, therefore, does not address vehicle recovery and its associated mobility limitations and constraints. As the U.S. Army pivots to the Arctic strategy, it is critical that maneuver and logistics professionals understand the cascading effects of ECW on personnel, equipment, and planning sustainment timelines.
Heated Maintenance Shelters
Heated maintenance shelters are required to conduct maintenance in ECW field conditions. Heated maintenance shelters prevent cold-weather injuries to maintenance personnel, bring equipment up to safe handling temperatures, and enable efficient and timely maintenance without the interference of wind-borne debris and extreme cold. The BSB utilizes light-weight maintenance enclosures (LME), commonly referred to as Field Maintenance tents. In addition to the LMEs, the BSB has a forward repair system (FRS) that can act as a limited heating enclosure. The FRS itself has a heating capability, but external tentage is required to contain the heat sufficiently to support maintenance operations in ECW. The LME and FRS systems do not provide insulation and require two to three 120,000 British thermal unit (BTU) heating systems to keep internal ambient temperatures above freezing. Without these heating systems, the LME will not stay warm enough to conduct larger jobs such as engine swaps for High Mobility Multipurpose Wheeled Vehicle, Light Medium Tactical Vehicle, and Load Handling System. The FRS on their own provide the capability for small repairs such as battle damage assessment and repair but leave maintenance personnel exposed to colder temperatures. The absence or presence of heating sources in LME and FRS shelters will determine work-rest ratios and man-hours, affecting repair throughput.
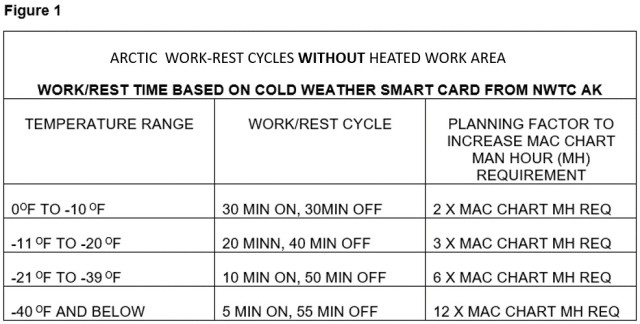
Equipment Thawing Time
Understanding equipment thawing time (ETT) is essential to conducting field maintenance in ECW. ETT is an important limiting factor in conducting maintenance in ECW. Thawing can take 2 to 12 hours, depending on shelter temperature. Thawing time refers to bringing a piece of equipment into a heated maintenance area and allowing it to warm up to ambient temperature. Doing this prevents damage to the equipment due to “cold induced brittleness” of the materials. Also, it reduces the risk to maintenance personnel of incurring contact frostbite from handling equipment and materials initially at sub-zero temperatures. It should be noted that the BSB’s current available LMEs require the use of commercial off-the-shelf heaters. No matter how many LMEs you have in a field environment, ETT will reduce repair throughput in Arctic winter conditions. This extremely critical factor is not accounted for in the Army maintenance allocation chart.
Cold Weather Work-Rest Cycle
Finally, in ECW, maintenance personnel should conduct shortened work iterations followed by rest and rewarming cycles to prevent cold-weather injuries. These work-rest cycles are dependent primarily on the wind-chill computed real-feel temperature, type of equipment being repaired, and the level of acclimatization of the service member performing the maintenance task. Once temperatures drop below freezing, the risk of cold weather injuries increases; once temperatures drop below zero, the risk increases exponentially. Conducting maintenance in outdoor ambient temperature poses the highest risk of cold weather injury, and service members conducting repairs must wear contact gloves to safely touch vehicle parts. Even with the best personal protective equipment, the prescribed work-rest cycle for sub-zero temperatures, shown in Figure 1, substantially increases to the man-hour requirement for any given job. The purpose of Figure 1 is to act as a guide for safe work-rest cycles for maintenance personnel operating in ECW and highlight the impact on work throughput. The table specifically addresses maintenance conducted in the open without shelter or heat source. The work-rest cycle describes the maximum safe time a mechanic can work “ON” the equipment followed by the minimum required time “OFF” they need to warm up before resuming work. The third column on the chart shows how the required work-rest cycle impacts the established man-hour requirement detailed in the Man-hour Allocation Chart (MAC) located in the Technical Manual for that specific piece of equipment.
Conducting maintenance in LMEs with a heating source reduces the risk drastically, but this depends on what temperature you can maintain inside the LME. Another factor in considering the work-rest cycle while conducting maintenance in an LME is the addition of a hand-warming heater station for maintenance personnel. The improvement of productivity using a heated shelter is shown in Figure 2. The information on Figure 2 acts as a guide for safe work-rest cycles for maintenance personnel operating in ECW and highlight the impact to work throughput. This table specifically addresses maintenance conducted in some type of enclosure or shelter with a heat source that raises the ambient temperature of the enclosure above environmental and provides an additional nearby heat source to allow the mechanic the ability to periodically warm their hands in order to continue working. The work-rest cycle column describes the maximum safe time a mechanic can work “ON” the equipment followed by the minimum required time “OFF” they need to warm up before resuming work. The third column on the chart shows how the required work-rest cycle impacts the established man-hour requirement detailed in the Man-hour Allocation Chart (MAC) located in the Technical Manual for that specific piece of equipment.
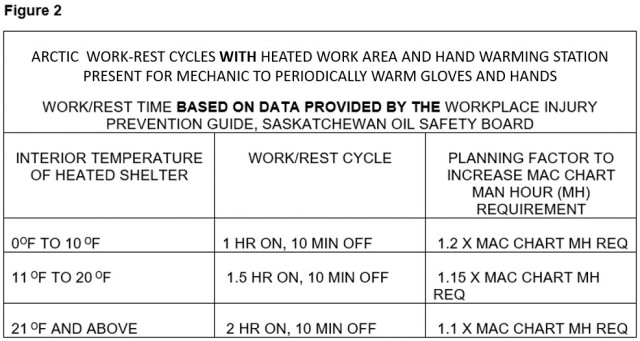
Whether maintenance is conducted outside or in an LME, leaders who are not hyper-vigilant on work-rest cycles expose service members to cold weather injuries. The loss of personnel will affect equipment repair timelines.
Logisticians planning for operations in the Arctic winter must understand the cascading effects of ECW on personnel, equipment, and planning sustainment timelines. As discussed, variables such as heated maintenance shelters, thawing vehicles, and work-rest cycles due to ECW exposure can affect repair speed, man-hour requirements, and equipment repair throughput. Furthermore, the Army maintenance allocation chart does not capture ECW planning factors that increase man-hour requirements. As the Army pivots to the Arctic strategy, maneuver and logistics professionals must understand the increased planning factors ECW to deliver the required effects to maneuver commanders.
Recommendations
Although there is limited research on Army maintenance in ECW, we have gained first-hand knowledge on the subject as the senior sustainer for our Arctic brigade. A battalion task force was utilized for our 2020 extreme cold-weather exercise. We concluded that LME maintenance was critical for conducting larger repairs while increasing the speed of repair throughput. Small repairs could be conducted in our FRS; however, the curtain system does not trap the heat well and is not optimal for repair. We concluded that our forward logistics element had a rate of repair of nine vehicles per day based on the BSB organic assets (two LME and one FRS). We eliminated one vehicle space of the 10 available for battery pallet chargers because the extreme cold temperature conditions necessitated additional battery charging capabilities.
Based on our experience in an arctic airborne BSB, there are three general points that all Army leaders must consider for operating in ECW environments:
- The Army Maintenance Allocation Chart does not account for repairs in extreme cold weather temperatures. It should include general consideration for repairs inside an LME and in the open. This is critical for leaders to account for the significant reduction in maintenance throughput due to ETT and work-rest cycles.
- The Army must add a program of record for bullet heaters, improve heating systems for our LME, improve the FRS curtain system, and upgrade the FRS heater with higher BTUs.
- BSBs and forward support companies require additional ground support equipment mechanics to support the repair of heating ventilation, air conditioning systems, quartermaster machinery, heaters and other related equipment enabling adequate personnel replacements due to cold weather work-rest cycles. Equipment thawing time (ETT) is a planning factor in repairing combat power for maneuver commanders. ETT must be understood by all echelon leaders while considering that conducting any operation in extreme cold weather takes 30 up to 1200 percent more time than operations in temperate weather.
--------------------
Lt. Col. Ralphael Jimenez is currently serving as the commander of the 725th Brigade Support Battalion (Airborne), 4th Infantry Brigade Combat Team, Jimenez’s military and civilian education includes the Armor Officer Basic Course, Captains Logistics Career Course, Major’s Intermediate Level Education, bachelor's in marketing from Inter-American University of Puerto Rico, Master of Business Administration degree from the prestigious Major General James Wright Fellowship Program at the College of William and Mary, and Lean Six Sigma Green Belt.
Capt. Alexander Banks is the deputy support operations officer of 725th Brigade Support Battalion (Airborne), 4th Infantry Brigade Combat Team. His military education includes Ordnance Officer Basic Course, Cold Weather Leader’s Course, and Captains Career Course and Lean Six Sigma Black Belt. Capt. Banks holds a bachelor’s in Mechanical Engineering from the University of Idaho.
Chief Warrant Officer 4 Brian Cox serves as the senior ordnance ground maintenance officer for the 4th Infantry Brigade Combat Team. Cox is a graduate of all Warrant Officer Professional Education Courses and is a Demonstrated Master Logistician. Cox has completed the Capabilities Developers Course, Industrial Business Based Logistics Course, Operational Contract Support, Contracting Officer Representative, and Joint Logistics Course.
--------------------
This article was published in the Spring 2022 issue of Army Sustainment.
RELATED LINKS
The Current issue of Army Sustainment in pdf format
Current Army Sustainment Online Articles
Social Sharing