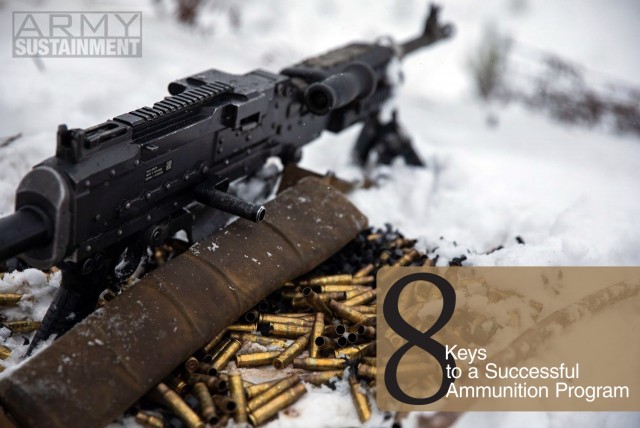
During the first day of command of Hotel Forward Support Company (FSC) in support of 1st Battalion (BN), 77th Armored Regiment in 3/1 Armored Brigade Combat Team at Fort Bliss, Texas, my distribution platoon leader and the BN master gunner (MG) walked into my office and said, “we are going to fail our gunnery ammo draw.” We had unknowingly put an armor heavy combined arms BN’s worth of gunnery ammunition on one document, and we did not have enough organic trucks or people to complete the draw. We did not fail the draw from the ammunition supply point (ASP), but it took assistance from three additional FSCs to successfully draw the ammunition.
It was clear we needed to put a little love and a lot of effort into improving our Class (CL) V ammunition program. One year later, the FSC executed another gunnery with additional maneuver and tactical lanes requiring more than 150,000 rounds with more than ten different DOD identification codes (DODIC). In total, our BN drew nine documents. When it came time to turn-in, we had zero deficiencies, clearing all documents. The BN had accounted for all ammunition and residue, making 1st BN, 77th Armored Regiment the only unit in our brigade to properly account for all our ammunition.
So, what changed?
The following are the eight key factors we improved or implemented to make our CLV program a success.
1. FSCs and Master Gunners Must Become Best Friends
Ammunition allocation looked like this—companies generated ammunition requirements based on upcoming training using the BN training resource meeting. They communicated this through the company executive officer (XO) to the BN MG, often the BN’s ammunition NCO as an additional duty in the S-3. The MG reviewed and added additional ammunition required for larger unit events such as BN gunnery. Often the CLV allocation process stops here—but there is another step. Next, the FSC XO and/or distribution platoon leader brief capabilities. These capabilities include ammunition handlers and DD626 equipment. DD626 is the standard vehicles must pass to transport ammunition. This information drives the decision on an ammunition documents composition. This is where our unit went wrong. The FSC did not communicate these capabilities before the document “dropping” in the Total Ammunition Management Information System (the Army’s CLV allocation system), and the BN didn’t know to ask. Neither entity knew what they were missing until it was too late. We never made this mistake again. From then on, the MG was on the FSC’s speed dial. The MG/ammunition NCO must understand the capabilities and limitations of the FSC’s equipment and personnel to compose and “drop” each document properly. We then planned CLV operations; this team included the FSC commander or XO, the FSC distribution platoon leader or platoon sergeant, and the BN MG. The BN S-4 is also a good addition to this working group; however, while resourcing requests usually go through the S-4, CLV, specifically, is requested and tracked through the S-3. Regardless, having the S-4 in the loop is beneficial.
2. Identify all Limitations and Constraints
The group must identify all unit limitations and outside constraints with the key players on board during the planning process. The ultimate goal is to ensure all ammunition is on a document size the FSC can realistically draw, issue, and turn-in. The largest limitation for an FSC is a lack of equipment that passes DD626 standards and personnel properly licensed as ammunition handlers. These two elements are needed to transport ammunition legally. Constraints placed on the FSC from outside entities may differ based on location, higher headquarters standard operating procedures (SOPs), and more. The most common constraints while planning includes the following:
- Like-type ammunition. Keep like-type ammunition on one document (or as few as possible). This decreases the chance of receiving different lot numbers. Fewer lot numbers for like-type ammunition decreases the chance of mixing the same ammunition and residue from different documents; this simplifies accountability and preparation before turn-ins. As you draw from the ASP, pay extra attention to lot numbers to confirm all lot numbers are annotated correctly on your documentation.
- Storing CLV. Live ammunition must be guarded or secured at all times. While this is simple for small arms ammunition, larger bullets (such as 25MM and 120MM needed for Bradley’s and tanks, respectively) are more complicated. ASPs typically have guarded and secured cages attached to or located near their area. However, don’t be fooled; DD626 equipment is required to store all CLV in these locations, rendering any platform there unavailable for additional draws. Often, storing CLV requires personnel to go to the field early to guard ammunition if a brigade-level ammunition holding area is not established. This should be brought up to the brigade’s ammunition warrant officer, who sits in the support operations (SPO) section in the brigade support BN. As they look at trends across the brigade, this information helps direct the CLV plan at higher echelons.
- Time-Distance Analysis. While some ASPs are located near the cantonment area and training ranges, other installations require a longer drive. At Fort Bliss, Texas, the second-largest Army installation, the ASP was a minimum of a 45-minute drive in a tactical convoy, and the training ranges were anywhere from a one- to three-hour additional drive one-way. Burnout of the distribution platoon must be taken into consideration.
- Flexibility and Expectation Management. MGs, or a BN S-3 representative, bring the maneuver plan to the table. This maneuver plan should generate and construct the sustainment plan. However, once key events (i.e., draws and turn-ins) for CLV are scheduled and outside the user’s control, the sustainment plan often cannot be changed, decreasing flexibility. The timelines built for an operation (i.e., gunnery table layout, transition days, maintenance hours, etc.) provide the framework around which sustainers build their support plan. However, at the most basic level, these timelines are based on the achievement of certain metrics (i.e., all crews through Table V and ready to transition early to Table VI). The achievement of these metrics triggers transitions. If triggers are initiated early or late due to unforeseen circumstances, often, the sustainment plan cannot react—sustainment planners must get ahead of this! Take into consideration the most common contingency plans for the maneuver timeline and incorporate those “what ifs” into the plan. Each document must have a draw no earlier than, draw no later than, and optimal draw date. Very simply, do not be the reason the maneuver plan is held up—and if you are, communicate and build in flexibility. Communicating these hard dates early through the planning process could make this potential problem disappear before it can even appear. The FSC commander often does this through BN leadership during the orders process and daily sync meetings.
- Special drawing requirements. The little details, if missed, can cause a unit to jump through hoops to make a draw happen. For instance, live grenades must have an armed guard to draw and transport. CS gas capsules require personnel to have full mission-orientated protective posture gear within arm’s reach. It’s good practice to have these special DODICs on the same document. For example, allocating hand grenades on two documents would require two separate armed guards and two additional vehicles to draw and transport the ammunition. Make it simple and put them all on one document.
Now, put this together and get planning.
3. Find the Sweet Spot
While our unit’s original problem was that all our ammunition was on one document, more documents may not always be the answer—find the sweet spot for each exercise. There is a point where too many documents provide a diminished return to the FSC. Fewer, and therefore larger documents, create potential problems if equipment “goes down” during training resulting in the FSC unable to move the document. However, too many documents drastically increase the workload of the distribution platoon. Roughly speaking, regardless of size, each document takes 4-6 working days to handle properly—not counting the days used on a range. A rough breakdown of these days looks as follows:
- Day 1 – Distro prepares their vehicles for the draw (DD626 inspections, Pre-combat checks/Pre-combat inspections, dispatching, etc.).
- Day 2 – Ammunition is drawn from ASP (at Fort Bliss, Texas, this began before physical training hours and usually took until the afternoon to complete).
- Day 3 – Distro issues ammunition to the maneuver companies, completing a full inventory.
- Day 4 – Following training, maneuver companies turn-in ammunition to the distribution platoon to complete a full inventory.
- Day 5 – Distro preps equipment and ammunition for turn-in.
- Day 6 – Distro and a tasked BN-level detail conduct ammunition turn-in to ASP (larger documents are often rolled over to a second day).
Note: At Fort Bliss, each document required an 18-Soldier detail to assist in the turn-in process. This could be decreased only with the ASPs approval for smaller documents and these details should be tasked through the S-3 shop to all companies within the BN.
During our bi-annual BN gunnery training cycle, it was common for the FSC’s distribution platoon to be in the field upwards of two weeks before the training and an additional 2–3 weeks post-training strictly because of CLV.
4. Turn your Limitations into Strengths
- Cross-train non-88M and 89B military occupation specialties within the FSC as ammunition handlers.
The FSC must coordinate with the SPO to schedule an ammunition handler class and push as many additional personnel through the course as possible. This increases flexibility across the FSC to pull from other sections to transport ammunition if the distribution platoon is fully tasked. For Hotel FSC in a COVID-19 environment, unforeseen quarantines would decrease our personnel capability within a section. Having those extra ammunition handlers in the distribution, maintenance, and headquarters platoons were key to our success during the execution phase. Flexibility can also be achieved across the BN. Maneuver companies should have no less than one NCO and one Soldier ammunition handler certified as they are required to man and run their ammunition issue point (AIP). This also allows maneuver companies to transport their ammunition to smaller ranges. The same applies to DD626 equipment—it is advantageous for maneuver companies to have at least one vehicle up to DD626 standards.
- Designate DD626 Platforms as Pacers
DD626 is the standard a vehicle must pass to transport ammunition. It is a detailed form checking for much more than “is the truck fully mission capable (FMC)?” Just because a vehicle is FMC does not mean it is up to DD626 standards. Slash faults can fail a vehicle during a DD626 inspection, which can cause a unit to fail a draw or turn-in. FSC commanders should already be prioritizing equipment based on mission requirements. They need to brief both FMC and DD626 platforms weekly during the planning phase and daily during the execution phase of the operations, as those numbers are usually different. But, for a truly successful ammunition program, BN level leaders, most importantly the BN commander, XO, and maintenance technician, must designate the distribution platoon’s DD626 vehicles as pacers, choosing, when appropriate, to make the hard decisions to prioritize sustainment platforms over combat platforms. This emphasis and prioritization were implemented in our unit’s second gunnery with the full support of the 1st BN, 77th Armored Regiment senior leadership. At one point, the FSC’s DD626 vehicles were deemed the priority over other combat platforms. This enabled the FSC to bring trucks up to DD626 standard resulting in successful draws and turn-ins, increasing the lethality of our BN.
5. The Necessities No One Talks About
Distribution platoons must order the required equipment for their trucks not found in their truck’s basic issued items, such as ammunition placards and additional tarps and fire extinguishers. However, certain extra equipment can elevate an ammunition program from good to great. Scales and buckets should be ordered to weigh dunnage accurately. Without these items, the distribution platoon cannot properly clear maneuver companies of their DD Form 5515, Training Ammunition Control Document, leading to confusion regarding who was responsible for potential deficiencies. Extra SurePaks with lids, ordered CLII through the supply system, can be used to hold sorted dunnage. Labeling the type and quantity of dunnage on each SurePak streamlines turn-ins. The ASP residue workers gave our unit accolades for our organization due to this simple idea. Other items that increase efficiency can be built. Our distribution platoon built a dunnage sorting table similar to the one used at the ASP from old wooden pallets and leftover plywood from blocking and bracing containers. This decreased the time it took to sift brass before a turn-in—a process usually done a minimum of three times. Building this table also helped prevent the BN from “failing a turn-in.” At the Fort Bliss ASP, five live rounds found in any dunnage below .50 caliber, regardless of the document size (at times dunnage rounds were in the tens of thousands), was grounds for a unit to fail a turn-in at the ASP and to come back another day.
6. All Companies Must Buy In
When CLV is viewed as an “FSC problem” instead of a collective battalion operation, you’ve already lost. Designate company XOs to sign for all ammunition issued to their company (through the unit SOP signed by the BN commander). Company XOs, usually former platoon leaders, have property accountability experience; ammunition is property and should be treated as such. Having a company-level leader sign for all CLV on a DA Form 5515 (and then signed down) decreases ammunition’s chance of mishandled as higher-level leaders have a vested interest in its proper maintenance and accountability.
7. Give the AIP a Little Love
Maneuver company ammunition handlers should be assigned to run their company’s range AIP. This is not the job of the FSC. Range operations personnel inspect all required documents and equipment to keep the AIP within the standard. However, that does not mean an AIP is run effectively. Similar to point five, AIPs should have boxes to sort dunnage as it comes off the range. Ammunition handlers should issue no more than the necessities needed to conduct training. Residue items such as bandoleers and plastic inserts are accountable items when ammunition is turned-in to the ASP. These items should never leave the AIP if possible. Ammunition cans fall into this category too. If an ammunition can is needed to use a weapons system effectively, plan and request these cans from the ASP. With a simple memorandum usually signed by the BN commander, ammunition cans can be given to each crew to keep. This keeps the ammunition handler from needing to issue out cans, keeping full accountability of them. Big bullet ranges, such as a tank range, often require a little more attention. 120MM tank rounds come in banded honeycombs forklifted onto a container roll out platform (CROP) at the ASP. One CROP can fit two honeycombs wide and four honeycombs lengthwise. Ammunition handlers in charge of the AIP must be cognizant of taking an even amount of 120MMs out of each side of a CROP. If they issue 120MM from only one side of the CROP, the CROP can no longer be moved. The lopsided weight makes it impossible for a Load Handling System (LHS) or Palletized Load System (PLS) to lift the CROP. If the range is cold, the solution to this problem requires either a forklift (usually found back in the Motorpool with the maintenance section) or un-banding honeycombs to move them by hand and re-banding them, leading to accountability nightmares. Additionally, ammunition should be used one full CROP at a time. If one live round is left, the whole CROP is considered “live” ammunition, forcing the distribution platoon to use a DD626 vehicle to transport the live ammunition, whereas dunnage can be transported by any vehicle.
8. Take Responsibility and Work as a Team
Holding individuals accountable for their actions motivates them to adhere to proper processes and procedures. If the FSC is the only company on the “red carpet” regarding ammunition, they are fighting an uphill battle—maneuver companies must also have a vested interest. This only happens when the FSC properly signs down ammunition on a DA Form 5515 and accurately clears a unit noting any deficiencies. As the FSC, we would inform the maneuver commander of their deficiencies and then brief the BN commander on those same deficiencies giving full transparency on our document progress. This also flattened communication and enabled other companies to track deficiencies across the BN in case residue or dunnage happened in their area of operations, a common occurrence if two armored companies were sharing the same range. As the FSC, we also briefed our deficiencies and took responsibility for our mistakes. This transparency at all levels allowed everyone to be on the same page and make CLV accountability a team effort.
Litmus Test
The ammunition program is vital to the overall success of any combat arms unit’s maneuver mission; in addition, this program, like many others, can point toward the true culture in an organization. Reactions within a unit to simple processes such as maneuver companies signing for ammunition, running their AIPs on ranges, and briefing their deficiencies inherently bring to light the relationship between the maneuver companies and the FSC, and the overall culture of the BN. When sustainers are viewed as equal partners with their maneuver counterparts and the unit identifies the importance of everyone’s role in the mission’s overall success, that organization thrives. The ammunition program within a BN is a good litmus test for this. 1-77th Armored BN passed this litmus test. With honest and positive BN and company leaders holding their subordinates to the standard, our ammunition program drastically improved because we worked together as a team. Soldiers, NCOs, and officers from each company were advocates for proper accountability of CLV, and it showed in our results. These eight key factors have the potential to streamline your unit’s ammunition program, directly impacting the unit’s lethality. These factors also enable your team to work together toward a better culture.
--------------------
Capt. Sarah Antioho is currently the primary distribution company Observer Coach Trainer at the Joint Multinational Readiness Center in Hohenfels, Germany. Antioho commanded Hotel Forward Support Company, 1st Battalion, 77th Armored Regiment, 3rd Brigade Combat Team, 1st Armored Division at Fort Bliss, Texas, from January 2020 to May 2021. She holds a bachelor’s degree in English Literature from Wheaton College in Illinois.
--------------------
This article was published in the Winter 2022 issue of Army Sustainment.
RELATED LINKS
The Current issue of Army Sustainment in pdf format
Current Army Sustainment Online Articles
Social Sharing