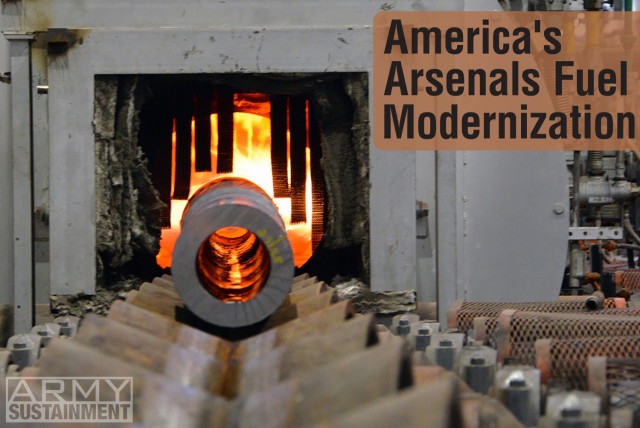
The Army’s organic industrial base (OIB)—23 arsenals, depots, and ammunition plants that manufacture, reset, and maintain Army equipment—provides critical materiel and sustainment support to warfighters across the joint force. While the OIB is essential to meeting current needs and national defense strategy requirements, it must modernize now to meet the needs of the future force in a multi-domain operations (MDO) environment.
OIB modernization directly aligns with the Army’s priorities of people, readiness, and modernization and postures the Army to respond to the evolving demands of future warfare. However, modernization does not happen overnight—as with an oak tree, planting a seed is the first step in the years of care and development needed to reach full potential. Through a 15-year OIB modernization plan nested with the Army’s modernization strategy, Army Materiel Command (AMC) is planting that seed and modernizing facilities, processes, and people to bring the OIB into the 21st century, infuse industry best practices and refine human resource management structure to maximize the skills and capabilities of our workforce.
Time to Modernize
As Army Chief of Staff Gen. James McConville said last October, “the time has come for transformational change to build the Army we need for the future, [because] winning matters.” The Army has set 2035 as its goal to transform into a MDO-capable force. The time is now to modernize our OIB facilities, processes, and people to institute the transformational change needed to support the future force. We must prepare ourselves now to surge or risk being late to need when called upon.
We are focusing our modernization efforts on projects that are most critical to support current readiness and posture capabilities to remain relevant for the Army of 2035 and beyond. To do this, we developed a 15-year OIB modernization plan that focuses investments on the most critical projects that will yield the right effects in the OIB and ensure our facilities and workforce are ready to meet the needs of the future force.
The plan looks holistically across the OIB and uses a four-phase approach to identify, evaluate, analyze, and develop a schedule to incorporate emerging technologies into our facilities, from industrial operations to installation and cybersecurity, energy and power resilience, and more. The end state is a comprehensive OIB investment plan that sustains the artisan workforce, maintains pace with the Army’s modernization of weapon systems, and enables surge capacity for large-scale combat operations. Today’s decisions are setting the course for the OIB over the next 40 to 50 years in support of the Army’s modernization efforts.
Transformational Change
To move the OIB into the 21st century, we need persistent and purposeful modernization, not incremental updates, to achieve transformational change across our facilities, technology, and data. The OIB modernization process seeks to leverage commercial innovation and cutting-edge science and technology to achieve the right results.
Staying integrated with the Army’s modernization priorities is essential to the OIB. We must resource and modernize the OIB today to provide capabilities that will support and sustain the next generation of equipment. We are responsible for developing the industrial base that will support the platforms Army Futures Command is bringing to fruition over the next 5 to 20 years, and we cannot wait until after they arrive.
At Watervliet Arsenal, the installation has already installed new machines to increase cannon production capacity in support of long-range precision artillery and future requirements. This is a good first step that must be replicated across the OIB. Maintenance bays at Corpus Christi Army Depot (CCAD) must be fitted and ready to maintain future vertical lift aircraft. Ammunition plant production lines must be prepared to produce the right size and scale of ammunition for the next generation squad weapon. Across every modernization priority, our OIB must be ready.
Modern Facilities. The OIB consists of more than $30 billion in facilities and infrastructure, much of which was built more than 70 years ago. These older facilities are not designed for modern best practices, and the increased workload of the last 20 years accelerated the aging of facilities and equipment, especially in our ammunition OIB. To modernize the facilities, we are developing an end-to-end list of required improvements, considering the entire workflow process, prioritizing each OIB’s core competencies, and understanding the requirements to meet a future surge. Throughout this process, we are also focused on and committed to protecting our critical capabilities and reducing single points of failure.
We are reassessing the area development plans to the master development plans in a totally modern approach by incorporating 21st-century industry standards, balanced against planned funding, then investing in consistent and persistent modernization efforts. Our goal is to have flexible, multi-purpose facilities with lines that have the capacity to do different functions, meet the evolving needs of the Army and ensure the safety of our workforce. For example, CCAD uses available technology such as robotics and automated blue light scanning to develop multipurpose assembly and disassembly lines. At the Crane Army Ammunition Activity, the workforce has successfully tested a robotic arm to demilitarize out-of-service ammunition like anti-personnel rounds.
New facilities and upgrades also will address the complex and diverse problem of climate change by improving energy resiliency, particularly electricity and water consumption, saving energy and money for the Army. Tobyhanna Army Depot is working with industry to eliminate oversized steam boilers, adding cooling system improvements to expand its utility monitoring and control system to provide enhanced monitoring and control capabilities. These efforts are projected to reduce the depot’s energy consumption by 20.6% and water consumption by 8.3%.
Modern technology. Advanced manufacturing and the use of modern technology is necessary to enable the maintenance and fielding of these modern systems. To meet the needs of a 21st-century Army, we must use 21st-century technology. Through advanced manufacturing, AMC enhances the supply chain, establishing internal capabilities to rapidly respond to Soldiers’ and units’ equipment and repair parts requirements at the point of need. In 2018, AMC established an Advanced Manufacturing Center of Excellence at the Rock Island Arsenal Joint Manufacturing and Technology Center. The center came online in May 2019 and currently includes 25 3D printers and equipment. More than 2,000 parts have been printed to date, including much-needed personal protective equipment and medical repair parts to help the whole-of-government response to combat COVID-19. AMC brings these capabilities closer to the point of need via a digital thread database that links parts available for 3D printing into our Army business systems, including the Logistics Modernization Program and Global Combat Support System-Army. We are also rapidly 3D scanning parts and working with Army, industry, and education partners to develop the digital twin of a UH-60L at Wichita State University.
Data-driven decisions. Logistics data provides the decision support tools and the data visualization Army decision-makers need to effectively support readiness and modernization initiatives. Data allows us to see ourselves across the OIB to help streamline processes, increase productivity and maximize our support to warfighters while minimizing costs. We will leverage robotics, maintenance analytics, and predictive sensors on equipment, and continuous process management to increase production capability and improve quality throughout the OIB. Artificial intelligence and machine learning will help anticipate demands for new systems and build flexibility to meet new requirements and those for legacy systems. While utilizing processes like shop floor digitization allows us to better see our equipment usage and help us know when machines need to be serviced. To do this, we ask ourselves, are we looking at the right metrics and do we understand what the data means, working with data scientists and data analysts to make predictive and informed decisions.
The Army is also modernizing and streamlining sustainment business processes to increase the velocity and fidelity of decisions on the battlefield. Through Enterprise Business Systems Convergence, Enterprise Resource Planning system users will be able to ultimately use a single platform to access mission-critical data and analytics, enabling rapid delivery of effects on the battlefield and beyond.
People are Key
Our workforce is where the rubber meets the road; they provide the best equipment the world has ever seen, and it is their dedication that lets a warfighter know when they take a piece of equipment on the battlefield, it will survive enemy contact. In view of the challenges ahead, to retain readiness and drive modernization, we must focus on our people and empower our workforce. Simply put, we are in a war for talent, and we need the best people to work for the Army and AMC.
Trained and Ready Workforce. Along with our facilities and processes, the Army must modernize and improve the recruitment, development, and retention of its civilian workforce to maintain relevance and compete in the 21st century. We can accomplish this by leveraging new technology, modernizing talent management, and transforming workplace planning, enabling civilians to be more resilient and adaptive. Ready civilians are vital to the Army’s success as they fulfill critical needs across hundreds of occupations, side-by-side with uniformed service members to achieve a strategic advantage in a complex world. They make a difference by exercising their abilities, skills, and knowledge to create innovative solutions.
Artisan Workforce. Across the OIB, about 19,500 employees work in more than 240 different job fields, ranging from aircraft mechanics, machine tool operators, welders, and machinists. These artisans are the backbone of the OIB. To meet the Army’s future needs, we need to ensure we are hiring, developing, and retaining the next generation of artisans, and as with modernizing our infrastructure, we must identify and prioritize the jobs and skill sets needed to repair the Army’s future equipment. We have gaps in our internal knowledge, we must address those today to bring in the right subject matter experts to help inject those fine skills and training into our workforce.
Safety. Safety is a top priority for the industrial artisans and professionals in our OIB facilities, many of whom work on assembly lines, operate heavy machinery, or handle hazardous materials. This is especially the case in our ammunition OIB, which includes a workforce of more than 11,000 skilled artisans working at 16 plants, centers, and depots to produce, store, distribute, surveil, and demilitarize conventional ammunition for the joint force. The inherent risks in producing explosive materials can vary depending on the specific materials or the stage of the production process. For some of the highest-risk steps, the best way to protect people is to keep them at a safe distance. This is where engineering controls can be implemented. The power of engineering allows us to adapt our way out of potentially more severe incidents during energetics manufacturing and create a safer environment for our operators. For example, the new and modernized nitrocellulose facility at the Radford Army Ammunition Plant uses this approach to provide safer conditions for the operators, increased precision, and a more environmentally-friendly operation. Operators are now further away from the operation in this modernized facility, and they can now sit behind a control screen where they can manage and supervise the process in real-time. Our envisioned end state is state-of-the-art manufacturing processes and machinery with built-in safety standards across the industrial base.
Conclusion
We are at an inflection point and must accelerate our modernization plans for the OIB—facilities, processes, and people—to meet the needs of a 21st-century MDO-capable Army. While these facilities are successfully meeting our current requirements, we must continue to invest in modernization to drive change and ensure our ability to meet future requirements in competition, crisis, and conflict. Investing in the future force relies on timely, adequate, predictable, and sustainable funding in every budget cycle, in concert with a focused plan, to build the irreversible momentum needed to achieve persistent modernization. As the Army transforms, AMC and the sustainment community will be ready to support our warfighters now and in the future.
--------------------
Ms. Lisha Adams currently serves as the executive deputy to the commanding general of AMC. She has earned her Bachelor of Arts degree in economics from Birmingham-Southern College and received her Master of Business Administration degree from the Florida Institute of Technology.
--------------------
This article was published in the July-Sept 2021 issue of Army Sustainment.
RELATED LINKS
The Current issue of Army Sustainment in pdf format
Current Army Sustainment Online Articles
Social Sharing