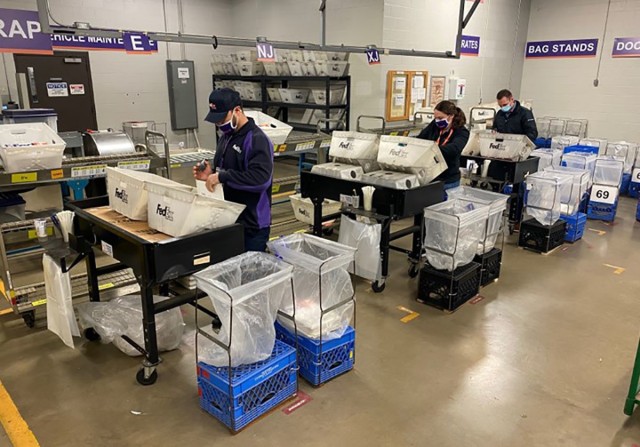
FORT LEE, Va. – A thriving Training With Industry program here is improving the Army’s ability to provide logistical support by leveraging modern civilian business best practices.
The Combined Arms Support Command is orchestrating TWI opportunities for each of its sustainment branches – Quartermaster, Ordnance, Transportation, Finance and Comptroller, Adjutant General – and overall logistics. Lt. Col. John D. Mitchel, logistics branch proponency chief, said there are 37 programs in all.
Capt. Claire Betterbed, a TWI participant working with Federal Express, attested to TWI’s unparalleled value. “It comes from full immersion into different real-time logistics challenges that participants view through a lens and perspective we do not traditionally experience in the operational Army,” she said.
“(I have been) working alongside industry experts to understand FedEx’s approach toward in-transit visibility, automated technology, disaster response efforts, partnerships with DOD, and optimizing transportation assets across the network. (These) are skills I think will translate well into addressing similar challenges across the Army.”
While each sustainment branch runs their own programs, the CASCOM Logistics Branch Proponent staff members are “the integrators and the consolidators of information,” said Sergeant Major James Yuras, senior enlisted leader of the group.
The Army realized years ago that it had gaps in competencies that industry could help fill, Mitchel elaborated. The TWI Program was initiated in the 1970s in response to the critical need for officers with state-of-the-art skills that were being demonstrated within private industry across the U.S.
During and immediately after World War II, the Army was the premier organization in terms of worldwide logistics, having moved supplies through two theaters of war, Mitchel further observed. That expertise gradually left the Army for the civilian world over the years. Bill Bowerman is one example. The former 10th Mountain Division Soldier used things he learned in Europe during World War II to become one of the founders of the Nike Company.
So, TWI helps in recapturing that expertise for the Army, Michel summarized.
Soldiers involved in the TWI program work with a civilian company for a year, during which they learn best practices that could be integrated into Army logistics. “Once they complete the assignment with that industry, we bring them back into a utilization tour for two years,” Mitchel said.
Some TWI participants return as instructors to help share their knowledge, and others – such as those who worked at FedEx – are assigned to key positions in the Army’s Military Surface Deployment and Distribution Command to maximize the return on investment in the operational domain.
“SDDC does a lot of our global distribution operations,” Mitchel noted.
Ordnance branch Soldiers have engaged in TWI opportunities with Caterpillar and Oshkosh, Yuras said. The Army uses engines made by those companies, so sending senior noncommissioned officers and warrant officers who repair and maintain the Army’s vehicles to the manufacturer gives them even more expertise along with an outside perspective.
In a similar way, Quartermaster Soldiers involved in fuel distribution have a TWI opportunity with Chevron Corporation, and Logistics branch Soldiers have an opportunity with FedEx, Yuras said.
“TWI at FedEx provides unlimited opportunities to learn directly from senior executives across the company to better understand how they formulate and implement their strategy, how they develop their teams and how they are constantly adapting to overcome tomorrow’s challenges today,” Betterbed elaborated.
“These days, FedEx has been responding to an unprecedented eCommerce boom and is playing a pivotal role in vaccine distributions, so it has been an incredible time to be fully integrated in an industry-leading logistics company.”
The staff at CASCOM and branch leaders don’t control what TWI participants do on a day-to-day basis. Instead, they use quarterly reports to refine their training objectives and guide the work to ensure it’s beneficial for the Army, Mitchel said.
“As a fast-paced company rooted in a people-first mentality and showing a true commitment to organizational values, there are far more similarities than differences between working with FedEx and for the Army,” Betterbed further observed. “While working at FedEx, I’ve been able to more fully appreciate industry’s ability to effectively leverage the most innovative technology and pivot quickly in response to unanticipated challenges.”
The programs are evaluated every year to determine if they are still bringing in new insights that are beneficial for the Army. If not, program administrators can move the next TWI participant to a different opportunity.
CASCOM and the individual program managers also review where there may be new opportunities to provide fresh perspectives for military planners and logisticians. They then have to determine what rank best suits the TWI opportunity. Some may work better for officers and others for NCOs or warrant officers.
“What’s the big Army problem we are trying to fix?” Mitchel asked rhetorically. “That’s one of the questions we are trying to answer.”
Looking into the future, CASCOM is endeavoring to develop a TWI program that will align with efforts to modernize the Army’s enterprise business systems, according to Yuras. That initiative is being shaped by guidance from Maj. Gen. Rodney D. Fogg, the organization’s commanding general.
“We’re looking at a few different industries who are on the leading edge of that,” he said, “and leveraging their knowledge as we transition to that new business system.”
Social Sharing