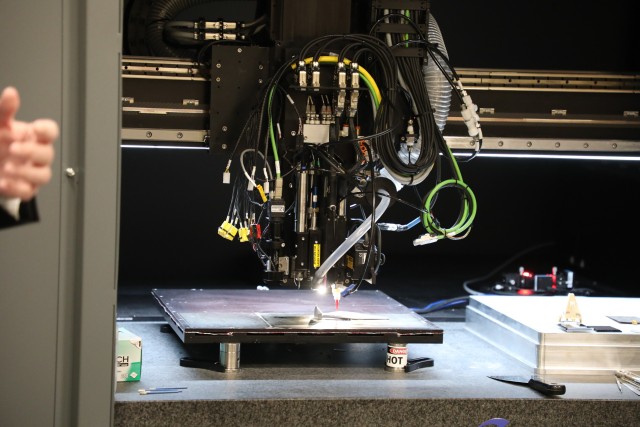
REDSTONE ARSENAL, Ala. – It’s a question Lance Hall asks of his U.S. Army Combat Capabilities Development Command Aviation & Missile Center customers, “What do you want your part to do?”
The answer he proposes is made possible by the AvMC Additive Manufacturing Facility.
When AvMC opened the doors on the facility in 2020, it was more than just a new physical space – it was a new way to serve the Warfighter. Additive manufacturing is a type of advanced manufacturing that can be used in all areas of a product life cycle from concept development to design, prototyping, production and sustainment. Whether it’s a rotorcraft part that’s not scheduled for an industry production line for another two years or it’s printed conductive materials on the inside of a missile case, additive manufacturing and AvMC ensure the Army is ready to fight tonight.
“Additive is more of a mindset than a specific technology,” said Hall, AvMC additive manufacturing technical lead. “It’s going about thinking about your problem in a different way, that you’re not constrained to the traditional methods of making a part. We can do new designs that work better – they go further, they fly faster, they deliver more punch when they get there, they’re lighter weight but still perform a mission just like the traditional method.”
The center-wide asset not only enhances AvMC’s science and technology core competencies, but also supports modernization priorities established by the Army Futures Command. The facility’s equipment includes the DMG Mori Lasertec 4300 3D, the 3DSystems ProX DMP 320, Stratasys Fortus 450MC, Object 350 Connex3 and the nScrypt 3Dn-1000. In-house capabilities now include material jetting, the ability to print conductive traces on the inside of tubular structures, laser powder bed technology and blown-powder deposition inside of a traditional multi-axis turning/milling center.
“Having an additive manufacturing facility and capability at the center provides AvMC yet another tool with which to deliver life cycle engineering solutions to our customers and ultimately the Warfighter, both from a readiness and a modernization perspective,” said Kathy Olson, AvMC additive manufacturing lead.

There is currently an ongoing effort to support the U.S. Army Aviation and Missile Command and the Army Materiel Command in identifying and qualifying readiness driver parts via additive manufacturing, a process AvMC can now conduct in-house thanks to the new facility. Other applications range from wind tunnel models to rocket nozzles and missile airframe bulkheads, whatever is needed to support the Warfighter.
“A lot of the benefit that we see is there are a lot of missile structures that are very complicated to build and they’re made out of very expensive materials,” said Matt Smith, division chief for composite materials and missile structures at AvMC. “Additive manufacturing allows us a more flexible fabrication method to build some of these structures to save weight, to save cost – especially with some of the high cost materials – and gives us a better design flexibility.”
AvMC’s mission is to deliver collaborative and innovative aviation and missile capabilities for responsive and cost-effective research, development and life cycle engineering solutions. The Additive Manufacturing facility highlights the center’s commitment to two of its priorities – readiness and modernization.
“From a readiness perspective, we can use additive manufacturing to prototype much faster and less expensively than traditional manufacturing, including design, test and iterate,” Olson said. “Additive provides the capability to quickly produce concept models, molds for composite layup, tooling, fixtures and jigs. Through reverse engineering, we can seek solutions to obsolescence, hard to source or long lead time issues.
“From a modernization perspective, we will be able to create and test parts that have been optimized for weight, frequency, and strength using a generative design process that most often results in a very organic design that cannot be traditionally manufactured. We can also explore through design and prototyping the consolidation of multiple parts into a single part to eliminate failure modes caused by joining processes. In the past we have been limited in design by what we could traditionally manufacture; AM isn’t bound by the same manufacturing constraints. It is cliché to say, ‘If you can imagine it, you can print it.’ But – that’s almost true.”
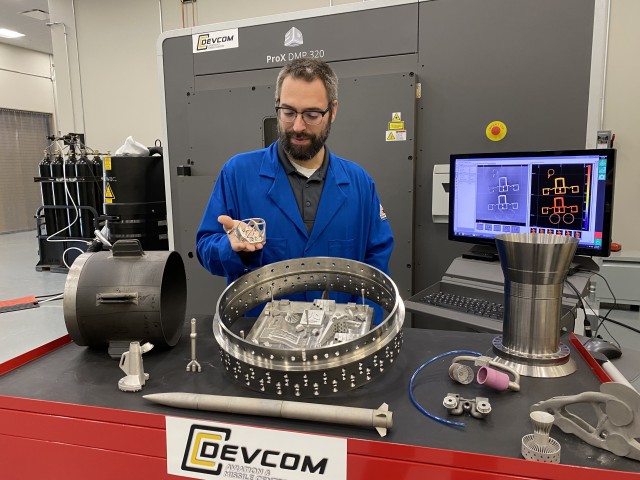
--
The CCDC Aviation & Missile Center, formerly known as the Aviation & Missile Research, Development and Engineering Center (AMRDEC), is part of the U.S. Army Combat Capabilities Development Command, which conducts responsive research, development and life cycle engineering to deliver the aviation and missile capabilities the Army depends on to ensure victory on the battlefield today and tomorrow. Through collaboration across the command's core technical competencies, CCDC leads in the discovery, development and delivery of the technology-based capabilities required to make Soldiers more lethal to win our nation's wars and come home safely. CCDC is a major subordinate command of the U.S. Army Futures Command.
Related Links
STAND-TO!: U.S. Army Modernization Strategy
Social Sharing