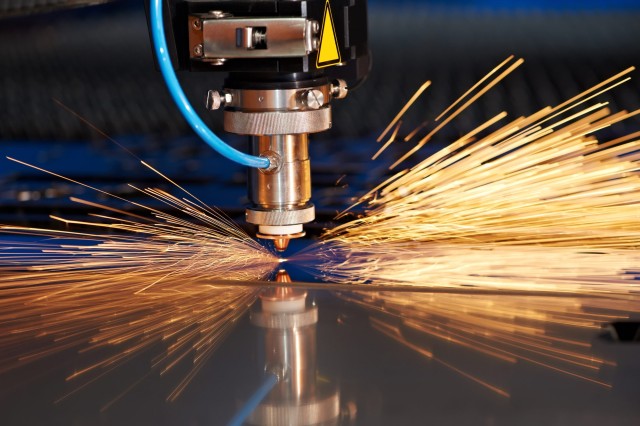
ABERDEEN PROVING GROUND, Md. -- For centuries, the standard recipe for metals development has been to take useful metals and add a small amount of other elements to enhance performance. Today, materials scientists are seeking a new approach to deliver a materials-by-design concept.
The Army identified materials-by-design in its Army Modernization Strategy as a priority research area to enable protection overmatch against future threats. Overmatch simply means being stronger, better armed, or more skillful than an opposing force.
Researchers at the U.S. Army Combat Capabilities Development Command’s Army Research Laboratory and partners at the University of North Texas sought to perform foundational research on whether material properties manifest themselves differently in high-entropy alloys because of their unique elemental combination. High-entropy alloys are formed by mixing equal or relatively large proportions of usually five or more elements.
“The overall goal of this work was to develop a framework that correlates changes in material processing with dominant deformation mechanisms and their impact on ballistic performance,” said Dr. Phillip Jannotti, a research scientist at the lab.
In a study published in Advanced Engineering Material March 30, 2020, the team said results may advance ballistic science to develop solutions that the U.S. Army needs by enabling optimally-designed materials that are tailored for a particular application.
“A key difference during alloy discovery and traditional ballistic characterization is that it is extremely expensive to fabricate new alloys, so every shot is precious,” said Dr. Jeffrey Lloyd, a research scientist with the lab and a program manager for metals research with Materials in Extreme Dynamic Environments. “We are pushing the limits of the amount of information you can extract during this key phase to identify candidate alloys and behavior for new ballistic applications.”
Lloyd said the partnership with the University of North Texas is an example of how the laboratory leverages a university’s expertise -- in this case classical metallurgy and characterization -- and uses it to help develop, explore and understand new materials for ballistic applications.
This congressionally-funded research looked at the link between metals processing and ballistic response. Ballistic impact, unlike traditional mechanical testing, subjects materials to extreme loading conditions.
Jannotti, co-author Dr. Brian Schuster and their colleagues have developed state-of-the-art experimental techniques to observe ballistic events, Lloyd said.
“At UNT, Drs. Mukherjee, Mishra, Banerjee and their students have world-class facilities and expertise for materials characterization and fabrication,” Lloyd said. “We put these tools to the test to see how much information we can extract from a single ballistic event.”

In a figure from the study, Lloyd pointed out the range of microstructures that form during a ballistic impact event.
“Microstructures are the fingerprints of how the material responds,” he said. “This is like CSI for ballistics. We got this all from a single test.”
The figure shows that researchers can perform hardness maps, electron back scattering diffraction and traditional scanning electron microscopy at different scales to dive into why the material stopped the projectile.
“The goal was to understand the role of processing on the deformation behavior and how this behavior compares with our conventional state-of-the-art knowledge of ballistic penetration,” Lloyd said. “This information is crucial for developing metal alloys with enhanced mechanical and ballistic performance whether for lethality or protection.”
The research program evaluated seven high entropy alloys. The scientific knowledge developed in this work combined expertise across the fields of material science, high-strain-rate failure mechanics and terminal ballistics, Lloyd said.
“Most importantly, we have developed a process that once we get a plate, designed by advanced computational methods and testing, we can perform full ballistic and microstructure characterization in less than two weeks,” Lloyd said. “We are working to get this down even faster. We want the rate-limiting step to be fabrication, not testing.”
Unlike traditional metal alloys and steels, high-entropy alloys or HEAs, and the associated science are relatively new.
“This, combined with the broad research trade space offered by high-entropy alloys, means that the opportunity to discover something novel is very high,” Jannotti said.
Researchers said the University of North Texas-ARL collaboration on HEAs performed foundational research on whether material properties manifest themselves differently in unique elemental combinations over conventional alloying. The collaboration, Lloyd said, was thanks to a cooperative partnership the laboratory created -- ARL South -- part of the lab’s Open Campus program, which is an initiative to build a science and technology ecosystem that encourages groundbreaking advances in basic and applied research areas relevant to the Army.
The bottom line, researchers said, was that experimentation found the behavior of these alloys can offer unique combinations of properties.
“It is important to note that we have only examined the equivalent of one piece of sand on an entire beach, so there are near limitless possibilities to explore,” Jannotti said. “In this program we are also developing atomic methods to rapidly evaluate potential candidate materials, as well as high throughput manufacturing and testing methods to explore properties.”
CCDC Army Research Laboratory is an element of the U.S. Army Combat Capabilities Development Command. As the Army’s corporate research laboratory, ARL discovers, innovates and transitions science and technology to ensure dominant strategic land power. Through collaboration across the command’s core technical competencies, CCDC leads in the discovery, development and delivery of the technology-based capabilities required to make Soldiers more lethal to win our nation’s wars and come home safely. CCDC is a major subordinate command of the U.S. Army Futures Command.
Social Sharing