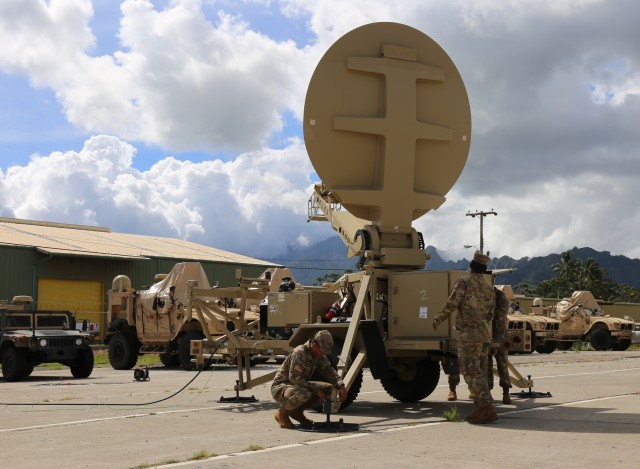
Imagine you are an active duty satellite communications systems operator/maintainer or multichannel transmission systems operator-maintainer, stationed in Yongsan, South Korea. Your system is the Satellite Transportable Terminal, or STT, the main satellite system for the entire Army Tactical Network. You are responsible for creating a means of communication for your entire brigade because the STT establishes secure voice, video and data communications virtually anytime and anywhere. Suddenly -- BOOM! -- The satellite crashes. The antenna won't tether to the satellite dish. You check to see if dust has gotten into the Joint Network Node or the Battalion Command Post Node because you know they operate in conjunction with the STT. Still, there is no connection. You try a couple of system reboots and get nothing. You feel a rush of panic because you know system repairs can take several weeks, maybe even months. Reluctantly, you report the news to your logistics assistance representative.
"Don't sweat it," you're told. "We'll get this satellite repaired in no time."
Fortuitously, a new repair concept called Depot Maintenance Forward is in place. DMF is a process in which depot-capability is placed in forward-locations to increase readiness for the warfighter. The concept was created for units stationed in high-activity locations such as Korea and Germany to leverage repair without evacuating systems to distant facilities. The U.S. Army Communications-Electronics Command and Tobyhanna Army Depot introduced DMF in support of the Sustainable Readiness Model, in which reducing turnaround time -- the repair cycle combined with shipping -- is a top priority.
Shannon Kaminski, an integrated logistics support manager for the Warfighter Information Network-Tactical, Increment 1 branch of ILSC Command, Control, Communications -- Tactical directorate, assisted with the rollout of the DMF process.
"We were involved in the very beginning looking at 'Is this even possible? Going to locations to see what capability even exists in terms of maintenance facilities. Can they paint? Can they do sand blasts? What kind of repairs can they do on vehicles or trailers?'" Kaminski said. "It was a joint effort with CECOM and TYAD that we ultimately landed as well as using already existing capabilities. So, in Germany that would be the Maintenance Activity Kaiserslautern (MAK) and in Korea it would be Maintenance Support Command Korea.
"What we did was verify that there was a capability that we could leverage. The next step was identifying units. To do that, we had to get buy-in from [U.S. Army Europe] USAREUR Germany and [United States Army Pacific] USARPAC Korea saying we need help prioritizing units and finding out what units need maintenance on their systems first. Then, we worked disposition instructions to get systems into maintenance and then get them back into the units. So, my role is basically the paperwork [part of] all of that and just making sure the paperwork is there and to ensure that anything they need forward, they have a point of contact to reach back to."
A fairly new process, the DMF concept inducted STTs as its pilot system in late 2018. Various levels of repair can be made depending on the system. Its two primary areas of repair include industrial repairs -- sanding down equipment to bare metal, cleaning, retouching, and repainting -- and electronic capability repair -- the ability to disassemble equipment and adjust the Line Replaceable Units. For the STT scenario stated previously, an electronic capability would be the best option. Jeffrey Roberson, regional maintenance manager for CECOM Far East (Korea), coordinates DMF hands-on.
"Depot Maintenance Forward provides a hot repair capability which services systems long overdue for above field-level maintenance," Roberson said. "While DMF targets WIN-T and command post systems, it really puts depot expertise in a place that impacts Soldiers."
Unlike previous repair processes, DMF frequently reports readiness and doesn't allow for extended periods of reset. To fulfill the drive for readiness, CECOM has had to adjust the way maintenance activity is coordinated by moving from a maintenance transaction to a supply transaction. Meaning, in maintenance, the unit reports weapon systems and the Soldiers get that same system back. In supply, the depot sends the Soldier's systems into repair and if they're a high priority unit, they can receive a float so there is zero downtime.
"As soon as they induct a system, we can give them another one that was actually working so there's no impact to their mission, which in turn, helps us incentivize units to get more inductions on the way," said Cesar Saenz, Inc. 1 branch chief. "But obviously, Tobyhanna Army Depot did a great thing; they did the bulk of the effort by trying to get the capability out there by negotiating with all these different vendors and organizations who are actually turning the wrenches on the equipment."
With a 14 hour time difference in Korea and a six hour difference in Germany, Saenz relies on communication from stakeholders such as Kaminski and Roberson. The team continues to support the DMF mission in hopes that its capabilities will expand.
"To be honest with you, there were a lot of obstacles and so many contributions from so many different people," Saenz said. "I would tell you that just hearing numerous times from the Army community of how CECOM and our team went out there on site and actually understood some of the challenges that folks were facing really made a difference. My team was indispensable in getting the equipment out when it was needed."
Social Sharing