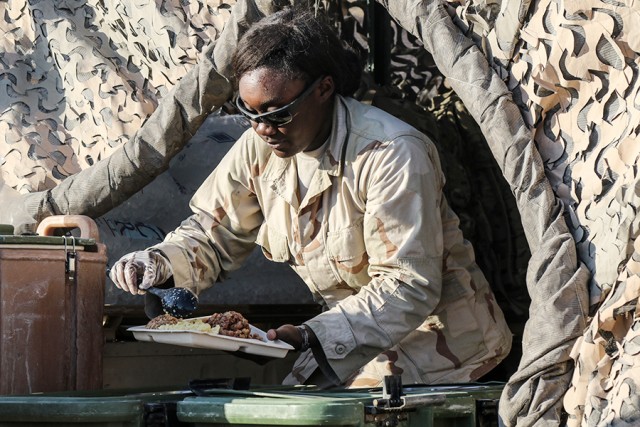
The 1st Stryker Brigade Combat Team (SBCT), 4th Infantry Division, Reconnaissance and Security (R&S) Excursion at the National Training Center (NTC) in 2017 was a monumental event in many ways. While the sole purpose of every other NTC rotation is to validate a unit's level of training and preparedness prior to deployment, this rotation served as a proof of concept for the task organization of an R&S brigade.
Traditional SBCTs are designed to fight with the firepower of armor brigades and with the speed of light infantry brigades. The R&S concept takes that up a notch. The purpose of an R&S brigade is to fight for information. As the first Title 10 forces that will be deployed into an immature theater of operations, R&S brigades must fight to understand the threat and literally decide what information is worth dying for. The vast majority of tactics, techniques, and procedures found in Field Manual 3-98, Reconnaissance and Security Operations, (the R&S bible) are based on previously existing cavalry doctrine.
The 1st SBCT created rotational task forces to satisfy the R&S requirement for greater depth of forces and longer lines of communications. This meant augmenting the SBCT with a wide variety of enabler units not currently found in its modified table of organization and equipment (MTOE). These enabler units included a unit from a cavalry squadron to provide direct control of rotary-wing assets, a second field artillery unit, and an M1A1 tank company.
While the typical SBCT's MTOE includes around 4,400 Soldiers, the package deployed to NTC approached 5,700 Soldiers. It was the largest and most complex fighting force ever to train at NTC. The rotation was observed by the Maneuver Center of Excellence to determine the appropriate force structure of R&S brigades for future deployments. It was a record-breaking event, but the important part is this: How does a distribution company go about supporting such a fast moving behemoth?
SHAKING UP THE MTOE
By MTOE, the typical distribution company in the brigade support battalion consists of a supply support activity (SSA) platoon, a fuel and water platoon, and a transportation platoon. For this rotation, A Company decided to try something new to facilitate the altered mission set of the R&S brigade. Rather than having two separate platoons of distinct capabilities, the company diverged from the typical MTOE structure and realigned the fuel and water and transportation platoons into two composite distribution platoons of like capability.
This transition took place about nine months prior to the NTC rotation to allow time for the teams to train together in their new configurations. After the realignment, each distribution platoon contained an equal mix of motor transport operators, petroleum supply specialists, and water treatment specialists and a complementing mixed fleet of M1120 load-handling systems (LHSs), M978 heavy expanded mobility tactical truck fuelers, and M105 compatible water tank racks. One platoon was designated as the brigade support area (BSA) platoon, and the other was dubbed the forward logistics element (FLE) platoon.
This distribution platoon concept also allowed for "plug and play" rotational task force augmentation, which in this case was the addition of a logistics task force platoon from the 68th Combat Sustainment Support Battalion. A contingent from a 59th Quartermaster Company platoon trained with A Company as a third distribution platoon of varied strength and capabilities during each of the brigade-level home station exercises leading up to the rotation.
For the NTC rotation, the final package from the 59th Quartermaster Company platoon consisted of a platoon leader and 19 of his Soldiers with four M1151 gun trucks and licenses on the M1120 LHS platforms operated by the organic distribution platoons. While the personnel--to-equipment ratio did not seem to match, in the end it proved invaluable to have more operators than vehicles as some of the organic LHS operators redeployed to Fort Carson, Colorado, early to attend mandatory schools and conduct permanent change of station. If those extra drivers had not been available, moving all of the company vehicles to the BSA at the same time would have been impossible.
HOW IT WAS BUILT TO WORK
While the two platoons were crafted to look relatively the same, their mission sets did vary. The BSA platoon was to manage supply point distribution and logistics resupply points (LRPs) and transfer requested classes of supply to forward support companies (FSCs) either from the BSA or at predetermined checkpoints, depending on the FSCs' geographic proximity to the BSA at any given time during the fight.
The FLE platoon, on the other hand, was to relocate closer to the forward line of troops, provide supply point distribution to FSCs, act as an ambulance exchange point, and serve as a potential new location for the BSA when it was time for the BSB to relocate. This was all contingent on the ever changing conditions of brigade's fight in time and space.
HOW IT ACTUALLY WORKED
Because of the way the fight progressed, the FLE was never called upon to deploy as expected. Instead, both distribution platoons conducted daily LRPs in support of multiple battalions while simultaneously transferring commodities to customer units on the BSA. While the LRPs were deployed, the A Company Soldiers who were not providing perimeter security or serving on various details were busy issuing fuel and water to FSCs that were still close enough to pull from the BSA.
For the first few days of the exercise, with three, four, or five battalions all pulling commodities at the same time, it created a scene akin to the New York Stock Exchange in the middle of the Mojave Desert. Green suits sped about at full tilt, jostling for position and demanding to know which water tanks were theirs and who from A Company was supposed to be trans-loading their fuel.
It only took about two mornings of this chaos to adjust. From that point forward, instead of each platoon keeping track of which interchangeable fuel and water tanks were theirs, one distribution platoon was given the responsibility to manage all BSA bulk water assets and the other was in charge of the fuel assets. This simplistic approach yielded an immediate payoff in the form of decreased customer wait times and improved visibility of on-hand bulk fuel and water quantities.
MANNING MULTIPLE LRPS
Although this was not how A Company was originally designed to operate for the R&S Excursion, the platoon leaders still found the overall mission to be easier to execute as they led mirrored distribution platoons instead of transportation only and fuel and water only.
With multiple LRPs being conducted simultaneously, but located up to 37 miles apart, it was easier from a mission command perspective for each platoon to be capable of providing supply classes I (subsistence), III (petroleum, oils, and lubricants), V (ammunition), and IX (repair parts) themselves without having to coordinate with their sister platoons for operators and equipment.
Secondly, the commodities most requested to sustain the warfighters during record high temperatures in the Mojave Desert in July were ice, water, fuel, and ammunition. At any given LRP, a distribution platoon could plan to bring each day a minimum of a container of ice, 2,000 gallons of water, and 2,500 gallons of fuel to each battalion. The platoon also had to consistently bring 10,000 gallons of fuel for the battalion with the attached tank company.
The composite platoons were properly outfitted to handle these requests without having to coordinate for additional operators or assets between platoons. This was possible because in the weeks and months leading up to this NTC rotation, A Company cross-trained its Soldiers on all of the tasks that the platoons would carry out during the rotation. The composite distribution platoon model helped the company create well-rounded platoons capable of accomplishing a wider mission set with the same number of Soldiers. The results during this proof of concept were undeniable.
A DAY IN THE LIFE OF AN LRP
Effective LRPs allowed the 1st SBCT to extend its operational reach during all phases of the exercise at NTC. The brigade support operations (SPO) section used the logistics status reports sent by each battalion daily to determine future logistics requirements and provide A Company with mission details 24 to 48 hours in advance. Despite best laid plans, the constant flux of battlefield conditions often shrank actual preparation timelines considerably.
In one such scenario, the FLE platoon launched into troop leading procedures to deliver several supply classes. The platoon leader issued the warning order to the platoon and made a plan to prepare equipment and loads. The logistics package consisted of multiple types of vehicles. The platoon leader and platoon sergeant decided the best way to attack the task was to arrange the trucks and loads into chalks, with each chalk containing the package for a different battalion.
While preparation commenced smoothly at first, the enemy always has a vote. In this case, the enemies were the work/rest cycle and the synchronization of logistics battlefield effects. The four containers of ice were not delivered to the BSA until midnight, and the repair parts for two battalions were not prepped or ready to be loaded onto the trucks.
Adapting to the challenge and not accepting anything less than 100 percent of supplies delivered to the customers on time, the platoon leaders took a divide and conquer approach. He allowed the drivers to sleep a few hours while the truck commanders prepared loads and staged vehicles through the night and into the early morning.
In order to maintain synchronization of logistics across the battlefield, the link-up time for all LRPs was at 8 a.m. daily. After prepping through the night and conducting a convoy briefing, battle drill rehearsals, pre-combat inspections, and a safety briefing focusing heavily on real-world fatigue, the convoy arrived safely at the designated location at 7:55 a.m.
The Soldiers established security by emplacing the three M1151 gun trucks in a triangular formation around the vulnerable commodities. As the distribution platoons from each of the four FSCs arrived simultaneously, the FLE platoon directed them toward their respective resupply packages and began the exchange. By 9:25 a.m., all FSC elements had departed the LRP location with their respective packages.
The lessons learned from this scenario are that prearranging the supply packages by battalions and segregating the supply packages from each other by battalion in different chalks works very well and that for long-term operations, FSCs need to adjust the number of personnel at the BSA. While the Soldiers of the mighty distribution platoons would not accept mission failure as an option, the ratio of work to rest between missions, taskings, and configuring loads for missions was not sustainable over the duration of a combat deployment.
Each FSC embedded within the SPO an average of two liaison officers at the BSA to communicate requirements between their forward elements and the BSA. Even an additional five personnel per FSC to help prepare loads for their battalions' resupply would have been a boon to A Company.
SUSTAINING COMBAT POWER
Just as feeding, fueling, and arming the largest and widest spread force in NTC history is not an easy feat, neither is the upkeep of its maintenance readiness through the SSA. The SSA's Soldiers were split across three geographic locations for the rotation. Four Soldiers were placed in the Fort Carson SSA to manage consistent deliveries from the logistics readiness center while the brigade was deployed. Those four Soldiers received and processed an average of 16 pallets per day, five days a week, for the month while the brigade was deployed.
The second location was the SSA at Fort Irwin, California, where seven Soldiers received and packaged repair parts for shipment either by ground to the BSA or, in the case of critical parts, by air directly to the customers. The final location was of course the BSA, where the remaining 16 SSA Soldiers received and processed parts for delivery to the FSCs.
The key to providing critical repair parts for such a massive and widespread brigade was the use of aviation assets to deliver directly from the SSA at the logistics support area at Fort Irwin. By the end of the rotation, more cargo was delivered by air than during any rotation dating back at least 14 rotations.
The other key to success was the strategic emplacement of repair part expediters at the rear SSA at Fort Irwin. These expediters were liaison officers who could tell the SSA staff which parts absolutely had to be transported to the front lines as quickly as possible. With their aid, the SSA Soldiers were given the clear understanding and sense of purpose required to get the most important parts to where they needed to go in the least amount of time.
All said and done, the R&S Excursion was a fast-paced, self-critiquing learning experience for A Company. There were plenty of mistakes made that were felt throughout the brigade. But it was the most effective way to learn how to support the R&S mission.
Most NTC rotations are fought from east to west or west to east, but the more difficult ones are fought south to north in order to spread forces wide. The 1st SBCT fought from north to south and then back north again. This had never been done before in NTC history. In the first 48 hours, the R&S excursion forces covered more land than is traditionally covered in an entire two-week training rotation.
Over the course of 12 days of training, A Company distributed 362,475 gallons of fuel, 323,800 gallons of water, 30 racks of repair parts, and 850,000 rounds of ammunition with a combined net explosive weight in excess of 150,000 pounds and valued at more than $5.3 million.
--------------------
Capt. Matthew R. Wellwood is an assistant professor of military science at the University of Wisconsin-Parkside, and a former commander of A Company, 4th BSB, 1st SBCT, 4th Infantry Division. He has a bachelor's degree in aeronautics from Liberty University. He is a graduate of the Combined Logistics Captains Career Course, the Mortuary Affairs Officer Course, the Quartermaster Basic Officer Leader Course, and the Sling Load Inspector Certification Course. He is a Demonstrated Senior Logistician in the International Society of Logistics.
--------------------
This article is an Army Sustainment magazine product.
Related Links:
Army Sustainment Magazine Archives
Social Sharing