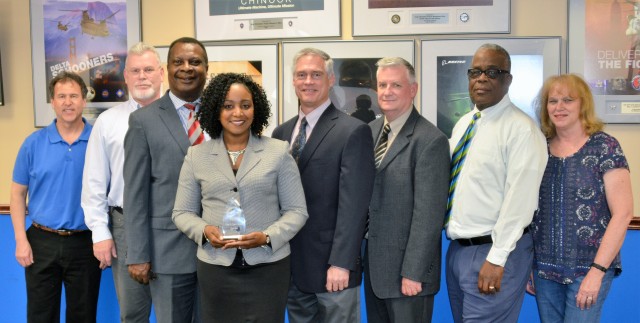
A Continuous Process Improvement project by a PEO Aviation team has been nominated for the Army's Lean Six Sigma Process Improvement Project Team Excellence Award for their efforts in eliminating or reducing the duplication of work for provisioning requests within the Cargo Helicopter Project Office.
The Cargo Helicopter Project Office is responsible for the Army's worldwide CH-47 fleet. Provisioning is the process of determining and acquiring spares and repair parts, and support and test equipment required to operate and maintain an end item of material.
The provisioning team manages taskers for the office and in the span of two fiscal years, the team experienced over 50 percent turnover in manpower due to attrition and promotions.
The workload demand continued to increase. Work requests that were submitted were unable to be assigned or tracked due to requests being sent in a variety of ways, such as in person, by email or through phone calls, resulting in duplicated work requests for their team.
A CPI project was established to identify inefficiencies and come up with possible solutions. CPI is a Department of Defense endorsed method for becoming more efficient and effective in operations. It involves strategically identifying areas for improvement, measuring current performance, performing root cause analysis, generating possible solutions, pilot testing and institutionalizing new improved processes.
"The Cargo Provisioning CPI team found the root cause was a non-standardized process without necessary process controls," Robin Miller, CH-47 provisioning team leader, said. "The business impact was a reduction in the available work time and reduction in workforce capacity."
A workflow web application was developed requiring unique single-entry request for tasker assignments. Other management features included a searchable database to track assignments, team workloads and an on-time delivery performance.
"The project has enabled the provisioning department to maintain previously fully-staffed workload levels without having to add additional staffing resulting in a cost avoidance," Miller said.
Project benefits include transparent management of all provisioning requests, elimination of rework and duplications, increased resource capacity, quantitative resource workload management and improved on-time delivery.
Winners of the PIPTEA will be announced later this year at the annual Lean Six Sigma Excellence Awards program in Washington.
Social Sharing