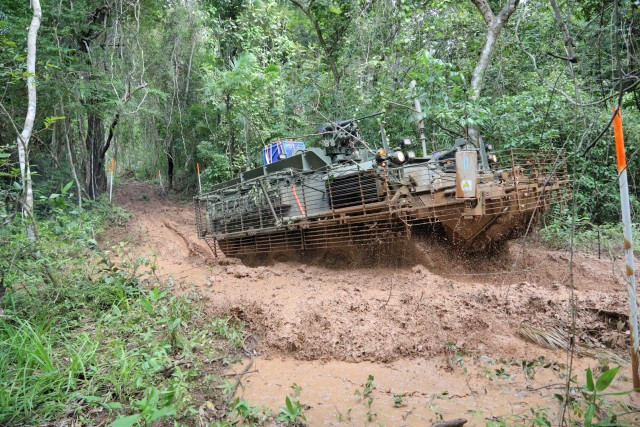
When Soldiers in Iraq and Afghanistan were threatened by the destructive power of improvised explosive devices, a variant of the armored Stryker combat vehicle sporting a specially-designed blast-diffusing hull saved countless lives.
The vehicle's stellar performance is doubtless related to the extensive evaluation it had undergone at U.S. Army Yuma Proving Ground (YPG) and its three subsidiary test centers since 2002, including a six month stint in the jungles of Suriname in 2008.
Recently, the vehicle underwent a punishing mobility test conducted by U.S. Army Tropic Regions Test Center (TRTC) in Panama, the first test of its kind conducted by the United States in the Central American nation in decades. This evaluation followed a significant amount of durability testing at Yuma Proving Ground facilities in Yuma, Arizona and Fort Greely, Alaska over the previous year.
Boasting an upgraded chassis and drivetrain along with a variety of mechanical, electrical and digital improvements to enhance performance, the latest Stryker variant was driven more than 2,000 miles across rugged terrain by the time testing concluded at the end of the tropical rainy season in December.
"If a young Soldier is ambushed while driving a combat vehicle in a dense jungle, his reaction will be to immediately extricate himself from that situation," said Ernest Hugh, TRTC director. "The question is, is this feasible under those conditions? What are the vehicle's capabilities and limitations in an extreme tropical environment?"
With tropic regions comprising nearly 40% of the world's land surface and serving as home to more than half the world's population, ensuring military equipment works as it should in this extreme environment is crucial, and Panama is an ideal locale to conduct this testing.
Drenched by well over 100 inches of rain per year, the consequences of a tropical environment can be disastrous to gear. Thick vines and vegetation can rip exterior components off passing vehicles, insects can eat through Kevlar, and high humidity and salinity in the air can rapidly corrode even stainless steels. Vehicles face their own special challenges: mud and other jungle biomass can degrade performance, if not stop a vehicle in its tracks.
Having successfully conducted tests of the Stryker and Mine Resistant Ambush Protected vehicle in the nation of Suriname in recent years, TRTC testers were excited to gain permission to test the latest upgrades to the Stryker in Panama, a global transportation hub where personnel and equipment can arrive faster.
"We have a better range of different types of roads here, and logistically you save a good two or three days of shipping this way," said Julio Zambrano, test officer. "Testing here means fewer stops in-between for materials and personnel."
These advantages were helpful to the test, but there was still a great deal of preparation necessary.
"We setup everything from zero here," said Carlos Mora, civil engineer. "In Suriname we had something predefined, but here took a lot more surveying work."
Personnel came from Yuma Test Center to assist in this painstaking process, and worked to define and characterize vehicle trails as other workers were remodeling a dilapidated 5,000 square foot building to serve as an office and vehicle maintenance bay. As the visiting personnel were returning to Yuma, there was concern that a relatively tame El Nino rainy season was in the offing. However, these predictions did not come to pass.
"The difference between the dry and rainy season is night and day," said Omar Silva, test officer. "When I returned after being here in the dry season, I couldn't believe it; I couldn't recognize it. The soil gets so soft and the vehicle is so heavy."
Extremely rugged in the best circumstances, the profile of the facility's roads changed as the rains flooded and washed out trails more and more with each passing day.
"We had to reclassify certain secondary dirt roads as cross-country all the way," said Zambrano.
Nonetheless, the testers got exactly what they hoped for: an unforgiving tropical rainy season on a punishing jungle road course.
"We expected the vehicle to get stuck," said Silva. "We made sure we came up with a good methodology to progressively try to get the vehicle unstuck. That way, you can characterize the performance of the vehicle."
When the vehicle got bogged down by slick, gripping mud that was formerly a road, testers first attempted to extricate it with a single-line pull utilizing the vehicle's built-in recovery winch. Failing that, they attempted to pull it out with engine assist and a double-line before resorting to a bulldozer.
"We do a lot of data collection when it happens," said Silva. "We try to characterize the terrain, how the vehicle ended up, and the angles of the winch line. We also take soil samples and check the moisture of the soil and other characteristics of its composition."
The testers also took a measurement of the slope of the vehicle with sophisticated instrumentation, as well as the longitudinal and lateral grade of the stretch of road, and made comparisons of how the terrain originally looked with the conditions in which it got stuck.
"We measure the distance from the vehicle to the trees the winch was attached to, and how far away it was from the tractor, if that was necessary to retrieve the vehicle from the muddy spot," said Mora.
"It's a lot of work, but I think we collected good data that can be used later in field manuals," added Silva.
Throughout the test, TRTC's highly skilled, multi-functional staff was augmented by personnel who normally work at Yuma Test Center.
"We have the ability to flex folks from Yuma Test Center when a large test comes here," said Col. Randy Murray, YPG commander. "It keeps costs down and provides the benefit of sending engineers who have worked on the same system in Yuma."
"We are a team and all help each other out, which makes things go a lot smoother" added Paul Wilson, heavy mobile equipment mechanic. "It's been a good experience."
All involved agree that natural environment testing is a critically important component to ensuring Soldiers' equipment works as it is supposed to in the unforgiving crucible of ground combat.
"It's one thing to see reports and photos, and another thing to be on the vehicle driving through the mud, trees, and thick vegetation," said Murray. "It's definitely different from the other two environments we tested it in at YPG. Being at all three test centers gives us a better understanding of what the system is capable of, and that is important information for the warfighter to have."
Social Sharing