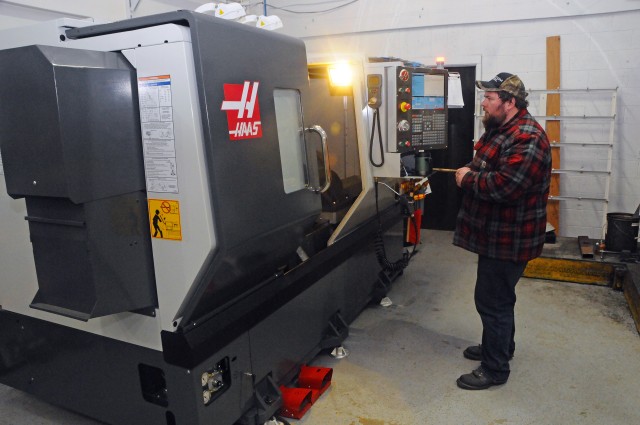
COLD REGIONS TEST CENTER, Alaska-- It is vital that all military equipment work wherever in the world American Soldiers need it, and treacherous extreme cold is something American troops have had to contend with more than once.
U.S. Army Cold Regions Test Center (CRTC) is the Army's center for testing systems in extreme cold, and the active support of the test center's Allied Trade shop is crucial to carrying out this important mission.
Fabricating everything from replacement parts for items under test to specialized fixtures and adaptors necessary for test infrastructure, Allied Trade machinists work each day to make the items testers count on.
Until recently, these parts were machined on manually-operated mill and lathes. As the equipment aged, it slowly lost precision, for which CRTC's machinists had to compensate. Now, the shop is using a new Computer Numerical Control (CNC) machine that is significantly more advanced.
"We've been trying to replace the previous unit, which was about a 1992 vintage, for the past five years," said Kyle Anderson, test support division chief. "The bearings were worn out and it was very difficult to find suitable replacement parts. We wanted to replace it with something contemporary and able to do more complex machine work."
The most labor intensive portion of fabricating a part with a CNC is designing it in a computer aided design program and setting up the machine with the appropriate tools. Once the design is loaded and the machine is cutting the part out of a piece of blank material, the machine is capable of producing far more complex components than manual machines.
"We're already machining parts today that we could not do in the past," said Sam Porter, machinist. "It's been awesome to see."
Located near Delta Junction, Alaska, CRTC exists to conduct punishing testing on a wide variety of military equipment, from vehicles to artillery. The nature of the work makes part failure inevitable, and downtime can be expensive, even when caused by failures of relatively simple parts.
"There's not necessarily a parallel between the complexity of a part you build and the impact it has on testing," said Porter. "Anything that shuts down testing is significant, no matter how small or simple. The primary focus is always keeping a test operational, especially tests with a massive amount of personnel support: downtime for them can run in the thousands of dollars per hour."
In the interior Alaskan winter, the prime time for testing, weather and road conditions can make expedited shipping of a replacement part difficult, if not impossible.
"'Overnight' shipping is a three to five day adventure, with all things being perfect," said Richard Reiser, test officer. "Overnighting something may within two days put it in Fairbanks, and then we may or may not be able to drive there to pick it up, depending on the size of the item and road conditions. In winter, we don't have a lot of daylight, the large animals come out, and roads become an issue with slippery ice and snow for continuous periods of time."
Meanwhile, waiting days or weeks for a part to arrive could mean that testers will miss the coldest days that they covet for their missions: this past winter was relatively warm, which meant testers had to be even more flexible than usual to be ready when temperatures dipped.
"We have to be able to take advantage of the weather as it happens," said Anderson. "That requires a quick turnaround, which is definitely incompatible with long lead times for parts. We simply have to be able to make them."
As they design items in the CAD program, CRTC machinists save the designs for parts as they go, which makes re-fabrication a quick proposition. Further, a CRTC customer that already has CAD designs for their test item's relevant part can provide it to the machinists. Items that previously took days to fabricate on a manual machine can now be done in a matter of hours: if the design is already available as a CAD file, it can be done in minutes, all to the manufacturer's specifications.
The CNC machine also gives its users a significant safety dividend: the tools and spindle that automatically machine the part are located behind plexiglass doors that must be closed for the machine to operate.
"The enclosures do wonders for us from a safety standpoint," said Porter. "Not just for the operator, but for other people around the shop. There's really no way to get into this machine other than the front door, and it is set up to alarm immediately and shut down the spindle if the door is opened."
The shop is small, but CRTC test customers appreciate having all their needs capably and personally met by a single entity.
"It's not common that you get all of these capabilities in a small shop with only a few workers," said Porter. "You don't have to talk to a department head located in another state to get something designed and machined. The customers enjoy that about our support."
Social Sharing