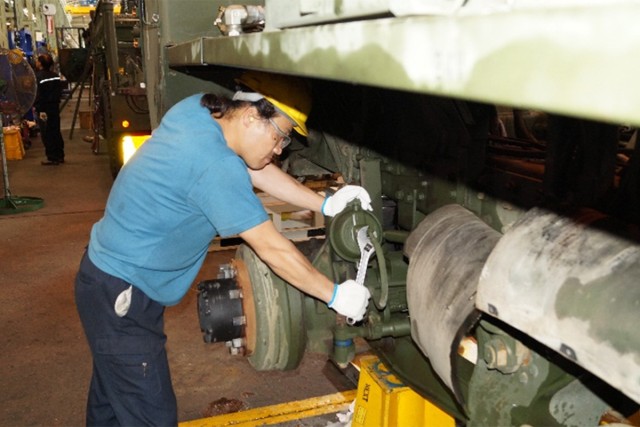
Shortly after a Military Sealift Command vessel was grounded off the coast of Okinawa, Japan, on Jan. 22, 2015, the Materiel Support Command-Korea (MSC-K) was notified that six humvees were inbound to the Port of Busan, Republic of Korea (ROK), for repair.
The vehicles and associated communication equipment, urgently needed for Exercise Cobra Gold in February, had been deeply submerged in sea-water during the accident and were badly damaged.
MSC-K marshaled both its tactical and Industrial Base resources to transport the equipment, remove its corrosion, repair it to 10/20 standard, paint it, and have it outbound for Thailand in time to participate in the exercise.
Although the extensive repairs required hundreds of parts and more than 1,350 man-hours of labor, the cost to the U.S. government was minimal thanks to low labor rates, extensive fabrication capabilities, and the close proximity of a Defense Logistics Agency Disposition Services facility. All of these assets were available to MSC-K because of its position at the sustainment hub of Korea.
HISTORY AND ORGANIZATION
On Sept. 15, 1964, several small logistics units in the rural farming community of Waegwan, ROK, were combined and designated as the U.S. Army Camp Carroll Depot. The depot's mission was to provide general support maintenance for the Eighth Army and store operational and reserve stocks.
More than 50 years later, this organization is now designated as the MSC-K and has transformed into a unit similar to a theater sustainment brigade. It has elements on almost every camp and base in Korea.
MSC-K's 25th Transportation Battalion coordinates the movement of all U.S. military personnel, equipment, supplies, mail, and other materials by air, rail, bus, and truck. Its 6th Ordnance Battalion stores, maintains, and issues all U.S. ammunition from ROK military ammunition supply points and ammunition depots. MSC-K's 498th Combat Sustainment Support Battalion provides area maintenance, supply, personnel, and finance support.
Members of the paramilitary Korean Service Corps (KSC) Battalion are embedded in dozens of units and perform missions varying from the after-hours transportation of M1 Abrams tanks to providing official translators for the Eighth Army commanding general. KSC personnel stock shelves in the commissary, operate forklifts, repair equipment, drive trucks, and perform hundreds of other important functions.
At the core of MSC-K lies the Industrial Base, operating in 19 facilities across Camp Carroll. It is co-located with the Defense Logistics Agency Distribution-Korea and the Army Field Support Battalion-Northeast Asia, which manages Army pre-positioned stocks stored in the Pacific.
The Industrial Base is organized into directorates and divisions and led by Department of the Army civilians and Korean national employees. The Directorate for Maintenance provides pass-back field-level-and-below depot sustainment support for U.S. Army, Navy, Air Force, and Marine Corps customers in Korea and Japan.
COST SAVINGS
MSC-K is able to keep its quality standards high and production costs low because the ROK assists with many of the costs associated with stationing U.S. forces overseas. Through a program known as Labor Cost Sharing, the ROK government contributes up to 75 percent of the cost of labor for Korean national employees. Because more than 90 percent of Industrial Base employees are Korean nationals, the U.S. government saves a significant amount of money.
Logistics Cost Sharing is another ROK-funded program that allows MSC-K to purchase supplies, tools, equipment, and services for its repair and production facilities. The only requirement is that the items must be purchased from a Korean vendor and, in most cases, be produced in Korea. By leveraging Logistics Cost Sharing, MSC-K has added capabilities, improved quality and safety, and increased efficiency at no cost to U.S. taxpayers.
In the last three years, MSC-K has received more than $18 million of Logistics Cost Sharing funds to purchase a 60-ton crane, a rail car mover, part washers, paint drying booths, ventilation systems, forklifts, and dozens of other items.
MAINTENANCE OPERATIONS
In one of the Directorate of Maintenance's largest facilities, Thomas Robertson and Chung Uk Yim walk along the bays of the Heavy Equipment Division to ensure that their workers receive the safety briefings that start their day. Since the ability to speak English is not a requirement for 90 percent of the workforce, every U.S. civilian is partnered with a bilingual senior Korean national.
Refurbishment is performed as part of the Theater Sustainment Repair Program. The program has been a unique part of operations in Korea for over 30 years and is a key reason that readiness rates, even for aging fleets, remain high. Wheeled and tracked vehicles, small arms, optics, radios, and all types of ground support equipment are eligible for refurbishment under the program every five years.
Mechanics use the "inspect and repair only as necessary" concept and only replace defective parts. At the end of the 90-day process, a refurbished truck will look and handle like new and all modification work orders, safety of use messages, and services will have been applied.
MSC-K is a qualified provider for the Army Materiel Command's National Maintenance Program. The directorate is also a source of repair for transmissions, radiators, wheel assemblies, and other repair parts. MSC-K has the lowest labor rate of the current 14 National Maintenance Program sources of repair. It is one of only two Army units to have ever been rated maturity level 5 (best in class) in three consecutive International Organization for Standardization 9001 quality audits.
Under theater sustainment repair and return, or pass-back maintenance, units send in their most difficult problems and worst wrecks. Pass-back maintenance constitutes the largest portion of the Directorate for Maintenance workload.
Units also ask MSC-K to fabricate specialized parts that are not available through the supply system. MSC-K has wood, metal, hose, and cable fabrication capabilities. Last year it started repairing hydraulic cylinders and fire suppression bottles to address specific maintenance concerns from its customers.
TRANSPORTATION OPERATIONS
MSC-K's Supply and Transportation Directorate (S&T) plays another critical role in Industrial Base operations. Its missions include the receipt, classification, storage, and worldwide distribution of various classes of supplies.
Units directed to retrograde class VII (major end items) equipment outside of Korea can turn it in to MSC-K. S&T will then work directly with MSC-K's Directorate of Maintenance to bring the equipment up to the standard required by disposition instructions.
S&T inventories and orders missing items and instruction manuals and professionally cleans, packages, and prepares equipment for shipment. S&Ts ability to efficiently and safely process and distribute heavy equipment through the retrograde process speaks highly of the level of expertise in the workforce and dedication to keeping the defense supply chain moving and the warfighter sustained.
STORAGE OPERATIONS
On the southeastern coast of Korea, the Busan Storage Center performs logistics operations such as the receipt, quality control, and care of supplies in storage, including rations, lumber, packaged lubricants, and war reserve operational project stocks.
One of the center's critical missions is agriculture inspections. The Busan Storage Center has U.S. Department of Agriculture-certified personnel to perform inspections of equipment being retrograded to the continental United States. This provides cost savings to units by keeping them from having to send personnel on temporary duty to perform this task.
From its humble beginnings in the 1960s as the U.S. Army Camp Carroll Depot, MSC-K has grown to become an integral part of logistics for all military services stationed in Korea. MSC-K is a truly unique organization that provides a quality product and saves the Army money through cost-sharing programs.
The organization's motto of "Two Nations--One Team" reflects MSC-K's tight integration of its local-national workforce and its commitment to providing logistics support throughout the Korean theater.
_____________________________________________________________________________________________________
Scott E. Fowler is the deputy director for maintenance at the Materiel Support Command-Korea. He holds a bachelor's degree in business management from the University of Maryland and an MBA from Central Michigan University. He is a graduate of the Army Civilian Education System Intermediate Course and is certified in Life Cycle Logistics Level III from the Defense Acquisition University.
Austin W. Anderson is a supervisor quality assurance specialist serving as the director for quality management at the Materiel Support Command-Korea. He is a retired chief warrant officer five and holds an MBA from the University of Phoenix. He is Level III certified in both Production Quality Manufacturing and Life Cycle Logistics, is a member of the Acquisition Corps, and is a Certified Lean Six Sigma Black Belt.
_____________________________________________________________________________________________________
This article was published in the March-April 2016 issue of Army Sustainment magazine.
Related Links:
Discuss This Article in milSuite
Browse March-April 2016 Magazine
Army Sustainment Magazine Archives
Browse Army Sustainment Magazine
Social Sharing