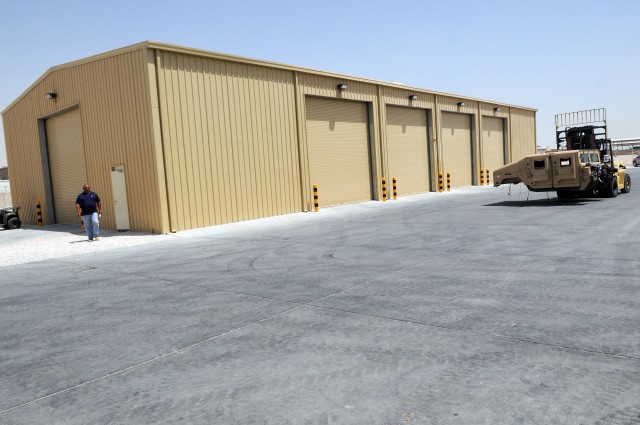
CAMP AS SAYLIYAH, Qatar (Apr. 17, 2008) Ac"a,! At a ceremony here today, the newest HMMWV maintenance facility in the Southwest Asia area of operations opened.
The facility provides the 1st Battalion, 401st Army Field Support Brigade maintainers doing HMMWV body repair work a permanent home.
Until now, when the maintenance team of Soldiers, Army civilians and contractors needed to work on battle-damaged or battle-worn HMMWV's here, the vehicles were taken into already cramped shop that was designed for other purposes. Space was at such a premium the vehicles had to be wedged into and worked on in any available area, frequently outdoors.
A Lean Six Sigma initiative implemented here in late 2006 helped solve the problem. The brigade and Army Sustainment Command staffs were instrumental in obtaining the necessary funding for the project, and the Area Support Group - Qatar Directorate of Public Works, provided their expertise.
Built at a total cost of $652,000, the new 6,000-sqare-foot Auto Body Repair Facility can handle as many as 16 vehicles at any given time in a climate-controlled environment.
The insulated building is equipped with four oversized, roll-up bay doors; is fully air-conditioned with bright industrial shop lighting; pneumatic air lines and heavy duty air compressor capability.
Another key feature is the ventilation system which will safely exhaust fumes created during metal cutting and welding activities.
"This facility takes our workers out of the heat, wind and dust and gives them a tailored place to work on these vehicles," said Lt. Col. Maxine Girard, 1st Battalion commander. "This should increase our capacity and throughput back to the warfighter."
According to Girard, the facility won't just increase production, but is a real morale booster.
"They (the HMMWV repair team) don't have to fight for space, and now have a place they can call their own."
The problem, and solution, highlight one of the successes of the Army's recent push at business process improvement through the LSS program, according to Lewis Strickland, maintenance manager for ITT Corp., which is under contract to perform the repair work.
As the battalion's mission expanded to meet the growing repair demands resulting from combat in Iraq, the need for more and improved shop space became increasingly apparent, Strickland said.
"A Lean Six Sigma project team made up of folks from ITT and the battalion determined that to obtain the needed enhanced throughput, a new facility would have to be built," said Strickland. "They wanted to be sure we were able accomplish the mission of getting these vehicles fixed and back where they belong - in the hands of the warfighter."
At the facility opening ceremony Col. Dennis M. Thompson, 401st Army Field Support Brigade commander, echoed those sentiments.
"In the past you had to make do and move into other, much needed space. That is not the desired solution," said Thompson.
"At the end of the day, this facility will increase maneuverability and capability in the battlespace," said Thompson. "This is another arrow in the battalion's quiver, and thousands of miles up the road, your work translates into better capability for the warfighter."
"The building is ready, but a bit more needs to be done," said Strickland. "All the needed repair and safety equipment must be brought in. Once that is accomplished in the next few days, the first vehicle should be brought in and the real work can begin."
Social Sharing