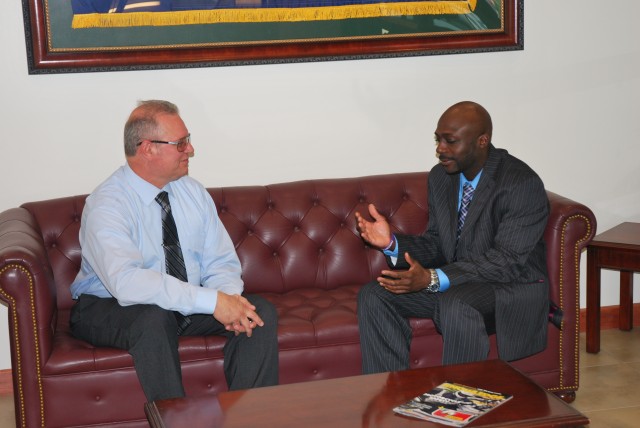
Military Surface Deployment and Distribution Command introduced continuous process improvement using the Lean Six Sigma methodology to command members in 2006. Since then, SDDC has realized cost avoidances of more than $25 million from LSS projects.
Two members in the command's Strategic Business Directorate used this training to improve their Transportation Discrepancy Report process and recouped nearly $14 million from ocean carriers associated with damaged or missing government cargo.
Demitrous Blount, chief, Cost and Billing Branch, and David Jones, lead traffic management specialist, are on a mission to ensure SDDC gets the exact transportation services it contracts for with ocean carriers on behalf of Department of Defense organizations. If commercial carriers are negligent or the service of the contract is not met as expected, their message is simple -- no payment!
According to the U.S. Transportation Command's Universal Services Contract, or USC, the government pays ocean carriers upon lift for all transportation services ordered on government cargo. The USC provides international cargo transportation and distribution services on an end-to-end basis contracted through ocean carriers to manage the process. The contract allows the government to request reimbursement of transportation services that are not performed as ordered, yet have already been paid.
From February 2009 to February 2010, Blount, along with Jones and 12 other team members from SDDC, U.S. Transportation Command and commercial industry, started their first LSS project -- Improve OCONUS (outside continental United States) Transportation Discrepancy Report Process.
"Prior to 2009, we had a process in place to recoup monies for damaged or destroyed cargo from carriers," Blount said, "but we didn't have timelines or standards to notify carriers to respond back to our requests for payments. With this project, we established a more efficient notification process and schedule within the branch to gain acknowledgment within 30 days from carriers on damaged or missing items."
According to Blount, prior to this LSS project it was standard procedure to submit Request for Payment letters to a carrier when the cargo was damaged or lost. But the unknown variable at the time was if the carrier would or would not respond to the letters. The project helped them set appropriate timelines for response and if not met, an automatic claim through USTRANSCOM's Acquisition office would be initiated. In this case, the office packaged up a multitude of claims that were sitting out there with no response from carriers and did a global settlement with one of the carriers contributing immensely to the recovery of about $14 million.
The results from this project also caught the attention of Department of Army leaders resulting in the team winning one of two Army Lean Six Sigma Project Team Excellence Awards in 2010.
Blount and Jones took their new calling to the next level with a second LSS project called Improving Recovery of Unearned Transportation Charges, which they exercised from December 2011 to April 2012.
This project focused on identification of transportation charges that were associated with destroyed or missing government items while being shipped by commercial carriers.
Within the first 120 days of improving this process, the team recovered $685,000 in transportation costs associated with destroyed or missing government cargo that was in the care of commercial carriers. SDDC expects recovery of $2.3 million per year of unearned transportation charges as a result of improving the recovery of unearned transportation charges process.
"In many instances, if the carriers knew they had damage to report, they didn't charge us up front," Jones said. "Our goal was to identify a process to determine which shipments carriers did not earn the transportation charges for. Then we had to expand upon that to recover the charges."
Blount and Jones will be involved in a third project starting later this year -- Recovery of Prorated Unearned Transportation Charges from Ocean Carriers.
"This project will allow us to look at prorated charges based upon damage percentages to cargo or partial pilferage," Jones said. "The goal is to come up with a solid formula or standard that we can recover at least part of the transportation cost associated with partially damaged or missing cargo.
"These projects are in line with solidifying a process to identify the charges and know which shipments carriers did not earn the transportation charges," Jones added. "Then expand on that to recover the charges."
Jones also mentioned they are creating a process to take recouped money from carriers and return it back to the source (military units who own the equipment) instead of turning it over to the U.S. Department of the Treasury.
About Lean Six Sigma
For LSS to be successful, the command has a full-time program director overseeing all LSS training and activities.
"My mission is to teach and lead SDDC members in the Continuous Process Improvement Program using Lean Six Sigma methodology," said Jim Coe, Lean Six Sigma Deployment Director for SDDC. "Our intent is to yield improved delivery of capability and sustainment to the Warfighter."
"To me, the biggest thing I learned from working LSS projects is no matter what you do, you work it collectively with various stakeholders," Blount added. "Everyone talks their piece that they know and it really opens up the lines of communication."
"LSS is a great tool and makes my work process better," Jones said. "It has given me more work, but it also gives me more job satisfaction because I know I can actually get out and get things done. Also, the nice thing is, the lines of communication that are opened through LSS always remain open."
LSS is a fact-based, data driven process improvement method used to remove waste and variation in a process while reducing cost and improving quality.
Between September 2006 and July 2012, nearly 300 SDDC military and civilian employees completed various types of LSS training and performed 69 LSS projects with 46 percent of the projects completed at brigade level and below. SDDC has realized a cost avoidance of $25.3 million during this timeframe.
LSS training includes a project sponsor, green belt, black belt, and master black belt. Project sponsor training equips employees to lead an LSS project in cooperation with a green belt or black belt. Green belt and black belt training provides the knowledge and skills needed to apply the LSS methodology to process improvement. Black belt training is much more in depth so employees can handle complex problems with multifunctional project teams. Master Black Belt training prepares employees to be senior subject matter experts coaching project teams and teaching LSS classes.
SDDC's primary focus is timely and accurate support to the Warfighter and the command leverages services from the best of U.S. transportation industry to accomplish this important mission. The command provides expeditionary and sustained end-to-end deployment and distribution solutions for surface shipping of Department of Defense equipment and supplies to Warfighters worldwide.
Social Sharing