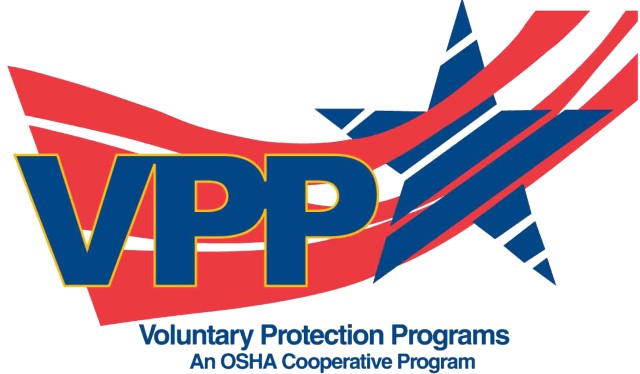
ROCK ISLAND ARSENAL, Ill. - A little before 6 a.m., Lu Gaeta, facility engineer, drives along Beck Avenue on Arsenal Island on his way to work. One morning about a month ago, car lights ahead caught him off guard.
"Someone was getting dropped off in front of the entrance to 299," he said. "The morning darkness and inadequate street lights really made it hard to me to see the car sitting there in the road. If I hadn't been paying close attention, I would have hit their tail end."
This incident came to mind later in the week when he was briefed during his department's safety meeting. Gaeta was able to discuss the problem and report it using the Voluntary Protection Program.
Voluntary Protection Program or better known as VPP is intended to improve safety in the workforce by implementing a safety program. This proactive model is management driven and employee owned, which works to reduce incident rates, increase production and provide satisfaction throughout the workforce.
"It's designed for employees to speak up and address concerns they notice in their work areas," Scott Berg from Rock Island Arsenal Joint Manufacturing and Technology Center's safety office, said. "It's having a proactive safety culture here at RIA-JMTC verse having a reactive approach."
In 2009, when VPP started at RIA-JMTC, they had a total case incident rate of 5.33 from the previous year. The current rate is 2.29, a 57 percent reduction.
"We have come a long way since our start in May 2009," Berg said. "It was a slow start, but I can really see improvement."
VPP comes from the Occupational Safety and Health Act (OSHA) of 1970, which details Congress's intent to have safe working conditions for all employees. It is not driven down from the top, but rather designed to empower everyone with the tools to succeed in a safe environment. Continuing to improve safety programs involves all levels of the organization.
With Col. James O. Fly, commander RIA-JMTC, fully engaged, the rollout for VPP is underway with a total of 243 items have been assigned to complete. Rock Island Arsenal has completed 214 of them, 24 are in progress and five have no action taken.
"Managers are creating an atmosphere for employees to take control of their environment," Travis Brokaw from the safety office, said. "I've seen a noticeable difference. People are going about it the right way and helping to create a culture that will benefit employees and make the program stick."
Brokaw went on to add he had gotten support from Greg Lupton, deputy director of product management and engineering. The planners needed to implement the Composite Risk Management (CRM) and were not all aware of the requirement. CRM is the process of identifying and communicating hazards by using worksheets and reporting methods.
"Greg agreed that it needed to be done and got his employees in line for VPP to integrate it with common practice," Brokaw said. "He wanted his guys to take ownership of safety practices."
The unions have jumped on board as well. Mary DeSmet, acting president of AFGE Local 15 on Rock Island Arsenal, said historically the unions have been the safety champions for the workers. They were the ones to assist in fixing the deadly working conditions and still continue today to be involved with all aspects of safety.
"We've gotten much safer than we were years ago," she said. "VPP will only enhance our ability to keep everyone as safe as possible. It was created to promote better cooperation between employees, management and the unions to assure the safest work environment we can have. VPP will not infringe on employee rights, in fact it will strengthen employee rights to make our workplace safer."
It's common for programs not to always have a smooth start. Lisa Roberts is a member of the VPP Steering Committee and said it's been challenging meeting with all of the employees.
"We haven't met with half of the workforce yet," she said. "People are hearing a lot about it from others but we'll need at least another year to really get the program going."
The Steering Committee is comprised of employees, management and union representatives who meet regularly to help craft the VPP awareness messages to the workforce. Committee members will rotate every two years.
Chris Brooks, machine repair, said they have reviewed VPP at their safety meetings. He said they review all the accidents and how they could have been prevented.
"My boss is good at going over safety," he said. "With machines especially, it's important that we use safety and communicate problems is a top priority. We do look at safety issues and try to handle them as needed."
Several employees have reported safety concerns using VPP. Some welders were concerned about how they could support armor plates while welding. They held a meeting to discover new ways to complete the work accurately and safely. It was determined the plates could be placed on top of metal frames to support the weight. Another project involved welding the Huskey bar from a horizontal position to a vertical position which provided a safer environment for the welder.
As for Gaeta's drives to work in the mornings, he says he's more cautious.
"I think my complaint with VPP was accepted and hopefully resolved in a matter that doesn't create another safety issue," he said. "I was told they are looking into it so that's good."
Social Sharing