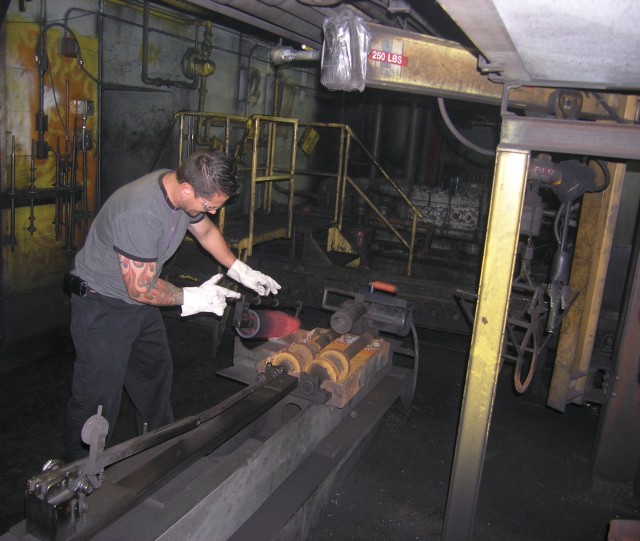
ROCK ISLAND ARSENAL, Ill. -- Scranton Army Ammunition Plant may now add another award to the mantle. Scranton AAP is the winner of the 2011 Secretary of the Army Environmental Award for Sustainability - Industrial Installation. Early 2012, the Army released the names of winners of the 2011 Army Environmental Awards for Installations, Activities, and Individuals.
The Secretary of the Army's Environmental Awards represent the highest honor in the field of environmental science and sustainability conferred by the Army. Scranton AAP is a first time recipient of this award and the only Joint Munitions Command installation to take the honor.
Particularly rewarding for Scranton, this award proves impressive for the government-owned, General Dynamics--Ordnance and Tactical Systems-operated plant of limited space. Situated on 15.3 acres in downtown Scranton, Pa., the government/contractor team must maximize the use of current infrastructure while incorporating low-impact development conforming with the established standards for historical buildings.
As a smaller production plant bordering a teeming industrial and residential area, there leaves very little greenspace.
Innovation is crucial when proposing and incorporating green technologies. No stranger to environmental standards and processes, Scranton is ISO 14001 certified in environmental management system. In 2010, Scranton boasted a first as the Department of Defense's first installation to commit to the Department of Energy's LEADER program. (The Save Energy Now LEADER program is a new component of the existing and successful Save Energy Now initiative through which companies partner with DOE to conduct energy audits and assessments designed to identify the opportunities for energy and cost savings in the companies' operations.)
The aim of the program requires participants to pledge to adopt a goal to reduce energy intensity to 25 percent over a 10 year time span.
In addition to the plant's committed effort, their operating contractor General Dynamics is ISO 14001 certified (2002) for production operations making them one of the first in the Army to do so.
Most importantly, the Scranton environmental plan is implemented daily 'through contractual oversight and involvement with the Production Based Support (PBS) Modernization efforts', according to Richard Hansen, commander's representative, SCAAP.
He continued, "Scranton Army Ammunition Plant, Joint Munitions Command, and General Dynamics collaborate on these modernization projects to ensure the government is getting best value and efficiency from all projects completed at Scranton Army Ammunition Plant."
But what specific environmental concerns does Scranton tackle best?
• water conservation & reuse
Nestled in an area receiving 40 inches of rainfall a year, Scranton officials used the prevalent resource to capture and reuse more than 2.5 million gallons of rainwater per year. Using three storage tanks of nearly 24,000-gallons, after collection and diversion of the rainwater, it is in turn used as cooling water for the plant's production. In April 2010 more than 3.1 million gallons of rainwater had been collected, counted and reused.
Scranton's water conservation effort is a most impressive feat with water consumption 37 percent less in Fiscal Year 2011 than Fiscal Year 2010, says Hansen.
• reduction of greenhouse gases & air quality improvement
Establishing an objective to reduce the volume of Volatile Organic Compounds, Scranton takes a closer look at coating operations of the large caliber ammunition products. Particularly of concern were VOC levels in indoor environments and air quality improvement as a result. A pollution prevention program is in use to identify technology controls, accordingly reducing the amount of paint and solvent required for coating. Following funding, training and improved efficiencies, GD-OTS supported conversion and installation of the three final paint lines. Those three lines are 100 percent compliant with emissions standards.
• material substitution & elimination
In an effort to reduce zinc-phosphate in its production process, Scranton is evaluating alternative replacement chemicals. Steel ammunition parts are treated prior to painting to improve corrosion resistance and paint adherence. The reduction effort was conceived in June 2011 in response to Scranton's selection in a pilot program studying the potential impacts of total maximum daily load of zinc (and future regulation of phosphate) in the Chesapeake Bay watershed.
• energy conservation
To cultivate sustainable modernization, Scranton is implementing three large scale improvement projects: modernization of a rotary hearth furnace, reduced consumption of a forge and boiler replacement. Those three projects aim to reduce natural gas consumption, lower electrical intensity and achieve greenhouse gas reduction goals. In addition, Hansen notes an 18.4 percent decrease in gas and electricity consumption than in Fiscal Year 2010.
As a true leader, the Scranton AAP family shares its success throughout the JMC by way of tasker responses and periodical facility updates.
Scranton Army Ammunition Plant is a subordinate of the Joint Munitions Command (headquartered in Rock Island, Ill.) JMC operates a nationwide network of conventional ammunition manufacturing plants and storage depots, and provides on-site ammunition experts to U.S. combat units wherever they are stationed or deployed.
Social Sharing