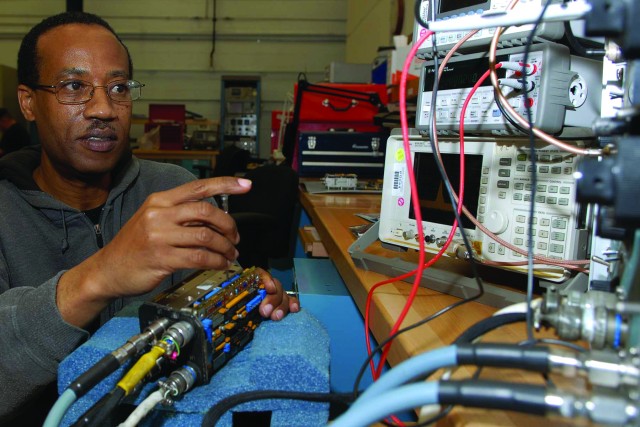
TOBYHANNA ARMY DEPOT, Pa. " Tobyhanna Army Depot has joined an elite group of public and government organizations that have earned certification in internationally recognized standards for quality.
Tobyhanna is the first military installation and third organization of any type in the world to achieve certification to Aerospace Standard (AS) 9100 Revision C and AS9110 Revision A, says Larry Bulanda, Quality Management Division (QMD) chief.
AS9100C, titled Quality Management System " Requirements for Aviation, Space and Defense Organizations, and AS9110A, titled Quality Management Systems " Requirements for Aviation Maintenance Organizations, were developed with input from aerospace personnel from the Americas, Asia/Pacific and Europe.
On July 6, the depot was notified by NSF, the depot’s AS registrar, that AS9100C and 9110A certification had been granted.
The AS9100/9110 certification signifies the depot’s commitment to meet or exceed increasingly stringent industry requirements as a world-class supplier of defense systems and related products to civil and military markets, according to QMD officials. The division is part of the Productivity Improvement and Innovation Directorate.
“Companies and other private and government public organizations here and abroad require AS certification before they will consider doing business with another organization,” Bulanda said.
The depot was audited by AS officials in July. Rimas Bildusas, a senior quality assurance specialist in QMD, said the four auditors pointed out several strengths, including the depot’s experience and expertise in core products.
“They noted that our work force is very knowledgeable and skilled in many areas to accomplish customer requirements, and that depot personnel are committed to a professional work environment,” Bildusas said.
“Not only are the work areas organized and refined by Lean events and 6S audits, but continual improvement to enhance operations was evident from on-going upgrades.”
Although the auditors were impressed with depot personnel and operational efficiency, some improvements were made to earn certification.
“During the preparation period, there were a lot of questions on requirements and processes that did not have established answers; there were many mid-process changes as they became available,” said Paul Sumski, Multipurpose Cable fabrication Branch, Electronic Assembly Division, Systems Integration and Support Directorate. “Everyone worked hard to help achieve certification. Everyone became aware of all the potential good things that certification could bring, such as increased Avionics workload. The cost center benefited as a whole by improving efficiency and working together as a team.”
Bulanda said there are three standout accomplishments.
“Tool control is one. We worked with John Jastremsky and personnel in the Tool Crib Operations Branch to build hundreds of Process Tool Boxes that were placed in AS shops,” he explained. “This gives the technicians in those shops improved tool control, helping to eliminate potential foreign object damage (FOD) from loose tools.”
“I was temporary supervisor [of the Navigation Branch] at the time of audit,” said Chester Schultz, Avionics Division, Command Control and Computer Systems/Avionics Directorate. “We were fortunate to be in the Depot Maintenance of the Future facility and already started to implement most of the 9110 practices. We increased the number of personnel entering data into the LMP (Logistics Modernization Program) data base, including parts used and work done. And we increased awareness to FOD and ESD [electrostatic discharge].
“The branch now has more control over parts, and awareness to counterfeit parts. I couldn’t be more proud of how the employees handled the audit, and the cooperation with getting prepared. They displayed a positive attitude towards the future of the depot.”
Another important accomplishment was the development of the FOD program. FOD is basically loose equipment or other objects that may damage equipment if not stored or disposed of correctly. QMD personnel in conjunction with Information Management personnel developed a voice-over slide show and hands on training to identify and eliminate FOD problem areas. American Federation of Government Employees (AFGE) Local 1647 assisted with the implementation of depot regulation 702-23 Foreign Object Debris and Foreign Object Damage Prevention, Control, Awareness Program and Tool Control, which governs the program. And FOD posters were distributed around the depot to further raise awareness.
“We established standard tool boxes in our branch and technicians are paying more attention to FOD and prevention,” said Carol Kubilus, chief of the Satellite Systems Support Branch, Electronic Assembly Division, Systems Integration and Support Directorate. “All team members, both federal and contractor, came together as one team and worked side by side to meet or exceed all requirements set forth by AS9100/ 9110.”
The third standout is the development and implementation of the Qualified Task Listing (QTL), a document that meets the AS requirement to have a record of an employee’s qualifications to perform assigned tasks.
“The QTL is like a resume,” Bildusas said. “It is a record of an employee’s education, training, skills and experience. If a branch needs help, the supervisor can access QTLs to identify employees from other shops who are qualified in that branch’s mission. One important note is that QTLs are not used to rate performance, only what an employee is qualified in.”
Bulanda and Bildusas noted that there were several other achievements made by personnel and organizations across the depot.
“Obtaining AS certification is a big accomplishment by the total depot team,” said Brad Jones, director of Productivity Improvement and Innovation. “Almost every part of the depot had a hand in the success. It shows that the quality of work performed by the depot work force meets very rigorous industry expectations.”
“Now that we’ve earned certification, we can’t just put it on a shelf and pull it out whenever we want to impress customers; sustainment is very important,” Bildusas said. “We will continue to meet with shops personnel to maintain our certification, but the bulk of sustainment will be handed over to the shops. From now on, there will be regularly scheduled audits and AS officials publish a list of organizations that no longer maintain the high level of quality needed to stay certified.”
Tobyhanna Army Depot is the Defense Department’s largest center for the repair, overhaul and fabrication of a wide variety of electronics systems and components, from tactical field radios to the ground terminals for the defense satellite communications network. Tobyhanna’s missions support all branches of the Armed Forces. About 5,600 personnel are employed at Tobyhanna, which is located in the Pocono Mountains of northeastern Pennsylvania.
Tobyhanna is part of the U.S. Army CECOM Life Cycle Management Command. Headquartered at Aberdeen Proving Ground, Md., the command’s mission is to research, develop, acquire, field and sustain communications, command, control computer, intelligence, electronic warfare and sensors capabilities for the Armed Forces.
Social Sharing