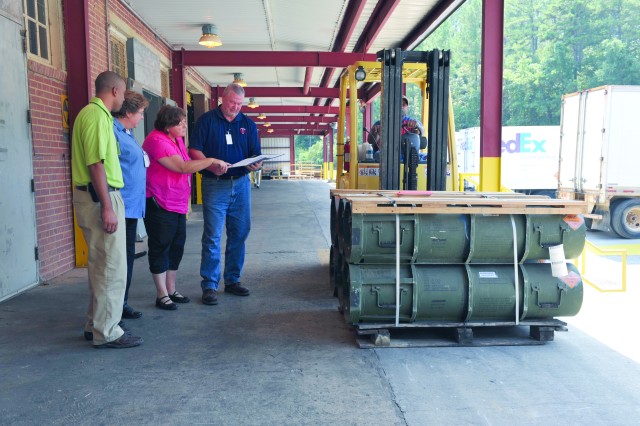
ANNISTON ARMY DEPOT, Ala. -- Whenever Anniston Defense Munitions Center gets a new commander, a team from Joint Munitions Command spends a week on site to provide the commander with an assessment of his programs.
Led by Jackie Skiles, command inspection program coordinator, the team consists of JMC personnel sent out to evaluate the core functions in their particular areas of expertise.
Whether safety, quality, security or travel, the headquarters personnel meet with their on-site counterparts to evaluate their duties and practices, and to share best practices from other installations. The team has a checklist of areas to examine, with Army regulations, command policy memoranda and other documents as their guides.
After the results are recorded, using a red, amber, green rating system, the commander is briefed on the results. While the commander receives daily updates, the final briefing is a roundup of all findings presented at once.
For the commander, "it's a starting point -- it's a baseline," said Skiles.
For Lt. Col. Randall DeLong, commander, Anniston Defense Munitions Center, the assessment team arrived early in his tour.
"We tell him where his vulnerabilities lie based against the established standard," Skiles said.
The benefit to the new commander is that he is given an idea of the strengths and weaknesses of his operation at the beginning of his tour, which lets him know which areas to work on. All JMC commanders sign an agreement with the JMC commanding general on their improvement areas. Since it's at the start of his tour, any findings are not negative marks against the commander.
And there are other benefits to the timing and style of this assessment adds Skiles. "The benefit of doing this when we do it is that if we identify a problem that is a result of a vague policy, funding, manpower or something like that, we can elevate that and possibly provide assistance."
The command inspection program evolved from a commander's complaint about disruption and duplication of inspections. The CIP resolved that issue by consolidating the inspection visits, so that one team visits for one week, rather than each staff section sending inspectors throughout the year. That fix was the beginning of the command inspection program 25 years ago.
"We started out very small. There was a test pilot at the former Newport Army Ammunition Plant in Indiana. It was the very first test site and they went out with about four or five people. They had some lessons learned and then they decided to go ahead and continue to evolve the program at the other ammunition plants," said Skiles.
For all of the evaluating and assessing, there really is one clear objective Skiles wants to make known. "The main thing I want people to understand is it's not adversarial in any way. We are not white glove inspectors that come down with the sole intent of finding discrepancies. We're not on a witch hunt."
Skiles pointed out that the inspection team is encouraged to find areas where the installation excels - best practices that other installations can emulate.
The status of Anniston Defense Munitions Center is strong, according to Skiles. "The desire to do a good job is as strong as it ever was."
Some team members were surprised by all that is going on at Anniston - getting headquarters subject matter experts out to the field to see how policies are being implemented and how some installation personnel are double and triple-hatted are important parts of the program.
According to Christie Webber, traffic management specialist, her role during the inspection is to make sure guidelines are not only in place, but in use. "Our strategy for evaluation is to ensure Department of Defense and Department of Transportation regulatory policy and processes are in place and being followed. We also ensure hazardous material training and certification is maintained and up-to-date."
Specifically, she evaluates transportation based on the Department of Defense / Department of Transportation regulatory requirements, DoD 4500.9-R Defense Transportation Regulation, and Title 49 Code of Federal Regulations. More specifically, she assesses shipping, receiving, commercial carrier performance and distribution of freight.
In addition to making sure processes are running smoothly, Webber gains a face-to-face with people previously accessible by e-mail or phone. The benefits extend beyond the inspection.
"I think it will help us communicate and build a strong working relationship," said Webber.
And today Skiles reflects on the overall status of the inspection program. "Since its inception, the program has been in a continual state of evolution. We are always trying to improve it and make it more user-friendly, more viable. We are open for any kind of suggestions or recommendations of improvement. That's always encouraged."
Anniston Defense Munitions Center's primary mission is receipt, storage, surveillance and shipment of missiles and conventional ammunition. It is also the site of the Department of Army's only Missile Recycling Center and is one of the Army's premium ammunition storage sites because it is capable of storing some of the Army's largest munitions.
Social Sharing