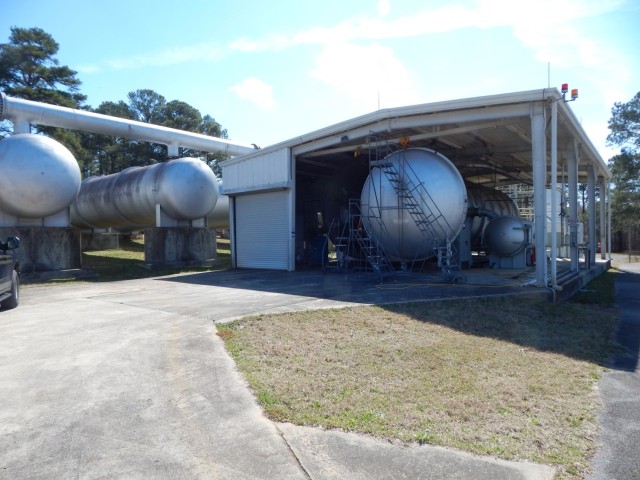
REDSTONE ARSENAL, Ala. (July 23, 2025) – The U.S. Army Redstone Test Center’s Propulsion Test Division has long served as the Army’s premier static test facility, boasting a rich history of evaluating propulsion systems within the Department of Defense. Located within RTC’s Missiles and Sensors Test Directorate, and with five test stands capable of accommodating solid, liquid, and hybrid rocket motors, the Propulsion Test Division specializes in static fire testing of systems generating up to 10,000,000 pound-force of thrust.
Recent developments at the High Altitude Test Chamber are no exception to the above statements. Utilizing three two-stage mechanical pumps for rapid evacuation of air, the chamber can simulate altitudes as high as 126,000 ft. at ascent and descent rates specified by the customer. Originally, this chamber was designed purely with MIL-STD-810 testing in mind:
- Rapid Decompression Testing: Rapid loss of cabin pressure to 40,000 ft.
- Storage/Air Transport: Low pressure testing of materials transported by air
- Leakage and Deformation Testing
Since ascent and descent rates can be throttled, the Propulsion Test Division can also meet specific customer altitude requirements outside of the bounds of MIL-810 testing to closely simulate the flight path an item would see in its operational environment. Additionally, the Propulsion Test Division can simulate temperature extremes (-40 °C to +60 °C) to take the altitude testing one step further by allowing for customers to test their item at a flight representative altitude and flight representative temperatures. This division has tested both the All-Up Rounds and at the component level for many Army, Navy, and Air Force systems.
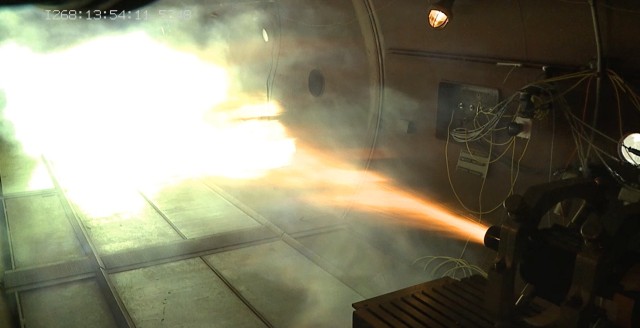
As valuable the above tests are for qualification testing, they do not encompass every Army test requirement, or the test requirements of the missile defense industry at large with regards to altitude testing. In general, both the United States, our allies, and our adversaries are purposing significant funding for Research & Development into hypersonic weaponry and defense, as well as modernization of current ICBM technology. The U.S. needs access to advanced, adaptable test facilities that can support the evaluation of hypersonic and interceptor weaponry to surpass the current capabilities of our adversaries.
RTC’s altitude chamber directly addresses this need. The facility has conducted multiple successful static firings for the Navy, The Missile Defense Agency (MDA), and numerous private industry customers in support of various Department of Defense (DoD) initiatives. Specifically, the Propulsion Test Division is primarily conducting altitude static firing of Divert and Attitude Control Systems (DACS) linked to multiple hypersonic and ICBM interception programs. A significant portion of these tests have been geared towards propellant characterization and technology maturation of extinguishable solid propellant. For items in flight, the DACS is responsible for making corrections to missile trajectory. These corrections need to be immediately available across all three axes (x, y, and z) to achieve the desired flight path. Extinguishable solid propellants DACS are demonstrating a reliable solution for rapid corrections to flight paths without the complexities inherent with liquid propellant operation and storage.
Recognizing an industry need for testing DAC systems at these high engagement altitudes, the division test team implemented a series of upgrades to the altitude chamber to allow for static firing within this controlled environment. Below is a list of some of the significant upgrades made to the altitude chamber to support static firing and improve data collection:
• Mechanical Pump Upgrades: As discussed further below, rapid evacuation of air and exhaust is essential for static firing as the introduction of exhaust affects data collection. Each of the 3 mechanical pumps at the altitude chamber have been upgraded with new, much larger models capable of removing more air at higher rates.
• Installation of Vertical Reaction Mass: Many customers require a vertical firing condition for their test item. The division installed a concrete reaction mass capable of withstanding 10,000 lbf. that does not interfere with use of the area for non-static firing tests.
• Sealed Camera Housings: Customers often want multiple high speed camera views to capture their item under test as a performance metric. At 10,000+ frames per second, high speed cameras in an environment with little to no air will quickly overheat. The division’s test team created custom sealed, nitrogen purged cameras capable of housing High Definition and High Speed cameras for test.
• Ambient Chamber Conditioning: Many of the test items static fired within the altitude chamber are early within the acquisition process and want to control as many variables as possible during testing. The Propulsion Test Division constructed a temporary conditioning wall that utilizes a dedicated HVAC unit to condition the altitude chamber to ambient temperatures. This wall also contains pass throughs for extreme conditioning of test items, if required.
• Data Collection Channel Count: The Propulsion Test Division significantly increased the channel count for static firing events within the chamber. Currently, the chamber has 120 K type thermocouple pass throughs, 20 T type thermocouple pass throughs, 21 accelerometer channels, 28 multi-use channels for strain, pressure, thrust, etc., 8 firing line pass throughs, and 6 ethernet pass throughs for cameras and test equipment.
While the above upgrades have significantly improved test capabilities within the chamber, none of these solve the overarching technical challenge that the chamber faces. Since the chamber contains no active or passive diffuser technology (discussed further below), the maximum propellant weight that can be fired in the chamber is a matter of pressure vs. volume. When a motor is static fired in a closed chamber (solid or liquid), the propellant mass is turned into high temperature, high pressure gas that rapidly expands upon exiting the motor nozzle. This gas acts as “air” and will increase the pressure reading of facility chamber pressure, thus lead to a decrease in altitude. The larger a test item is, the more significant of a loss in altitude.
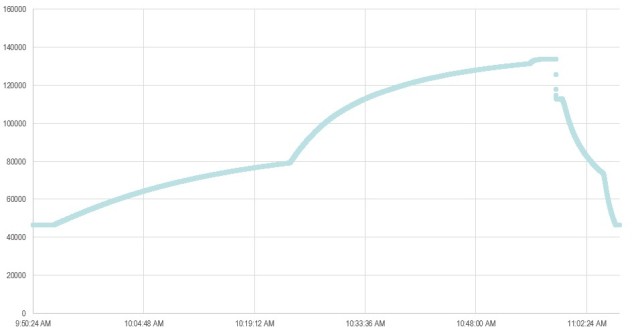
Above is an example of the facility chamber altitude readings of an item during test. At T+0, the starting altitude was around 133,000 ft, but at the completion of the firing the altitude decreased to 113,000 ft.
The Propulsion Test Division is actively pursuing solutions for the rapid evacuation of exhaust during tests. Most vacuum facilities in the country operating at simulated altitudes employ steam/air ejection technology, which leverages the venturi effect in fluid dynamics. A high-pressure motive fluid is fed through the primary motive nozzle (shown in the below picture), and through the divergent section of the diffuser. As the fluid flows through the primary nozzle and into the diffuser, the high pressure, low velocity gas turns to a high velocity, low pressure state. This process effectively reduces the pressure of the motive fluid to be lower than the pressure of the altitude chamber. By directing the rocket motor’s exhaust plume into the ejector inlet, the system can effectively remove the exhaust as quickly as it is being introduced.
The implementation of this technology will not only improve current capabilities and test results but will also allow the division to house much larger Net Explosive Weight (NEW) solid rocket motors and accommodate longer burn durations for liquid propellant motors. This technology has the potential to attract an entirely new customer base outside of DAC thrusters, solidifying the Propulsion Test Division’s position as one of the country’s premiere static test facilities, and further the country’s ability to develop and counter emerging missile technology.
The U.S. Army Redstone Test Center is located on Redstone Arsenal and is a subordinate command of the U.S. Army Test and Evaluation Command. RTC provides technical expertise, state-of-the-art facilities, and capabilities to plan, conduct, analyze, and report the results of tests on missile and aviation systems, sensors, subsystems and components.
About the author: Tyler Davidson serves as a Test Engineer for the Missile and Sensors Propulsion Division of the Missile and Sensors Test Directorate at the U.S. Army Redstone Test Center. Tyler joined RTC after graduating from the University of Alabama in Huntsville 5 years ago with a Mechanical Engineering degree. Tyler has quickly gained a strong understanding of propulsion test concepts at altitude. Always striving to push RTC test capabilities forward, Tyler plans to implement air ejection technology (or similar) to simulate true static firing at vacuum, a capability that is not readily available for use within the country.
Social Sharing