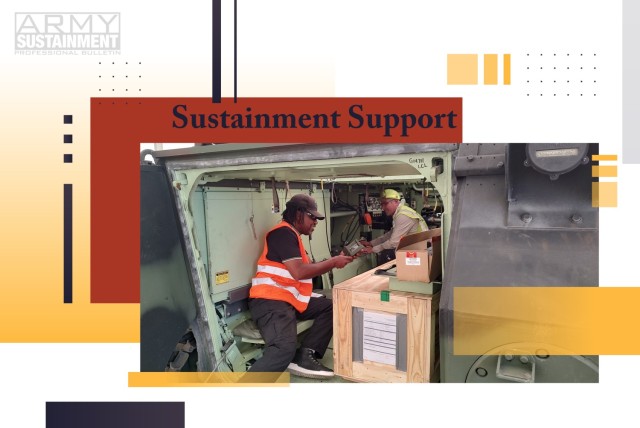
The 405th Army Field Support Brigade (AFSB) is assigned to the U.S. Army Sustainment Command (ASC) and, under the operational control of the 21st Theater Sustainment Command, U.S. Army Europe and Africa. The brigade is headquartered in Kaiserslautern, Germany, and provides materiel enterprise support to U.S. Forces throughout Europe and Africa, providing theater sustainment logistics; synchronizing acquisition, logistics, and technology; and leveraging U.S. Army Materiel Command’s materiel enterprise to support joint forces.
The 405th AFSB’s Army Pre-positioned Stocks-2 (APS-2) mission is resourced in part through the Enhanced Army Global Logistics Enterprise (EAGLE) program, which provides the contractor workforce needed to meet the Army’s APS-2 logistical support service requirements in Europe. Contracting officer representatives, in turn, oversee and ensure these contracted requirements are met.
Herbert Gately, chief of quality assurance (QA), Army Field Support Battalion-Mannheim (AFSBn-Mannheim), 405th AFSB, says QA representatives at the Coleman APS-2 worksite in Mannheim, Germany, play key roles in EAGLE contract oversight. Working onsite with government-contracted maintainers and logistics personnel, the QA specialists help ensure the APS-2 equipment is received, stored, maintained, modernized, and operationally configured within the contract scope to meet the requirements set forth by ASC and the Army.
At the Coleman worksite, this currently includes nearly two armored brigade combat team’s (ABCT’s) worth of APS-2 equipment, such as M1 Abrams main battle tanks, M2 Bradley fighting vehicles, and M109 Paladins, plus tactical wheeled vehicles, material handling equipment, generators, command and control communications equipment, basic issue items, and more. Later this year or early next, one ABCT’s worth of APS-2 gear is scheduled to move to the newly opened APS-2 worksite in Powidz, Poland, the Long Term Equipment Storage and Maintenance Complex.
The AFSBn-Mannheim QA team is staffed by Department of the Army Civilian employees and rotational, contingency Army Expeditionary Civilian Workforce deployed civilians with collective experience in QA, quality control, contracting, maintenance, supply, and transportation disciplines.
QA Team Objectives
The AFSBn-Mannheim QA team is tasked to ensure onsite contractors are accomplishing all care of supplies in storage work tasks (COSIS). This includes equipment maintenance, logistical support property accountability, and equipment issue in accordance with the contract’s performance work statement, the QA surveillance plan, onsite standard operating procedures, APS and maintenance policies, and best practices in the management of the program.
Specific Tasks and Key Methods
QA specialists perform three tasks: observe, document, and report. Key methods used by the Coleman QA team involve sampling contractor work orders based on workload, following quality trends, quality history, mission requirements, and non-compliance reports. These methods also include observing the contractor’s performance in the management of contract data, including executing Global Combat Support System-Army (GCSS-Army) maintenance and supply tasks, ensuring modification work orders completed by the contractor are inspected and applied on site, and documenting this in the Modification Management Information System (MMIS). They also review equipment presented to the QA office in MMIS to ensure safety message completion and documentation.
QA specialists ensure APS-2 equipment is repaired to Army standards and ready for use by observing contractor completion and performance of all test, inspection, and sustainment maintenance tasks.
Equipment accountability is another crucial mission when it comes to APS-2 readiness. The QA team helps oversee contractor-managed equipment and materials inventories, ensuring accountability and availability for issues through periodic sensitive item and cyclic inventories, physical security inspections, and supply audits using GCSS-Army.
Safety and security are paramount for all Army and contracted personnel at the Coleman APS-2 worksite. One of the missions of the AFSBn-Mannheim QA team is conducting daily walkthroughs while observing contractor ground guide procedures, use of personal protective equipment (PPE), periodic evaluation of equipment load tests, reviews of occupational health standards, and audits of APS-2 tactical wheeled and heavy tracked vehicle operator’s training programs.
To further complement Coleman’s worksite safety program, senior Army and contractor project management staff conduct weekly quality and safety walkabouts — the purpose being to visit the different work areas and offices and talk to employees about safety and quality. This allows employees at the ground level to voice their concerns and improvement ideas directly to management, fostering personal responsibility and ownership of the safety program.
The QA specialists at the Coleman APS-2 worksite also ensure hazardous material (HAZMAT) is documented, stored, issued, and disposed of per Army and host nation policies. This includes the placement of HAZMAT labels, use of HAZMAT safety data sheets, employee use of PPE, appropriate segregation of onsite corrosive and flammable items, and availability of fire suppression systems and devices, plus all the appropriate onsite certifications and training requirements for environmental safety and health personnel and leadership.
Recently, the QA team at the Coleman APS-2 worksite coordinated with other organizations within U.S. Army Europe and Africa to redistribute excess packaged petroleum products, which is considered HAZMAT. Redistribution and reduction of disposal costs for these products will reduce operational costs.
Coleman APS-2 worksite QA specialists ensure APS-2 stocks are stored and issued within the COSIS service schedules, extending equipment shelf life. In addition, aggressive monitoring of high-value COSIS priority group items, implementation of Integrated Logistics Support Center corrosion prevention programs, and observance of ASC Packaging, Storage, and Containerization Center guidance are strictly followed.
In the future, the AFSBn-Mannheim team of QA specialists and the cadre of contracting officer representatives will continue to work together to provide the critical oversight needed to maintain the readiness of APS-2 while expanding the team’s role in the oversight of emerging onsite equipment modifications and fielding.
The Coleman APS-2 worksite is located on a former Army airfield. In August 2021, U.S. Army Europe and Africa announced it would retain the Coleman worksite, which was previously scheduled to be returned to the German government.
The 405th AFSB’s APS-2 program provides turnkey power projection packages ready to deploy at a moment’s notice while helping to reduce the amount of equipment needed from the deploying forces’ home stations. APS-2 sites like Coleman help reduce deployment timelines, improve deterrence capabilities, and provide additional combat power for contingency operations. APS-2 equipment may also be drawn for use in training and exercises.
For more information on the 405th AFSB, visit the official website at www.afsbeurope.army.mil and the official Facebook site at www.facebook.com/405thAFSB.
--------------------
Kevin Grimm currently serves as a quality assurance specialist for Army Field Support Battalion-Mannheim at Coleman APS-2 worksite in Mannheim, Germany. He is also an Army Expeditionary Civilian Workforce employee deployed to Germany from Aberdeen Proving Ground, Maryland, where he is assigned to U.S. Army Communications-Electronics Command.
--------------------
This article is published in the Fall 2023 issue of Army Sustainment.
Social Sharing