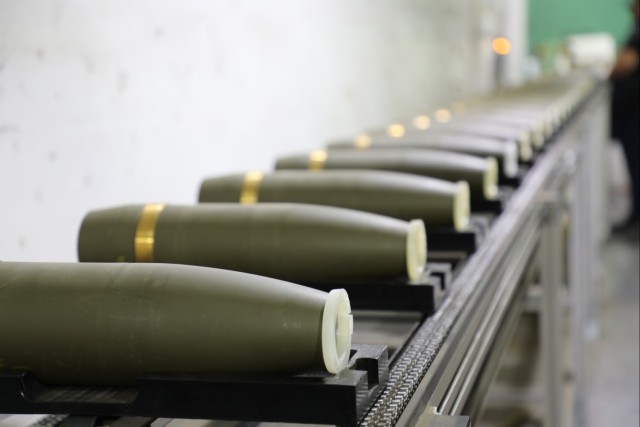
REDSTONE ARSENAL, Ala. – Logistics experts across the Army Materiel Command enterprise have been hard at work modernizing the Army’s supply chain over the past two years. The effects of that work have been felt for more than three months as AMC’s supply chain optimization efforts have been fully operationally capable at the headquarters.
Since going live with the SCO effort in February, AMC has been using data and forecasting models to track the successful transition and anticipate future challenges to its supply chain. Traditionally, projecting changes in supply chain vendors, capabilities and the needs of the Army has been a difficult task and required extensive lead time. With SCO, AMC seeks to be more proactive to global events that affect the supply chain.
“What we are seeing right now is a decreased order processing time by around 50% across Life Cycle Management Commands,” said Dr. Dan Parker, AMC chief of supply chain integration. “We are getting orders to units faster and more efficiently servicing the field.”
While most of the effects of SCO won’t be observed overnight, in a year’s time the forecasting model developed by experts in the AMC enterprise will be refined to best meet the needs of the Army.
Organic Industrial Base depots will also experience improved data integration with major supply partners, such as Defense Logistics Agency, and be more prepared to react to increases and decreases in product demand.
More than 2,000 employees in AMC’s supply chain workforce saw their positions realigned during the implementation of SCO. Position descriptions were standardized across the field to align the workforce according to best practices, while keeping the uniqueness of each LCMC intact. Throughout this change, AMC has been closely tracking employee morale and using their feedback to evolve SCO.
“The indications we’re getting are that much of the workforce is excited and welcoming the opportunity to have their position realigned under SCO,” Parker said.
The realignment included AMC forming a Supply Chain Optimization Integration Cell to develop metrics and workflows to support operations globally, from the strategic to the tactical level. The cell comprises supply chain professionals across the AMC enterprise, many of them in developmental positions, who are bringing their expertise to the headquarters level.
“What the cell has accomplished in 90 days may have taken a year before SCO,” Parker said. “The difference is that our developmentals see this as work they want to do – and even enjoy. It’s stimulating and relevant to the position they will return to, whether it’s at Letterkenny Army Depot, Aviation and Missile Command or back into headquarters AMC.”
The synergy achieved by utilizing subject matter experts from across the field was a valuable addition to the execution of SCO, which Parker says wouldn’t have been possible without the buy-in from senior leaders across the AMC enterprise.
“What truly drove us to gel was our senior leadership,” Parker said. “When they stepped in, they helped us execute SCO in record time. What should have been a 6-to-8-year project was accomplished in 24 months. We owe that to every individual who has participated.”
Social Sharing