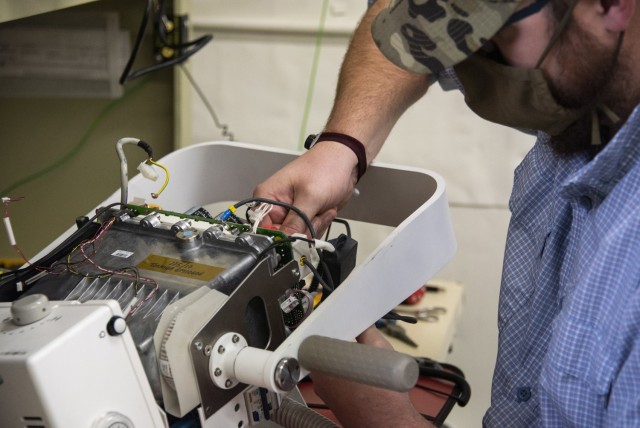
TRACY, Calif. -- Even in overseas locations, expert sustainment-level medical maintenance support is just a phone call or email away.
The teams at the U.S. Army Medical Materiel Agency’s Medical Maintenance Operations Divisions, or MMODs, continue to leverage “telemaintenance” capabilities to bring support directly to forces in forward-deployed environments.
“Telemaintenance is a communications tool that allows technicians to share equipment information, views of the equipment and troubleshooting techniques, and in some cases enables software updates to be transferred electronically,” said Kevin Culihan, deputy director of USAMMA’s Medical Maintenance Management Directorate.
One of the latest cases happened this past fall when two computed tomography, or CT, machines in Iraq and Kuwait broke down and needed repairs. The unit commanders knew who to contact.
Technicians from the Forward Repair Activity-Medical, or FRA-M, team at USAMMA’s MMOD in Tracy responded to begin diagnosing and fixing the problems remotely.
“Both situations were resolved by sending replacement parts to the unit,” said Ian McNesby, production controller at MMOD-Tracy. “Our telemaintenance channels helped speed that process.”
While advanced medical technology has contributed to the lowest casualty rates in history, it has significantly increased the complexity of deployable medical systems, Culihan said.
“Advanced medical systems, particularly on an austere battlefield, are a significant maintenance challenge for the repairers responsible for maintaining and ensuring the equipment is available,” he said. “Medical equipment, such as radiology, laboratory and pulmonary, are unique and complex enough to merit their own maintenance specialty.”
That’s where USAMMA’s forward repair teams come into play, able to assist Soldiers trained as biomedical equipment repair specialists, often known by their military occupational specialty, 68A, just as if they were on ground right alongside them.
In the case of the CT device at the Baghdad Diplomatic Support Center, Tracy technicians utilized secure telephonic and messaging channels to assist the unit with troubleshooting and diagnosis of the issue.
McNesby said the FRA-M team determined there was a computer software problem, as well as the need to replace several components in the imaging system. The computer was sent back to Tracy for reconfiguration then shipped back to Baghdad.
“When the computer got back on site, our technicians here using telemaintenance walked through the process to swap out the computers, make sure everything was working and start them on the calibration process,” he said. “… If you don’t have those options, you have to physically send someone down there and it costs the government quite a bit of money to do that.”
In Kuwait, the CT system in question was operable, but the unit commander had concerns with the device’s brake system, which provides stability during operation, McNesby said.
“If we’re dealing with them remotely, we can diagnose the problem, order them the parts, so the only thing they’re waiting on is having the parts arrive,” he said, adding that typically cuts turnaround time by several weeks when compared to sending a technician to the location.
“We would be adding additional time that they can’t afford to lose onto that timeline,” McNesby explained. “In some cases, depending on where we’re talking about, that may be the only CT they have within a 100-mile radius that they could use.”
While MMOD-Tracy sends technicians to theater annually for scheduled maintenance and calibration checks on medical equipment, telemaintenance allows them to provide expert support throughout the year as well -- regardless if a technician is on the ground or not, McNesby said.
“With telemaintenance, they don’t have to be physically there in front of the equipment to understand what the customer is saying,” he said. “That expertise is invaluable in diagnosing problems, and their experience and familiarity with the devices definitely comes into play.”
McNesby also was quick to credit not just his technicians at Tracy, but also the USAMMA procurement team that assists in quickly acquiring the needed parts and shipping them to customers in a timely fashion.
“Telemaintenance is a true a combat multiplier that reduces the stress of 68A biomedical equipment technicians, while simultaneously enhancing patient safety and patient care on the battlefield,” Culihan said.
USAMMA is a direct reporting unit to Army Medical Logistics Command, the Army's life cycle management command for medical materiel.
Social Sharing