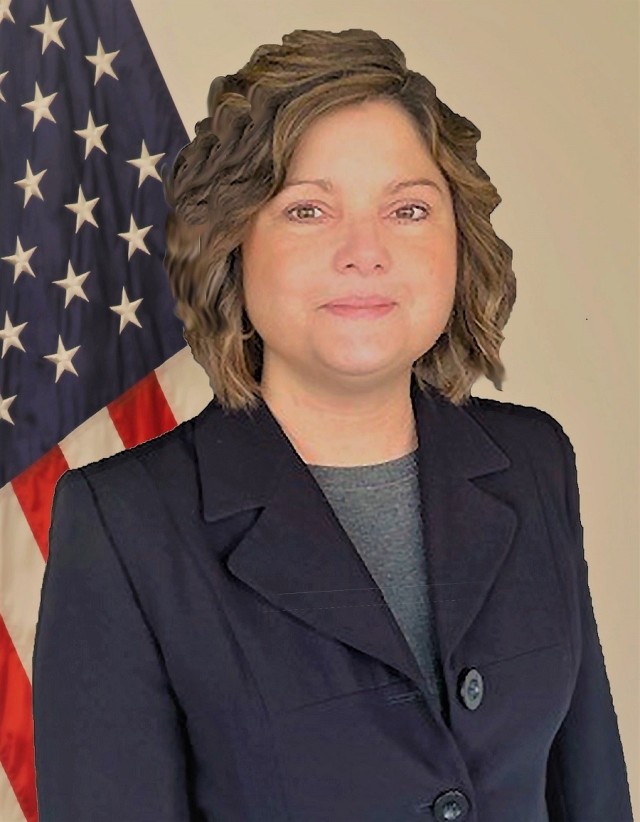
Part of the Security Assistance Command’s support to partners and allies goes beyond just facilitating military sales to other countries. It can also include the repair and return of parts and systems of items in foreign military sales.
Kelly Gibson, chief of the Commercial Repair and Return Branch in New Cumberland, Pennsylvania, oversees this important program. She is also the employee of the fourth quarter of fiscal year 2022 for USASAC.
Gibson manages two five-year indefinite delivery, indefinite quantity contracts valued at $199 million. She is leading efforts to recompete and award a new $499 million base contract for 2023-28 repairs of items in foreign military sales.
Once a contract has been awarded, Gibson oversees all CRR repair support, from development of the acquisition requirements package to return of repair-complete parts to partner nations. She also monitors vendor performance to ensure it meets contract standards.
“Kelly is so deserving of this award because of her contributions to the enterprise, few could have achieved what she has, and because she is a genuinely nice professional who bends over backwards to help our partners. USASAC is blessed to have an employee of her caliber,” Ann Scott, chief of USASAC’s G4 Services and Products Division at New Cumberland, said.
For each contract, Gibson performs the critical accountancy function of tracking and managing all repair costs to ensure that costs do not exceed each contract’s authorized ceiling. Failure in this area violates the Anti-Deficiency Act and is punishable as a criminal offense.
Gibson manages over 2,050 repairs annually, including approximately 1,700 repairs that are open as of late 2022. Her complex and important duties demand that she demonstrates business acumen and possess an enterprise perspective necessary for building working relationships with key stakeholders across the Army security assistance enterprise.
Another reason Gibson is being recognized as the employee of the fourth quarter is her persistent efforts in achieving approval of and implementing a new 4% program support charge for the ASAE CRR program.
Prior to Gibson’s management of the CRR program, it provided above standard level of support at no charge to USASAC’s partner nations. This resulted in a lack of resources to support the CRR program and in violation of security assistance policy. The PSC gave the program a resourcing stream and allowed it to continue operating on behalf of our foreign military sales partners.
To get approval of the PSC, Gibson worked tirelessly for more than three years with USASAC, and Department of Defense level agencies to make the case for why this charge was necessary. In 2022, the PSC was officially approved, which currently affects 35 partner nations and 111 FMS cases in the CRR program.
To date, 32 of the 34 partners using the CRR program have concurred with the PSC and continue receiving commercial support. Their concurrence is due in large part to Gibson’s work to improve program performance, keep the ASEA and our partners informed of progress toward the support charge, and to ensure that all stakeholders understand their responsibilities regarding implementation of the PSC.
She also proactively realized that this program would need real and continuous improvements to keep it successful. As a result, she continues to implement numerous CRR business and process improvements. These initiatives have cut repair turnaround time in half, which has eliminated unnecessary actions by our partner nations, the regional operation teams, and the contracting agencies. Many of her efforts shortened repair times by literally hundreds of days in many cases. Her efforts also added transparency to the program and built trust and proficiency among our partner nations and the country case managers. All of this helped ensure the proactive, effective monitoring and management of repairs.
All while pursuing approval of the commercial repair and return program support charge. “Gibson also masterfully managed a heavy workload, one that has grown from 834 repairs in 2019 to 1,705 in August 2022,” Scott said.
Gibson and her team have implemented numerous other process improvements saving hours across the enterprise and making efficient use of our partners’ limited foreign military sales funding. Among the most significant outcomes of these initiatives is a reduction in average repair turnaround time from 980 days to 518 days. This is well below the ASAE standard of 557 days per repair and a major improvement throughout the enterprise.
Social Sharing