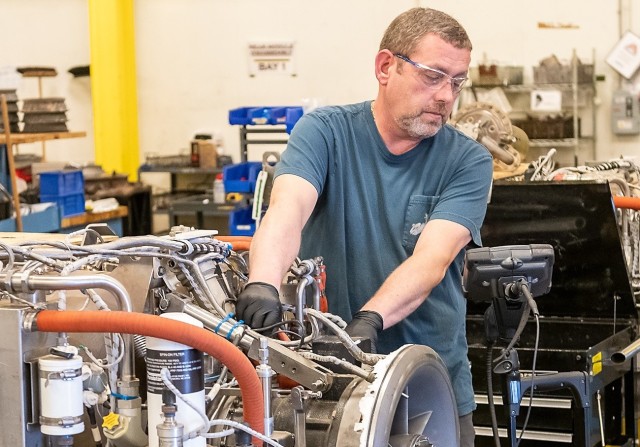
ANNISTON ARMY DEPOT, Ala. – The condition-based overhaul program was created in 2008 with the potential to save customers hundreds of thousands to millions of dollars. The cost savings generated by three or four CBO program engines could purchase a brand new engine.
In 2010, members of the workforce who were selected for positions in the CBO program, began working on the proof of concept. Proof of concept allowed workers to demonstrate how practical the program would be if implemented properly.
One year later the CBO program implemented a pilot program involving 16 AGT1500 engines. Steve Norton, lead turbine engine analyst, said the program is a partnership with Honeywell and KBR, two government contractors, to generate cost savings. The program also created a need for turbine engine analysts.
A total of four turbine engine analysts, with almost 75 years of combined turbine engine experience, are responsible for managing, monitoring and evaluating the program. The analysts must remain in constant contact with all shops supporting the turbine engine functions.
If an asset or part is damaged or worn, the analysts must diagnose the
cause and provide a solution. Jason Haney, turbine engine analyst, summed up their responsibilities in a nutshell. “It is our job to narrate the story the engine is telling us,” he remarked.
The analysts come from different backgrounds within the turbine engine shop, which is beneficial in analyzing and troubleshooting an engine. Each analyst has a unique perspective when they inspect an engine. They work as a team exchanging ideas and diagnosing problems they may have never seen before.
Before the engine is inducted, a combination of the work planning guide interval readings and the findings from the initial visual inspection allow the analysts to create the scope of work for the engine. The scope of work can be amended after the engine has been inducted following disassembly and further visual inspection of engine parts.
The Tiger Integrated System is a database used to track data and maintenance feedback around the world. The analysts can track trends, make adjustments to the scope of work and provide suggestions to the customer regarding changes to the engine design, improve functionality, adapt maintenance schedules and identify trends.
This data is gathered by field service representatives from TACOM, field service engineers from Honeywell and depot analysts. All of these subject matter experts maintain open lines of communication and build rapport with one another. This creates what Haney refers to as a communication triangle between ANAD, TACOM and Honeywell.
“The ultimate goal,” Norton said, “is to provide quality engines for the warfighter while saving money for the taxpayer.”
Social Sharing