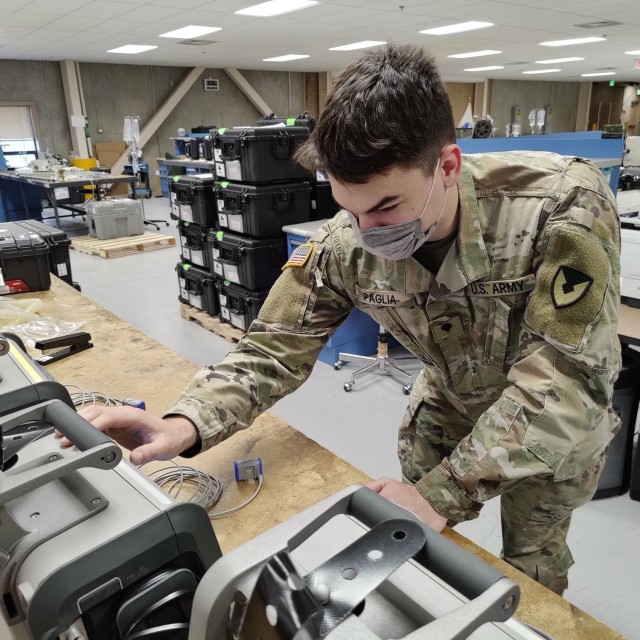
RENO, Nev. — When new medical equipment is fielded to the warfighter, medical maintenance experts from the U.S. Army Medical Materiel Agency work quickly to ensure they can handle any support needs.
That often means continuing education and training through equipment manufacturers, as was the case with a recent training event to get acclimated on a new ventilator system.
Eight technicians — two each from USAMMA’s three Medical Maintenance Operations Divisions, or MMODs, as well as two more stationed at Sierra Army Depot — traveled to Reno in early November to take part in manufacturer training on the new “transport” ventilator. The unit combines the functionality of an ICU ventilator in a compact and rugged package needed in the field.
The training helps technicians build familiarity with the product’s maintenance and repair procedures to ensure a high level of readiness support for Soldiers.
“Readiness is our first priority, and we achieve it by having technicians fully trained to the manufacturer’s service standards,” said Jose Vasquez, director of the MMOD-Hill, located at Hill Air Force Base in Utah.
This training is a requirement from the manufacturer before technicians can order parts and perform invasive services and repair procedures. It also helps build the maintenance skillsets, gives authority to the MMODs to order repair parts and mitigates any potential loss of warranty or liability that may arise from untrained technicians who could damage equipment.
“For a class that only lasted two days, it was packed with useful information and new skills,” said Mark Kisel, a biomedical equipment technician from MMOD-Tobyhanna in Pennsylvania.
Kisel said the training included overviews of preventative maintenance procedures, including common issues and troubleshooting tips at each stage. It also taught disassembly, component identification and repair technique.
“Knowing how to properly execute both preventative maintenance and repairs ensures that USAMMA can provide all levels of service to support this equipment throughout its entire lifecycle of use with the Army,” he said.
Each MMOD under USAMMA, a direct reporting unit to Army Medical Logistics Command, serve as a center of technical excellence in different disciplines, including medical imaging, pulmonary and clinical lab equipment. They provide sustainment and depot-level maintenance support to all Army components, as well as authorized Department of Defense activities and other federal agencies.
Since completing the two-day training course, participants returned to their respective depot locations to not only provide training to colleagues, but also develop internal forms and manuals for the equipment based on manufacturer’s specifications and in compliance with Army regulations, Vasquez said.
“Having firsthand knowledge of the correct service procedures is critical because non-user-friendly manuals can be misinterpreted, so calibration and testing could potentially be incorrect which may result in catastrophic failures that could be traced back to the technician and leadership,” he said. “Being OEM trained removes subjectivity and arbitrary decision-making which helps standardize testing procedures and decreases variance.”
And as always, new equipment brings increasingly complex and diverse capabilities and operating systems.
Kisel said this type of training is helpful to not only provide basic troubleshooting, but also in-depth explanations of the systems and capabilities directly from the manufacturer.
That further translates to knowledge and skills throughout the bench of USAMMA technicians, who then can share this information and support with Soldiers on the ground. It also provides savings in the form of time and money when repairs are needed.
“At the depots, we can complete all levels of repair, cutting costs and repair time by reducing the need to refer repairs to the manufacturer,” Kisel said. “In short, these skills save the Army money, increase consistent readiness and ensure that our warfighters in the field have the equipment they need to save lives.”
Social Sharing