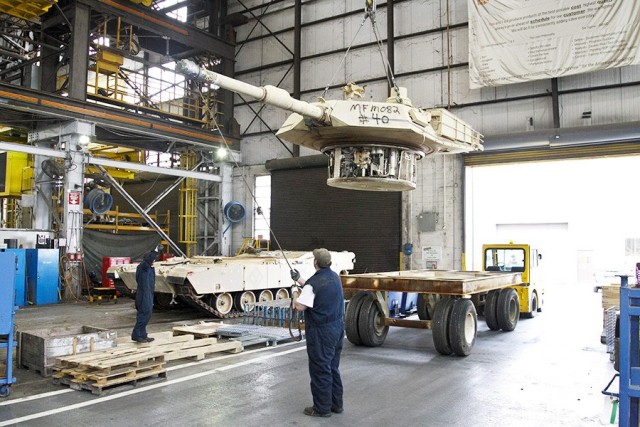
ANNISTON ARMY DEPOT, Anniston, Ala -- As we continue to reflect on some of the key elements that have made Anniston Army Depot a staple over the last 80 years, we’d be remiss if we didn’t include the assignment of the maintenance mission for the overhaul and repair of combat vehicles that started in the 1950s.
Critical to that charge was the need for a facility to house the varied activities of rebuilding armaments and ordnance vehicles which were formerly scattered throughout a dozen depot buildings.
Construction of the Maintenance Shop, now known as the Combat Vehicle Repair Facility, concluded in March 1953. The facility cost $3.25 million to build and the equipment cost was $1.25 million.
The building was 50 feet high and the structure had three bays, each 850 feet long, two of which were 100 feet wide, and the center bay was 60 feet wide. At that time, production lines stretched from one end to the other, with various contributing operations placed where needed in the complete dismantling, overhaul and reassembling of all types and sizes of Army fighting equipment.
The installation of equipment was complete during the second half of 1953. All combat vehicle rebuild operations, including components such as engines and power trains were then done in this building.
Over the years the building added additional width, making it 260 feet wide, making it the largest building on the installation.
Throughout its 68-year life span, the facility has seen numerous types and variants of combat vehicles.
“Combat vehicles leave here in like new condition,” said Steve Pennington, director of production. “The building has seen major changes over the years, but one thing that hasn’t changed is the dedication of employees who work inside this building, which is the size of three football fields. They endure tough conditions to make sure the disassembly and reassembly of combat vehicles are of the best quality. They realize there is zero room for error. Our equipment has to work right when needed.”
Today, the building houses:
· Seventeen combat vehicle models, including the M1A1/M1A2 Main Battle Tank, ABV- Assault Breacher Vehicle, JAB- Joint Assault Bridge, AVLB- Armored Vehicle Launched Bridge, FAASV- Field Artillery Ammunition Support Vehicle, Paladin, M9ACE- Armored Combat Earthmover, M88A1/M88A2 Recovery Vehicle, M113FOV to include, OSV, M577, MBT, M1064, M1068, and all the Stryker variants.
· There are 391 employees in the building – mechanics, welders, machinists, parts attendants, quality inspectors, and partnership employees who help to ensure we have the parts needed to fulfill the mission.
The building is set up with lines of bays, but there are only two fixed pieces of machinery in the facility. Everything else can be moved to accommodate whatever workload is most pressing and whatever mission is most vital to our Soldiers and Marines.
Social Sharing