ANNISTON ARMY DEPOT, Ala. -- Phillip Thompson has 33 years of federal civilian service and two decades of that time has been spent in the Directorate of Production’s hydraulic shop. The last three years, Thompson has operated one of the hydraulic shop’s Universal Hydraulic Test Stand.
The test stand, installed in 2008, is utilized in testing components found in a few combat vehicles common to the depot. These vehicles include the Stryker family of vehicles, M88 A2 recovery vehicle, and the M1 Abrams tank. The Stryker family of vehicles are the most common components tested at Thompson’s work station.
Thompson was testing a Stryker engine manifold as we arrived at his work station. The engine manifold distributes hydraulic oil throughout a circuit. The flow of pressurized oil is regulated by hydraulic valves installed within the manifold and directed through hoses to some kind of work device, such as a hydraulic motor. The Stryker engine manifold controls the winch, height system as well as the heat and air conditioning. “That might be the most important thing I’m testing,” Thompson said, in reference to the air conditioning and heating.
To begin his test procedures, the engine manifold is placed in a cradle inside the test stand and held in place by using a long, threaded bolt tightened down with a nut. Thompson ensures all solenoids and valves are torqued in place. He connects a hydraulic fluid line, closes the sliding door of the test stand and the proof test is ready to begin.
The proof test, also referred to as the leak test, allows Thompson to check for any leaking hydraulic fluid. The operational test ensures hydraulic fluid is dispersed through the solenoids, which open and close the valves, “Valves open and close like turning a light switch on and off,” Thompson said. The flow test ensures the component is using the correct flow rate measured in gallons per minute according to the National Maintenance Work Requirement, also known as the NMWR. During the flow test, Thompson must perform the proper adjustments using a ratchet with a hex bit.
Thompson could not have done his job without the support of the workforce in the shop, “The main thing is having the parts. The people here do a good job building the assets and keeping the work going out to the customer.”
Tommy Dulaney, supervisor of the hydraulic shop, spoke about all of his employees. “My team is the most important asset on this depot,” he said. “The hydraulic shop’s mission is to support the warfighter. My employees do their best to give the warfighter the best equipment we can offer.”
Tours are conducted throughout various shops across the depot. Whenever soldiers are part of the tours in the hydraulic shop, Thompson takes notice. “It’s good to see the recipients of our products," he said. "We are ensuring they have everything they need.”
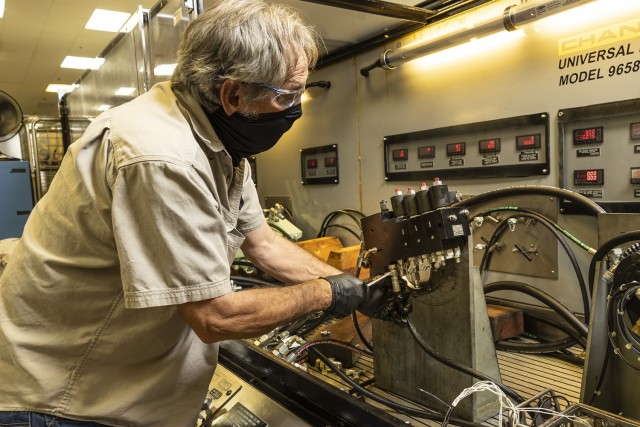
Social Sharing