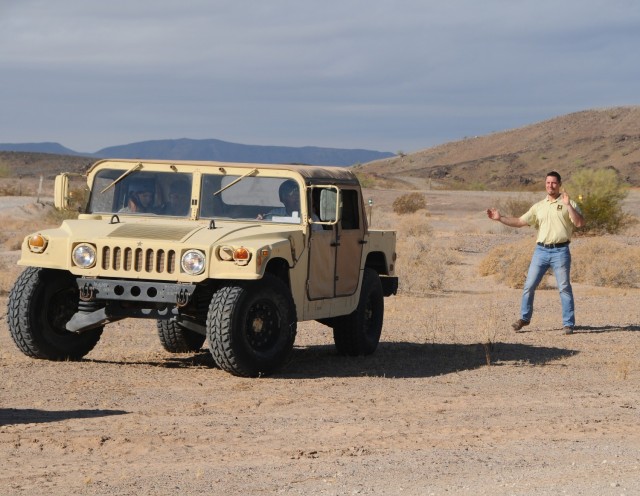
U.S. Army Yuma Proving Ground’s mission of testing nearly every piece of equipment in the ground combat arsenal requires the skill of hundreds of talented engineers who hail from all parts of the country.
Many rise to distinction within the test community and spend entire careers here, even if they never imagined working and living in one of the world’s most extreme desert environments.
An example is Rob Fillinger, a test officer in the Combat Automotive Systems Division who enjoys the variety and importance of YPG’s workload.
“There’s no such thing as a typical test, and that’s one of the beauties of working at YPG, especially in the automotive branch. There are so many different platforms that we encounter, and many in a different phase of their acquisition cycle, from prototypes to legacy programs.”
In over 10 years here he has worked on virtually every platform the branch has tested, but is particularly proud of his work testing the Mine Resistant Ambush Protected vehicle.
“I like that platform just for the fact that it has saved so many lives. It was crucial for our Soldiers in Afghanistan and Iraq. It’s near and dear to my heart.”
Born in tight knit Livonia, Michigan, Fillinger’s father worked for the local school system and his mother had a dog grooming business. About fifteen miles northwest of Detroit, the auto industry was ever-present in the community.
“I thought for sure I’d be working for one of the Big Three. I didn’t have any one particular car company in mind: it wasn’t who I was working for, it was what I was doing that I was interested in.”
Fillinger was always mechanically-minded.
“Growing up I always wanted to know how things worked. At an early age I was taking things apart and putting them together again.”
In high school he ran on the track team and played basketball and football, where future NFL linebacker Tim Shaw was one of his teammates and friends. He worked through school, too.
“I was always a really hard worker growing up. I would scavenge broken lawn mowers, fix them up, and sell them.”
After high school, he got his degree in mechanical engineering from the regarded Lawrence Technological University and worked in a fabrication lab there concurrently. Several months after he graduated, he landed a job at Chrysler’s Technology Center doing vehicle emissions testing, and thought he had finally arrived. Then fate intervened: it was the autumn of 2007 and the economy was on the cusp of what ultimately became the Great Recession.
“It was a really tough time to be an engineer in the auto industry when I graduated. The week I got there they announced 17,000 layoffs: it took about three months to reach me.”
He lost his job less than three weeks before Christmas.
“I had a good friend who grew up across the street from me who was a foreman at a construction company. That kept me on my feet for a few months while I was on my job hunt.”
Meanwhile, the housing market was collapsing as well. He knew that whenever the auto industry eventually began to recover, he would be competing against a glut of former workers with more experience in the industry than he had. Some of his friends had moved to Arizona seeking other opportunities, and he posted his resume in one of the major regional newspapers. A job recruiter found it, and called him with information about Yuma Proving Ground.
“I had never even heard of YPG,” Fillinger said with a laugh.
He started here in March 2008 and quickly distinguished himself as the Combat Automotive Systems Branch racked up record-breaking levels of work: well over one million direct labor hours in a single year at its peak. His workload tended toward performance and environmental testing.
“To me, those types of test are more interesting and dynamic. There is a lot more data to go over and analyze.”
He has been civilian of the quarter for the proving ground and, so far, received two Army Achievement Medals for Civilian Service. He even occasionally finds himself testing Army vehicles at the General Motors Desert Proving Ground located on leased land within YPG.
“I’ve been over there several times and it was always a good experience testing there. The size of their dynamics pad alone makes it a great facility.”
Though he never dreamed of working in such a place, Fillinger has no plans to leave. He calls his co-workers his “Yuma family.”
“There’s a lot more money in private engineering, but I think the work here is a lot more fulfilling. When you drive out of the gate and past the Big Guns at the end of the day, you know you did something good for our country and our Soldiers.”
Social Sharing