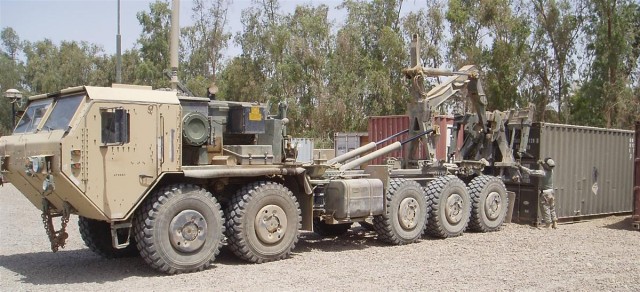
CAMP LIBERTY, Iraq - The Palletized Load System is odd looking but is touted as the vehicle backbone of the Army's distribution and resupply system.
The 89th Transportation Company from Fort Eustis, Va., inherited sixty PLS after driving M915 tractor-trailer vehicles for two of four deployments.
Traditionally an M915 company, the 89th Trans. Co., had to take extra measures in learning to operate the PLS. Like the M915s, the PLS can carry containers and all classes of supply during a mission, however, there are some differences.
Unlike the M915, the PLS is integrated with both the cab and trailer as one. The cab of the tractor is situated in front of the motor and the first two axles in a design that dates back to the 1950s.
In the mid-1950s, the Army started looking for a better cargo truck; one that could traverse all types of terrain, carry more equipment and keep up with its highly-mobile combat forces. To do that, the Army turned to commercially owned companies that designed earth moving equipment.
Beating out two other companies, Caterpillar won the contract design of the M520 "Goer." The Goer was an 8-ton cargo truck with articulating steering and amphibious capabilities. It was first used during the Vietnam War, but its lack of suspension and slow top speed made it inadequate for traveling on hardened surfaces.
In the 1980s, the Army replaced the Goer with Oshkosh's Heavy Expanded Mobility Tactical Truck. The PLS is a variant of the HEMTT and entered the service in 1993, first being used in Bosnia by the 1st Infantry Division.
The PLS can carry its loads on a flat rack, which are inter-changeable, and uses a hydraulically powered hook arm to lift or lower the flat rack. This greatly reduces the need for any type of material handling equipment such as a crane or forklift.
Spc. Michael Moore, a native of Deer Park, Texas, and a PLS operator said, "It's easy to pick up loads with the PLS. You don't have to wait for a fork lift; you just pick up the load and go."
According to Oshkosh, a driver can operate "without leaving the cab. The driver can load or unload the truck in less than one minute, and do the same for both truck and trailer in less than five minutes."
"The CTIS is nice too" Moore said. The central tire inflation system allows the operator to change the amount of air in the tires with just the touch of a button.
The design of the PLS also has some added benefits unseen before Operation Iraqi Freedom.
Spc. Donald Blandini, a Saugus, Mass. Native, said "I feel safer in a PLS compared to a 915. It's a better concept."
While it does have advantages, the PLS has its share of disadvantages as far as the limited turning radius to maneuver in tight areas, especially in supply yards.
The 89th Trans. Co. mission has many logistical advantages as far as operating a PLS. One advantage is the container handling unit. This feature includes a big hand which extends to pick up a container without a flat rack. Some trucks also come with a material handling crane to allow loading of other various pieces of cargo.
The 89th Trans. Co., will return to its fleet of M915s but has made full-use of the PLS, a vehicle that lives up to the title backbone of the Army's distribution and resupply system.
Social Sharing