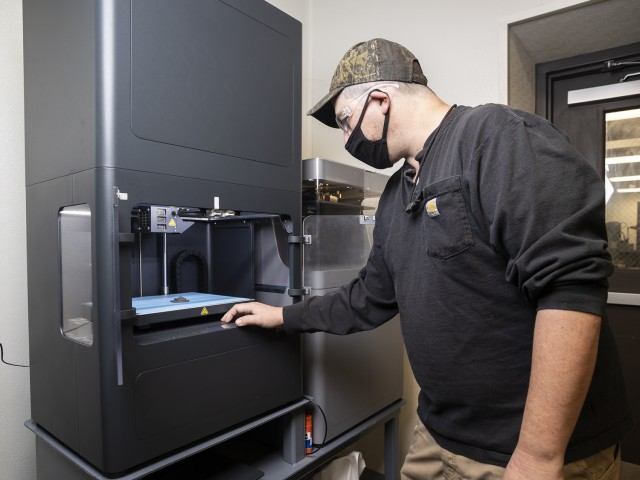
ANNISTON ARMY DEPOT, Ala -- A new 3D printer arrived last week at the machine and weld shop in the Directorate of Public Works.
The new printer, a Makerbot Method X, joins two other 3D printers in the shop that are used to make prototypes for fixtures and tooling for the Directorate of Production. They are also used to create replacement parts for industrial equipment.
“I think everyone in the shop is more excited than anything,” Jeff Thompson, toolmaker supervisor, said about the new printer. “It helps them out a lot.”
The first 3D printers arrived in the shop last summer. The Markforged Metal X and X7 printers, which cost over $250 thousand, allowed the shop to begin printing both metal and carbon fiber objects. The addition of a new printer will allow them to be more efficient.
Thompson came up with the idea to use 3D printers a few years ago while working with a former depot leader on a project. He recalls they were trying to find a solution for a part and a decision was made to make the purchase.
Eventually, acquiring a 3D printer became a part of the command’s Top 10 list.
The acquisition process took some time, but Thompson and his staff are grateful and appreciative for the efforts of everyone involved.
The printers bring a lot of benefits to the shop, allowing them to make both simple and complex production parts on-demand.
Matthew Chambers, a mechanical engineering technician, is the primary user of the 3D printers. For him, the printers allow him to reduce man-hours.
“We’ve actually taken a work order where we completed the whole job on printers,” Chambers said. “That equated to about two man-hours.” Thompson added, “We probably saved about a thousand dollars by doing that.”
Previously, a machinist would have to mill parts or use the CNC machine for every project or idea which would use many man-hours and materials. And when something went wrong they would have to “just work it out” according to Chambers. This is why Chambers said, “The 3D printer is just better.”
But the 3D printer is not a replacement for production workers. They are best for resolving issues with parts. “When you think about machinists, they are like artists,” Thompson said. “They put a lot of time into their projects with hopes of it being error free.”
The printers are also useful when engineers need models quickly. “We can go from an engineer’s idea to fruition quickly,” Chambers said.
The time it takes to print objects depends on the complexity. Some projects take two hours while more complex projects can take a day. Currently, they are working on a model of a gun cradle for the Directorate of Production Engineering that will be used during the process of testing and repairing gun cradles.
Grant Greenwood, an electronics engineer in DPE, recently worked with the shop to create stocks for a fixture on a small arms weapon. “These items were complex shapes that were difficult to manufacture,” he said. “So 3D printing was a good option.”
Thompson knows the printers are not miracle workers, however. “It’s not a solution to all manufacturing problems,” he said. “It’s another tool in the shop.”
Safety was a major concern when choosing the type of printers they needed. According to Thompson, other printers have lasers that produce metal powder dust that require the user to wear a lot of personal protective equipment. “I researched and found the safest one,” Thompson said.
Thompson added that these printers are environmentally safe. In fact, they are marketed as desktop 3D printers designed to be in an office setting. Gloves are the only PPE required. However, they are only used when handling the wash solution needed to remove wax after an object has been printed and before it goes into the printing oven.
In addition to the 3D printers, a 3D scanner was purchased. The Creaform Handyscan, which cost around $90 thousand, keeps them from having to get out calipers and measure objects. Instead, they can scan something, it takes the dimensions and loads a model into a computer for printing.
The best part, “It’s really accurate,” Thompson said of the scanners.
Having the scanner and printer combination allows them to make almost any object that comes into the shop. Thompson also touts the way scanners can check for defects in parts. “I can see employees using this to check crates of parts for defects in the future,” he said.
Social Sharing