ANNISTON ARMY DEPOT, Ala -- While many Anniston Army Depot employees were enjoying a week of down time during the holiday period in December, some of the teammates in the Directorates of Public Works and Production Engineering were working behind the scene to ensure the installation’s equipment and machinery remained operational.
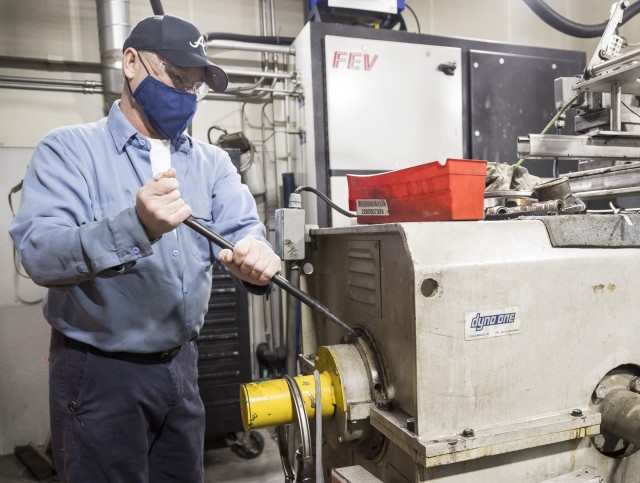
On a daily basis, the depot provides world-class refurbished major end items, components and forward readiness support to the warfighter to include combat vehicles, artillery, assault bridging, small caliber weapons, locomotive, rail equipment and non-tactical generators.
Conducting preventive maintenance is an important of accomplishing the mission. And the periods when the least amount of employees are present is the ideal time to improve the performance and safety of the equipment. The goal is to maximize the useful life of the equipment.
“We’re working to increase the life expectancy of the equipment, have fewer interruptions to production and improve efficiency,” said Matt West, a utilities supervisor in DPW. “Anything that is in good repair tends to operate a little better. Some areas we can’t control, such as the treatment plant. We took this time to do a lot of work in that area.”
While July and December are ideal times to perform maintenance, those dates aren’t etched in stone. “We have to be prepared whenever the time presents itself,” West added. His team consists of over 30 position titles, to include electricians, plumbers, air conditioning mechanics, machinists, boiler plant operators, treatment plant operators and others in the Electric and Refrigeration and Plumbing Shops.
Work was also performed in Combat Vehicle Repair Facility by other members of the DPW team -- Machine and Weld Branch, and the Fabrication and Support Branch. This facility, 50 feet high, 850 feet long and 260 feet wide, is the largest building on the depot.
“We repaired the floor plates used to bring the vehicles in for disassembly and reassembly and applied non-skid coating backs to those steel plates,” said Rickey Cline, roads and grounds supervisor. Painters stripped the old paint and replaced it with brand new non-skid painters. Additionally, two water lines were repaired and valves were added.
Welders and mill wrights performed work around the spinner hanger, dynamometer and test cells.
“There are certain maintenance activities, such as the spinner hanger, engine/transmission test stands, that require taking the equipment offline for an extended period of time,” said John Rogers, chief of the DPE’s Equipment Maintenance Division, which is comprised of electrical, millwright, and maintenance support shops.
“We used this time to perform tasks that may not be mandatory but require shop downtime to complete,” he said. “For example, the removal and/or installation of equipment located in the center of a shop. While it doesn’t hurt that the old equipment is there, you may have to stop production to perform the required work. It enables us to do it during a scheduled timeframe.”
Additionally, Rogers’ team also changed filters and rotated bearings on the test stands and serviced the spinner hanger and blast booth. They also conducted an overall equipment inspection and replaced parts that were reaching the end of their lifespan.
“It’s like going to the doctor for an annual physical,” he said. “You want to catch the little issues before t
They require going to the hospital. Thanks to the dedication of the maintenance team, we were able to complete this work on the major pieces of equipment, with no hiccups.”
Social Sharing