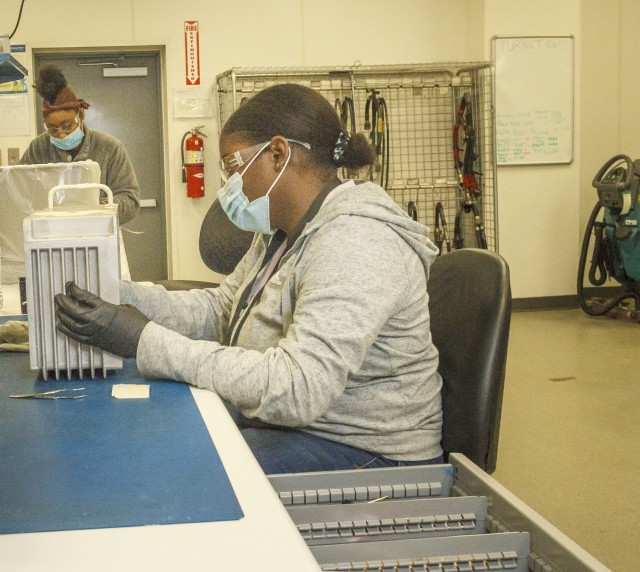
ANNISTON ARMY DEPOT, Ala. -- The Safety Office recently conducted a perception survey, looking at areas of safety and health at the depot. The following information covers areas which needed to be addressed and the ways in which safety at Anniston Army Depot can be improved. An additional area, reporting of unsafe working conditions, will be detailed in the Oct. 15 issue of TRACKS.
I have seen the industrial hygiene survey in my work space.
Industrial Hygiene surveys can be printed out at any time from the Industrial Hygiene office. ANAD Industrial Hygiene sampling results and notification letters are sent to supervisors within 15 days after the cost center’s assessment has been completed. Supervisors should review the results and ensure everyone is aware of hazards in their work area. The sampling results should be post on the cost center safety board.
I have participated in the development of safety products for my job.
Job Hazard Analyses are reviewed and updated each January. Supervisors update JHAs throughout their cost centers and employees are made aware of the hazards present in their work areas. Employees should know the hazards associated with the work they perform and the proper personal protective equipment to wear when completing their job. Employees should be involved in the development, update and review process of JHAs.
Management sets a good safety example through words and actions.
ANAD’s management and the Safety Office want the depot to be the safest workplace possible. To assist in this, the following regulations have been recently updated:
• ANAD Reg 385-2 (Ergonomics Program)
• ANAD Reg 385-3 (Reporting of Unsafe and Unhealthful Working Conditions)
• ANAD Reg 385-4 (PPE)
• ANAD Reg 385-5 (Hazard Communication Plan)
• ANAD Reg 385-6 (Emergency Eyewash and Safety Shower Program)
• ANAD Reg 385-7 (Accident Investigation and Reporting)
• ANAD Reg 385-8 (Lockout and Tagout Program)
• ANAD Reg 385-9 (Ladder Safety Program)
• ANAD Reg 385-11 (Fall Protection Program)
• ANAD Reg 385-15 (Compressed Gas Cylinder Safety)
• ANAD Reg 385-16 (Radiation Safety Program)
• ANAD Reg 385-19 (Haz ID Risk Assessment and Control)
• ANAD Reg 385-24 (Office Safety)
• ANAD Reg 385-25 (Dipping Coating and Degreasing Operations)
• ANAD Reg 385-27 (SOH Inspection Program)
• ANAD Reg 385-29 (Cranes, Hoists, Cables, Ropes and Slings)
Using these regulations, management performs a documented safety inspection of work areas monthly, making safety observations in order to identify workplace hazards and keep team members safe. Additionally, managers select employees to learn their opinions on safety in their work areas. Management is committed to making the depot the safest workplace it can be. Team members can view the new ANAD regulations on the Intranet under ANAD Regulations.
Social Sharing