
Innovative technology and associated system performance improvements are laudable goals to pursue, but success of a system is also measured by how well, how long and how efficiently they serve the Soldier over time.
Armament system developers must consider all factors that could undercut readiness and increase sustainment or “supportability” costs. Identifying these supportability and cost burdens, which are rooted in early design decisions, is paramount for the success of a system.
From a cost perspective, it’s critical to “design out” potential supportability problems since about 60–80 percent of the life cycle cost of a system is incurred during the operations and support phase of the life cycle.
In an effort to minimize large operations and support costs, the U.S. Army Combat Capabilities Development Command Armaments Center (CCDC AC) has taken a fresh look at how we design armament systems during the early phases of the acquisition life cycle, evaluating various options to provide an overall system solution.

According to logistics training material from Defense Acquisition University, operations and support costs may include those associated with:
- Software updates and upgrades.
- Protection against cyberattacks.
- Hardware repair overhaul, reset and retrograde.
- Data conversion and cleaning.
- Software and hardware obsolescence mitigation.
- Demilitarization and disposal.
- Facility modifications for training, maintenance and storage.
- Tools and equipment for repair and maintenance.
- Training.
A 2003 report by the Government Accountability Office focused on weapon system total ownership costs. It determined that up to 90 percent of these operations and support costs are locked in by the time a product is developed and ready for production.
Even though this report is somewhat dated, we still believe it is relevant to today’s acquisition life cycle. For ammunition and associated items (Supply Class V), operations and support costs are believed to be less, but still a significant portion of the overall life cycle costs because of several different factors—for example, you cannot get back spent bullets. Additionally, ammunition usually doesn’t have parts that require scheduled maintenance, repairs or upgrades. These costs have a huge impact on the ability to sustain fielded systems.
The CCDC AC has introduced several initiatives that will drive engineers and scientists toward identifying and addressing supportability issues at an early stage. The goal is to “design out” these issues or, at the very least, properly identify these issues as risks to our stakeholders and to our partners who will receive this technology and mature it further for production.
Realistic planning and resourcing can be achieved by program managers when the science and technology community can identify supportability risks before transition, thus ensuring successful programs and eventual fielding of the capabilities.
SUPPORTABILITY SPECIALISTS
One initiative is the Science and Technology Supportability Cell at the Armaments Center, which was established in 2017 and currently has a staff of six people. This group’s mission is to assess emerging armament system designs for any supportability issues and opportunities across all science and technology efforts. The cell does this by using various personnel, processes and tools to identify, analyze and evaluate supportability implications.
This cell comprises of supportability project officers, who have various engineering and life cycle logistics backgrounds and a capability to apply their knowledge and experiences in the abstract. That would entail taking designs of potential systems and envisioning how they will be used and function if they were fielded now, and extracting from that concept the impacts or considerations needed so that it can be supported. Before being integrated into science and technology projects, the Science and Technology Supportability Cell conducts an assessment of the projects within the portfolio to identify the major projects that have the strongest needs for supportability analyses and improvements.
These supportability project officers provide the initial assessment and identify necessary follow-on tasks, taking the burden off of the project lead. They serve as the single point of contact for all supportability related tasks. These tasks detail the specific assessments, analyses and evaluations necessary to address supportability concerns, implications and opportunities. The tasks are then given to the project lead for inclusion into the overall project plan. An internal document at CCDC AC provides guidance to project leads on how to assemble a team and what tasks the project lead is responsible for—it guides the leads in the steps of project initiation and management. In situations where resources are not available to fully analyze or mitigate the supportability concerns, someone is designated to track the risks associated with a project and include them in a risk profile, so the project lead can focus on the project as a whole.
These assessments provide the entire project team insight into cause-and-effect relationships between certain design decisions and the potential impact to the Soldier and the Army infrastructure. To accomplish their objectives, supportability project officers use various engineering tools and techniques such as risk analysis, failure modes and effects analysis, and supportability analysis.
In addition to these tools, supportability project officers have access to some totally new and unique tools, such as the Logistics Map (LOGMAP) and the Life Cycle Impact Analysis Tool that were developed by the Armaments Center as part of separate initiatives.
The LOGMAP adds value to the project management process used at CCDC AC, the Armaments Technology Development Process, by providing guidance to the life cycle engineering community on recommended actions and analyses that should be done at specific times within the process.
LOGMAP identifies when specific actions should be taken in relation to other project tasks, allowing logistics engineers and logisticians to synchronize their actions with those of the other project engineers. It allows for the development of a supportability road map within the science and technology environment for each project. It provides guidance to supportability project officers with respect to the high level “how, what and when” actions that should be taken.

ASK THE RIGHT QUESTIONS
The Life Cycle Impact Analysis Tool is a software-based tool that helps supportability project officers and project team members identify potential supportability and cost burdens by answering a series of questions. It “speaks” to the design engineers, asking questions on intricate design details that have a profound impact on the eventual support needed for the system rather than asking basic “compliance” questions. Currently, the tool contains more than 500 questions that were derived from several logistics-based references such as Product Support Manager Guidebook, Independent Logistics Assessment—a document used to analyze the supportability planning of a program—and Army Regulation 700-127 “Integrated Product Support”. Furthermore, experts and lessons learned helped take the information contained in the reference documents and tailor which questions should be answered, to better be in line with what projects should be looking for. Example questions include:
- Does this technology require new maintenance skill sets and levels?
- Does this technology application require facility modifications such as handling, storing, operating or maintenance?
- Is nonstandard test equipment needed for this technology?
- Does this technology require special handling equipment or other enablers to use?
- Does the design optimize the use of common parts and material and minimize the use of peculiar or unique parts within the system?
- Does this technology application require standard personal protective equipment for using or maintaining the technology?
- Does the technology require a power source?
- Does this technology require a humidity controlled environment for storage?
These example questions are simple and relatively straightforward but are often overlooked during early design development. In addition, these questions can be customized to include additional detail for a more specific situations.
The questions contained within Life Cycle Impact Analysis Tool are all encompassing and touch on all 12 of the integrated product support elements. These questions help drive discussion and identify potential supportability burdens. The tool takes it a step further, providing a qualitative analysis based on answers to the questions.
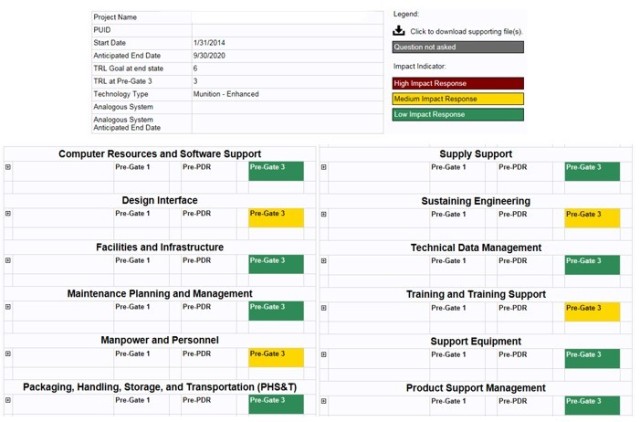
The tool uses the answers to these questions to assess “high,” “medium” and “low” impact to sustainment. These impacts then help derive associated risks so that plans can be developed to mitigate, eliminate or track. The tool provides an iterative process to analyze alternatives for design, to assess risks at each stage of the project and to provide valuable input to Life Cycle Sustainment Plans. The tool is intended to be ever-evolving, allowing for questions to be refined and customized based on lessons learned.
There have been several early successes in the implementation of LOGMAP, the Life Cycle Impact Analysis Tool and supportability project officers. In one situation, a design review revealed potential issues with maintenance and cleaning and with supply of barrel shroud components for a weapon system in development. The supportability project officer identified several implications with the design, recommending that the team explore the use of 3-D printing to produce a better geometric venting design of the shroud, which would be easier to maintain and would reduce the need for additional spare parts.
Additionally, the 3D printed solution would also reduce materiel costs of the component, providing an inexpensive alternative to the initial design.
In another situation, during a product design review for the development of a rifle fire-control system, the supportability project officer identified potential issues with the placement of the control housing unit, which contains the software and associated components to operate the system, and its impact on other components.
The supportability project officer recommended that the team obtain user feedback gathered for other, comparable fielded systems to explore different design options that would minimize wear on the other system components.
With the integration of supportability project officers onto science and technology projects and the use of these newly developed tools, CCDC AC has taken the first step toward making supportability an integral part of development and providing best value solutions to our customers.
These initiatives provide the engineering community with a broader sense of the effect that the capabilities they are developing will have on total ownership cost, on the logistics footprint, and on readiness, thus providing greater fidelity to the trade space and ensuring the best value solution is selected. They provide another means of ensuring availability of future systems for the Army.
CONCLUSION
An emphasis on supportability helps to ensure that a system can have a long and effective life in the field and reliably support Soldiers in achieving their mission objectives. The costs associated with mitigating supportability issues later in the life cycle can be prohibitive and time-consuming, thus hindering readiness. Keeping supportability at the forefront of early system development can require some adjustment in thinking, but the benefits are clear and compelling.
For more information, go to https://ac.ccdc.army.mil/organizations/esic/LRED/.
CHRISTOPHER APPLEGATE is deputy director of the Logistics Research and Engineering Directorate (LRED), where he helps shape efforts within the organization to meet strategic objectives. He holds a Master of Engineering in systems engineering from Stevens Institute of Technology and B.S. in mechanical engineering from Wilkes University. He is a member of the Army Acquisition Corps (AAC).
JOSEPH CANNATARO is the competency manager of the Life Cycle Supportability Division (LCSD) within LRED. He manages a team of engineers and other professionals responsible for identifying, analyzing, developing and managing supportability considerations for weapon system programs. He holds an MBA from the Florida Institute of Technology, a B.S. in electrical engineering from the New Jersey Institute of Technology, and various certificates in leadership and management. He is a member of the AAC.
CHIA W. “JEFF” LEE is the associate director for supportability integration, supervisory for the Science and Technology Supportability Cell, and the supportability project officer on the Extended Range Cannon Artillery project. He manages a team of supportability project officers to support many science and technology projects and coordinate supportability analysis and design activities early in the life cycle. He holds an M.E. in systems engineering from the Stevens Institute of Technology, a B.S. in industrial engineering from Rutgers University, and is a certified internal auditor for ISO9000 and CMMI quality management frameworks. He is a member of the AAC.
Read the full article in the Summer 2020 issue of Army AL&T magazine.
Subscribe to Army AL&T – the premier source of Army Acquisition news and information.
Social Sharing