As global competition continues to drive business innovation, industry in both the public and private sectors is continually looking for opportunities to achieve efficiencies. Persistent budget considerations, coupled with the need for a high quality product, have forced operations of all sizes to take a hard look at current operations in an attemp
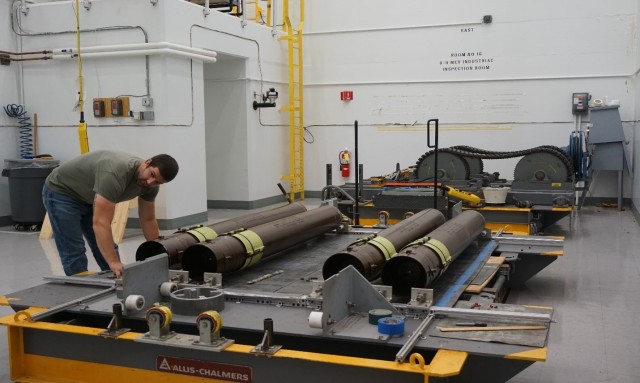
VIEW ORIGINAL
t to streamline their business. A potential area for reform that has recently garnered attention is conventional testing practices, specifically how those practices affect quality and cost-control measures. A potential solution to this efficiency deficit is the application of Non-Destructive Testing.
NDT provides the ability for an evaluator to test components of a system without altering the article being examined. Often offering significant cost saving and logistical advantages, NDT safely ensures proper equipment operation without the damage that can occur during other traditional means of testing. The Joint Munitions Command has recognized these advantages in the NDT process and is looking to expand its use to better serve the Joint Warfighter.
To do this, JMC has compiled an Integrated Planning Team comprised of personnel from JMC Headquarters, Rock Island, Ill.; Letterkenny Munitions Center, Chambersburg, Pa.; Crane Army Ammunition Activity, Crane, Ind.; and McAlester Army Ammunition Plant, McAlester, Okla.; in order to synchronize training/certifications, maintenance, modernization and manning. This IPT integration allows affected installations critical access and input into the process. Validating the quality and reliability of munitions within the JMC enterprise creates a more streamlined process and incorporates individual installation leadership into the planning process.
JMC will also leverage an indefinite-delivery, indefinite-quantity contract. IDIQ provides for an indefinite quantity of services for a fixed time. These contracts are applied when the government cannot determine, above a specified minimum, the precise quantities of supplies or services that the government will require during the contract period. IDIQs help streamline the contract process and speed service delivery.
The known cost across the enterprise will be in preventive maintenance for the current IDIQ equipment available in JMC. All other “unknown” associated costs will be executed through a delivery order set up by each installation. Delivery Orders would be placed according to each installation’s requirement and be tied directly to that installation, rather than the stand-alone contract. Quantity limits/ceiling may be written as number of units or dollars and each installation will help determine quality limits/ceilings based on their DO requirements.
Ultimately, this process could save JMC a substantial amount in modernization funding by allowing continuous lifecycle and technology upgrades to JMC’s NDT equipment. These upgrades would extend equipment lifespan and positively affect the program’s bottom line.
JMC is currently working the contact specifics to address these issues with consideration given to installation requirements and input. Remaining sensitive to the unique mission requirements that drive varying equipment and training needs, JMC is working diligently to address cost drivers as parameters are being developed.
Always driving toward new and innovative process improvements is what allows the Department of Defense to increase its readiness capabilities. Identification and implementation of new technologies and operational practices, such as these, are how our Joint Warfighters remain equipped with the munitions they need to provide lethality that wins.
Social Sharing