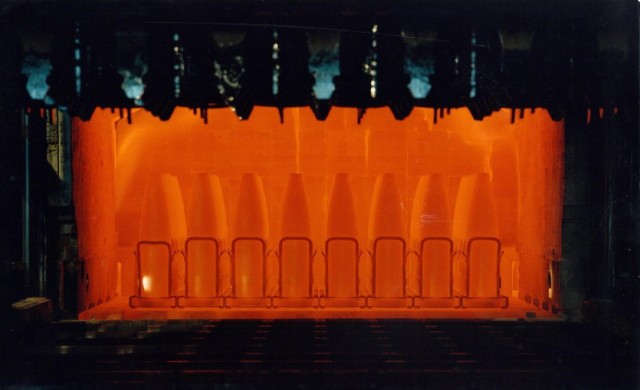
Scranton Army Ammunition Plant manufactures and ships large-caliber ammunition metal parts to be loaded, assembled, and packed at several facilities in the U.S. The metal parts produced at SCAAP range in size from 105mm to 155mm projectiles. Variations in type of projectiles that could be produced include the 120mm mortar family, the 5-Inch 54-Caliber Navy Gun projectile body and the 105mm projectile.
All projectiles manufactured at SCAAP go through a rigorous inspection process at every stage of their production which begins when the billets are initially forged into metal tubes. The tubes produced at the forging process are hot inspected at temperatures near 1,700 degrees to ensure proper internal and external dimensioning. The metal tubes are then cooled on an underground conveyor system where they remain for four hours in order to cool to room temperature. Once cooled they are cold inspected to verify their internal and external dimensions remained consistent. The tubes go through a series of machining operations which begins their transformation to a projectile where the nose is pressed onto the tube during the nosing operation. The projectiles will then be heat treated, final machined to exacting dimensions, painted and shipped.
SCAAP has modernized and improved the facility and its infrastructure to support expanded production capabilities, such as, the 155mm production line enhancement project which increased manufacturing capacity on that line from 12,000 to 15,000 rounds per month. This initiative assists in ensuring SCAAP can support the battle rhythm of our Load, Assemble and Pack (LAP) facility at the Iowa Army Ammunition Plant. Additional modernization efforts completed to increase production include: the Billet Saw Cell (which increased capacity while reducing the number of operators required to operate it), the Erie I and Bliss I Forge Press Quick Die Change projects (which reduced change-over time from one product to another from 18-24 man-hours to two to four man-hours, this enables a more efficient and seamless transition from one projectile to another with minimal interruption).
SCAAP works closely with its customers and LAP counterparts to ensure every projectile shipped from the plant meets the requirements from full-form thread length on the nose threads to projectile dimensions measured in thousandths of an inch. SCAAP produces and ships projectiles to two Organic Industrial Base Facilities within JMC. Iowa AAP receives more than 12,000 155mm projectiles every month for LAP operations. Crane Army Ammunition Activity LAP’s the 5-inch 54-caliber Navy Gun projectile.
SCAAP also provides research and development capability for emerging projectile requirements through the Department of Defense Ordnance Technology Consortium, which brings together the Joint Program Executive Office Armaments & Ammunition, the Army’s Combat Capabilities Development Center and the Long Range Precision Fires Cross Functional Team.
JMC, Joint Program Executive Office, SCAAP and Medico Industries, and their subcontractor General Dynamics Ordnance and Tactical Systems work collaboratively to ensure that SCAAP remains capable of sustaining the Joint Warfighter through industry leading manufacturing capability.
Social Sharing