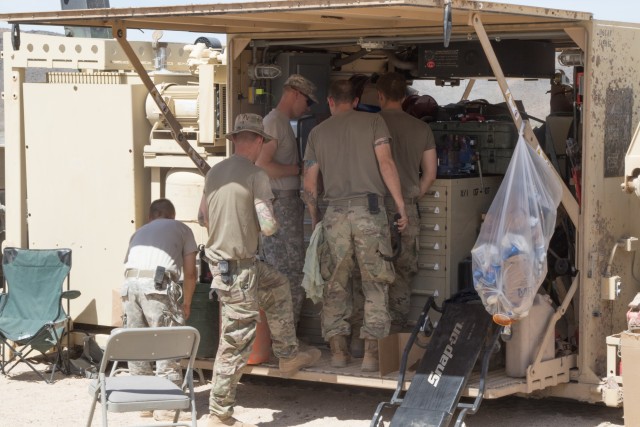
Two teams from Army Contracting Command-Rock Island’s intern homeroom (IHR) are supporting the Joint Manufacturing and Technology Center (JMTC) by working on several contracts for the Forward Repair System (FRS).
According to JMTC, the FRS is a mobile, self-contained repair shop designed to perform field-level repair and maintenance on major combat systems like the Abrams tank and Bradley Fighting Vehicle. It is comprised of several subcomponents including a Palletized Load System (PLS) flatrack, onboard crane, air compressor, generator, welder and hand tools.
This year, JMTC is commemorating 20 years of FRS production within its factory.
“The whole thing is a repair shop on wheels,” said Carrie Lansing, contracting officer. “What we are doing is helping support JMTC build new ones, but then they also have a requirement to refurbish old ones, so that’s why we have a couple of service contracts to work on the generators or the air compressors that are a part of the system.”
The FRS contract is set up as an Indefinite Delivery/Indefinite Quantity (IDIQ) contract. However, FRS requires a variety of contract methods, and the majority of the contracts are done through commercial purchase orders.
The FRS contracts are being worked on by two IHR contracting teams under the direction of contracting officers, Lansing and Anna Whitcomb. The contract specialist interns are Kaci Christensen, Andrea Garcia, Cole Harris, Whitney Jansen, Mika Mahyenga, Noel Reilly, Rabekah Stone, Michael Thune and Zane Viernow.
Each specialist has different roles in completing this contract. Whitcomb says that this contract is a great “learning tool” for the interns because, “we’re doing new purchase orders or new delivery orders every time, they are getting the repetitive process with each new requirement so they get to see a buy from start to finish,” said Whitcomb.
Stone said working on two contracts for the FRS from scratch has been a valuable and rewarding experience.
“Completing these requirements honestly hasn’t been the smoothest process, and there have been twists and turns along the way,” said Stone. “The most rewarding aspect of working on the FRS contract is knowing the difference these systems will make on Soldiers once they’re completed. I feel a sense of ownership.”
The interns noted the FRS requirement involves working with several different point of contacts (POCs), which provided a good opportunity to learn how to obtain bits of information from different areas and piece them all together to gain a complete requirements package.
“Working the JMTC’s FRS requirement was extremely beneficial for myself, and everyone on my team,” said Harris.
Since moving the JMTC FRS contract into the IHR, they have been able to successfully address some post-award problems that had been previously encountered. Though the customer is based on Rock Island Arsenal, it was sometimes hard to tell if everything had been completed because JMTC is such a large organization.
Lansing said once the FRS program was brought into the homeroom, they began working with JMTC to restructure the way workload was sent to ACC-RI – aligning the contracting personnel to specific programs so they work with the same program manager.
“Prior to that, there was not really a set way in which requirements were received and there were multiple POCs,” said Lansing. “Now that we have more of a team approach with them, I think it has really helped because we have built that relationship with the people specifically working the FRS program.”
Social Sharing