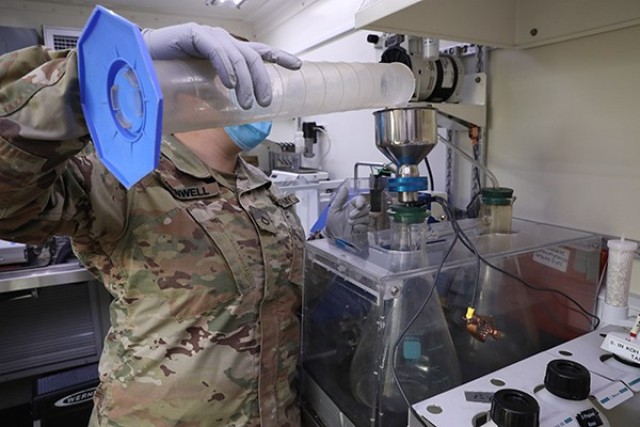
FORT STEWART, Ga. — Soldiers from the 135th Quartermaster Company, Special Troops Battalion, 3rd Infantry Division Sustainment Brigade, recently recertified their B-1 status, giving the fuel lab technicians the authorization to conduct the basic checks of petroleum, oils and lubricants.
Fuel lab technicians provide a necessary service to Fort Stewart and Hunter Army Airfield by distributing the bulk fuel that keeps the Army’s premier armored division rolling and aircraft flying.
They are also preparing to reach the highest level of the Army Certification for petroleum in, B-2, which will give them the authorization to conduct full systems checks and their capabilities.
The Petroleum laboratory specialists of the 135th QM Co. play a key part in the fuel distribution system ensuring that the fuel is to the highest standard. They are responsible for conducting laboratory fuel sampling tests on petroleum, oils and lubricants to ensure that the POL distributed by the company meets the quality, durability and purity required to ensure the safe operation of Army equipment.
“[The fuel lab] is a division asset supporting all of 3rd ID with clean POL to ensure that the Army keeps rolling along as well as flying high,” said Warrant Officer 1 Nathan Huston, petroleum systems technician with 135th QM Co. “Being the only fuel lab on Fort Stewart, we also get tasked with supporting groups such as the Task Force 1st Battalion, 28th Infantry and 160th Special Operations Aviation Regiment.”
The fuel lab tests fuel out of the commonly used POL equipment including Heavy Expanded Mobility Tactical Trucks, 5k Tankers, Tank Rack Modules and Tank and Pump Unit. These tests are conducted daily so that military occupation specialty 92L Soldiers - petroleum laboratory specialists - will know the specifications of the fuel.
“There are two tests that we perform on a daily basis, a visual test and a particulate contamination test,” said Pfc. Lorissa Cornwell, a petroleum laboratory specialist with 135th QM Co. “It gets challenging at times being the only 92L in the company, but I am thankful for the Soldiers that come to help out with as much as they possibly can without being a 92L.”
Petroleum supply specialists with 135th QM Co. get the opportunity to assist the 92L’s with their daily responsibility of ensuring that Soldiers are issuing the cleanest fuel possible, not only throughout the 3IDSB, but throughout Fort Stewart and Hunter Army Airfield.
“Just like any new experience it was challenging and unfamiliar, but I was ready to step up to complete the mission,” said Sgt. Raawban Broussard, noncommissioned officer-in-charge of the POL lab with 135th QM Co. “Over time, the 92L taught me the most by showing me the rules and regulations of the POL lab operations. I learn more and more daily which helps to complete the mission.”
The fuel lab conducts more than 100 tests of POL each month. The lab is certified by the Army Petroleum Center, which gives the authority and rights to perform their testing capabilities. The 135th’s Hazardous Material team plays a huge role along with the fuel lab. HAZMAT provides the lab with the proper storing and disposal of the POL.
“The POL and chemicals that we use are very buoyant and have to be stored and disposed of in a certain way for environmental considerations.” Broussard said.
The key to the unit’s success in supporting the division is cooperation between the various fuel handling specialties and the customers to ensure that the highest quality product is being delivered and the units being supported are capable of conducting their missions.
“It takes a lot of attention to detail while operations and testing are going on,” Broussard said. “Maintaining our discipline and teamwork, we are confident to continue keeping everything rolling”
Social Sharing